Interpreting Flange Performance: Analysis of Flange Requirements in High-Pressure, High-Temperature Environments
I. Introduction
Hello, and welcome to YANHAO’s exploration of flange performance in challenging industrial environments. In the fast-paced realm of industrial applications, flanges play a pivotal role in ensuring seamless connectivity and operational reliability. As a cornerstone of various systems, flanges facilitate fluid flow, maintain structural integrity, and enable efficient maintenance practices.
Flanges serve as the unsung heroes, connecting pipes and components to form robust systems across industries. From petrochemical plants to power generation facilities, the importance of flanges cannot be overstated. They act as linchpins, providing the essential linkages that keep operations running smoothly.
