How are Pipe Flanges Manufactured?
1. Introduction to Pipe Flanges
Pipe flanges are essential components used to connect sections of pipes or hoses, providing a leak-proof seal and allowing for easy maintenance, inspection, and modification in various industries. A pipe flange is a disc-shaped fitting with holes that align with matching holes on the pipe or equipment, allowing for the insertion of bolts to hold the assembly together securely.
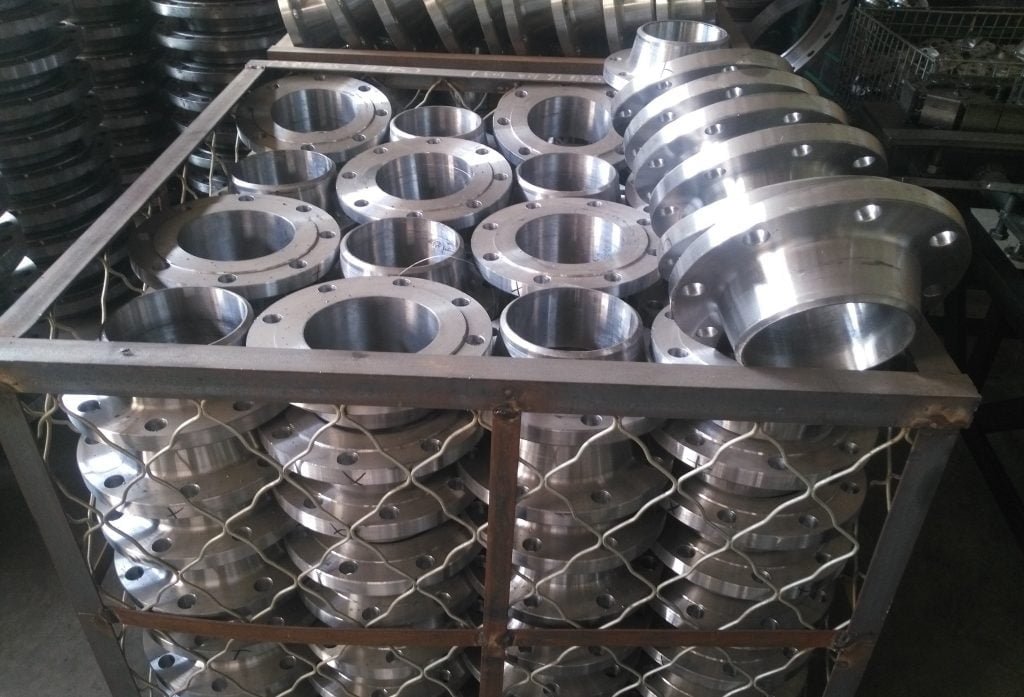
Pipe flanges play a critical role in industries such as oil and gas, petrochemicals, power generation, water treatment, pharmaceuticals, and many more. They are used to join different sections of pipelines, connect valves, pumps, and other equipment, and facilitate the efficient and safe flow of fluids, gases, and solids.
Flanges ensure the integrity and reliability of piping systems, preventing leaks, pressure loss, and other hazards that can have detrimental effects on operations and safety. With their versatility and adaptability, pipe flanges enable easy installation and disassembly, saving time and costs during maintenance and repairs. Their importance in ensuring the efficiency, reliability, and safety of industrial processes cannot be overstated.
Stay tuned for the next section, where we will delve into the manufacturing process of pipe flanges and highlight the expertise of Hebei Yanhao Pipeline Equipment Co., Ltd. in producing high-quality flanges for various applications.
2. The Manufacturing Process of Pipe Flanges
2.1 Material Selection
In pipe flange production, the selection of materials is crucial to ensure the durability, strength, and compatibility of the flanges with the respective piping systems and operating conditions. Three commonly used materials for pipe flanges are stainless steel, alloy steel, and carbon steel.
- Stainless Steel: Stainless steel is a popular choice for pipe flange manufacturing due to its excellent corrosion resistance, high tensile strength, and heat resistance. This material is suitable for applications where hygiene, cleanliness, and resistance to harsh environments are critical factors. Stainless steel flanges are widely used in industries such as food and beverage processing, pharmaceuticals, chemical plants, and offshore oil and gas.
- Alloy Steel: Alloy steel flanges are composed of various alloying elements such as chromium, molybdenum, nickel, and vanadium. These alloys enhance the flange’s mechanical properties, including higher strength, toughness, and resistance to high temperatures and pressures. Alloy steel flanges are commonly used in power generation plants, oil refineries, and petrochemical industries, where operating conditions require robust and reliable flange connections.
- Carbon Steel: Carbon steel flanges are cost-effective and versatile options used in a wide range of applications. Carbon steel offers good strength, rigidity, and weldability, making it suitable for general-purpose flanges in industries such as water treatment, HVAC, plumbing, and infrastructure. Different grades of carbon steel, such as ASTM A105 and ASTM A350 LF2, are commonly used, depending on the specific requirements and operating conditions.
Hebei Yanhao Pipeline Equipment Co., Ltd. specializes in manufacturing pipe flanges from these materials, ensuring superior quality and performance. Our team of experts can provide guidance on material selection based on the application, budget constraints, and other project requirements. Stay tuned for the next section, where we will discuss the advanced manufacturing equipment used by our company.
2.2 Production Equipment
Hebei Yanhao Pipeline Equipment Co., Ltd. is equipped with state-of-the-art manufacturing equipment that allows us to produce high-quality pipe flanges to meet the diverse needs of our customers. Our advanced machinery enables precise and efficient fabrication processes, ensuring the reliability and performance of our flanges. Here are some of the key equipment utilized in our production facility:
- Hydraulic Machines: We employ hydraulic machines for tasks such as cutting, punching, and bending. These machines utilize hydraulic power to exert force, enabling accurate and controlled operations. Hydraulic presses and shearing machines facilitate the precise shaping and cutting of flange components, ensuring dimensional accuracy and quality.
- Bending Machines: Bending machines are essential for shaping flange materials into the required configurations, such as bends, curves, and angles. Our bending machines employ advanced technology and computer-controlled systems to achieve precise bending without compromising the integrity of the material.
- Forging Tools: Forging is a critical process for manufacturing flanges, especially in the case of alloy steel and carbon steel flanges. Our facility is equipped with efficient forging tools such as forging hammers and presses, which apply controlled force and heat to shape the raw materials into the desired flange shapes.
- CNC Machining Centers: Computer Numerical Control (CNC) machining centers are used for precision machining operations, achieving tight tolerances and high surface finishes. These machines are utilized for operations such as drilling, milling, and threading, ensuring the precise alignment of bolt holes and other critical features on the flanges.
- Heat Treatment Furnaces: Heat treatment is often required for certain types of flanges to enhance their mechanical properties and durability. We have advanced heat treatment furnaces that provide precise temperature control, allowing for processes such as normalization, annealing, quenching, and tempering to be carried out effectively.
By employing this advanced manufacturing equipment, Hebei Yanhao Pipeline Equipment Co., Ltd. ensures the production of flanges of the highest quality and integrity. Our commitment to utilizing cutting-edge technology enables us to meet the diverse demands of our customers and deliver products that exceed expectations. In the next section, we will discuss the quality control measures implemented in our production process.
2.3 Production Steps
Flange manufacturing involves various processes, including forming, machining, welding, and casting. Each process plays a crucial role in shaping and fabricating the flanges to meet specific design requirements. Here is a detailed explanation of these processes:
- Forming: Forming processes involve shaping the raw materials into the desired flange configuration. This can be achieved through methods such as forging, rolling, or bending. Forging involves using heat and pressure to shape the material into the desired shape. Rolling processes use rollers to gradually shape the material into the desired dimensions. Bending involves using hydraulic or mechanical force to bend the material to the required angle or curve.
- Machining: Machining processes are employed to achieve precise dimensional accuracy, smooth surfaces, and tight tolerances on the flanges. CNC (Computer Numerical Control) machining centers are commonly used in flange manufacturing. These machines utilize computer-controlled systems to accurately cut, mill, drill, and thread the flange material. CNC machining ensures the precise alignment of bolt holes and other critical features, enhancing the overall quality of the flange.
- Welding: Welding processes are utilized to join flange components and create a secure and reliable connection. Various welding methods can be employed, including arc welding, TIG (Tungsten Inert Gas) welding, MIG (Metal Inert Gas) welding, and more, depending on the material and design requirements. Welding ensures the structural integrity and strength of the flange by creating a durable bond between the components.
- Casting: Casting processes are used to produce flanges from molten materials. The most common casting method for flanges is the investment casting process. In this process, a wax pattern of the flange is created, coated with a ceramic shell, and then heated to remove the wax and harden the ceramic shell. Molten metal is poured into the shell and allowed to solidify, forming the final flange shape. Casting allows for complex geometries and intricate designs to be achieved.
It is important to note that not all processes are used in the manufacturing of every type of flange. The selection of processes depends on factors such as the material, design specifications, and application requirements. Additionally, rigorous quality control measures are implemented throughout each process to ensure that the flanges meet the required standards and specifications.
Hebei Yanhao Pipeline Equipment Co., Ltd. possesses expertise in all these flange manufacturing processes, ensuring the production of high-quality flanges that meet customer requirements and industry standards.
2.4 Quality Control and Testing
At Hebei Yanhao Pipeline Equipment Co., Ltd., we understand the critical importance of maintaining stringent quality control measures throughout the manufacturing process. We are committed to delivering flanges of the highest quality and reliability to our customers. To achieve this, we employ various inspection techniques and utilize advanced inspection tools. Here is an overview of our quality control and testing procedures:
- Significance of Quality Control: Rigorous quality control measures are vital to ensure that the manufactured flanges meet the required standards and specifications. Quality control helps identify and rectify any deviations or defects in the production process, ensuring that only conforming flanges are delivered to customers. By adhering to strict quality control procedures, we can provide flanges that exhibit excellent performance, durability, and safety.
- Inspection Techniques: We employ a combination of visual inspection, non-destructive testing (NDT), and destructive testing techniques to assess the quality of our flanges effectively. Visual inspection involves a thorough visual examination of the flanges for any surface defects, such as cracks, scratches, or deformations. Non-destructive testing methods, such as magnetic particle testing (MPT) and X-ray testing, are utilized to detect subsurface defects and discontinuities that may not be visible to the naked eye. Destructive testing involves subjecting selected samples to controlled stress, such as tensile or impact testing, to evaluate the mechanical properties and strength of the flanges.
- Inspection Tools: We utilize advanced inspection tools and equipment to ensure accurate and reliable quality assessment. Magnetic particle testing (MPT) is used to detect surface and near-surface defects by magnetizing the flanges and applying ferromagnetic particles, which reveal any discontinuities. X-ray machines are employed for radiographic testing to examine the internal structure of the flanges and detect any hidden defects. Hardness testers are utilized to measure the hardness of the flange material, which is an important indicator of its mechanical properties and resistance to deformation.
Apart from these specific tools, we also employ various measuring instruments, such as calipers, micrometers, and gauges, to verify dimensional accuracy and ensure compliance with the required specifications.
These quality control and testing procedures, coupled with the utilization of advanced inspection tools, enable us to deliver flanges that meet the highest quality standards. Our commitment to quality control helps guarantee the performance, reliability, and safety of our products, instilling confidence in our customers and end-users.
3. Advantages of Hebei Yanhao Pipeline Equipment Co., Ltd.
3.1 Location Advantage: Hebei Yanhao Pipeline Equipment Co., Ltd. is strategically located in Cangzhou City, Hebei Province, which is known as China’s renowned flange industry hub. This advantageous location offers several benefits to our company and customers. We have easy access to a wide range of raw materials, suppliers, and skilled labor, enabling us to streamline production processes and reduce costs. Additionally, our proximity to major transportation networks facilitates efficient logistics and timely delivery of our flanges to customers worldwide.
3.2 Raw Material Advantage: We prioritize the use of high-quality raw materials in our manufacturing processes. We source steel from renowned suppliers such as Baogang Group, Laigang Group, and other trusted partners. These suppliers are known for their stringent quality control measures and consistently supply us with steel that meets international standards. By using premium-grade steel, we ensure that our flanges exhibit exceptional strength, durability, and resistance to corrosion.
3.3 Production Capabilities: At Hebei Yanhao Pipeline Equipment Co. Ltd., we have a robust production capacity to handle varying customer demands. Our advanced manufacturing facilities are equipped with state-of-the-art machinery and equipment. With a skilled workforce and efficient production processes, we can efficiently produce a wide range of flanges in various sizes, materials, and configurations. This capability allows us to handle both small and large-scale orders while maintaining high-quality standards and meeting tight delivery schedules.
3.4 Customization Capabilities: We understand that different customers have unique requirements. Therefore, we offer customization capabilities to provide tailor-made, non-standard flange products based on specific customer needs. Our team of experienced engineers and technicians works closely with customers to understand their requirements and develop customized flange solutions. From material selection to precise dimensional specifications, we ensure that the final product meets or exceeds customer expectations. Our ability to offer customized flanges distinguishes us as a flexible and customer-centric manufacturing company.
In the following section, we will elaborate on our commitment to environmental sustainability and highlight our initiatives to minimize the environmental impact of our manufacturing processes.
4. Conclusion
In conclusion, Hebei Yanhao Pipeline Equipment Co., Ltd. is strategically located in China’s renowned flange industry hub, allowing us to access a wide range of raw materials, suppliers, and skilled labor. We prioritize the use of high-quality steel sourced from reputable suppliers, ensuring that our flanges exhibit exceptional strength and durability. With our strong production capabilities and customization options, we can meet varying customer demands and provide tailor-made flanges based on specific requirements. Our commitment to superior quality and reliability sets us apart in the industry. Choose Hebei Yanhao Pipeline Equipment Co., Ltd. for high-quality pipe flange products that meet or exceed your expectations.
Author: Lewis Liu
Hello, my name is Lewis Liu, and I’m a professional sales engineer with over a decade of expertise in the flange fittings sector.
I am quite informed about flange selection, installation, and maintenance. I am passionate about providing customers with the greatest solutions for keeping their pipeline systems running smoothly, safely, and dependably.
If you have any queries or concerns concerning flange fittings for your pipelines, whether they are about selection, material choice, specification requirements, or anything else, please contact me at any time. I am dedicated to providing expert advice and assistance to help you make educated decisions and reach your objectives.
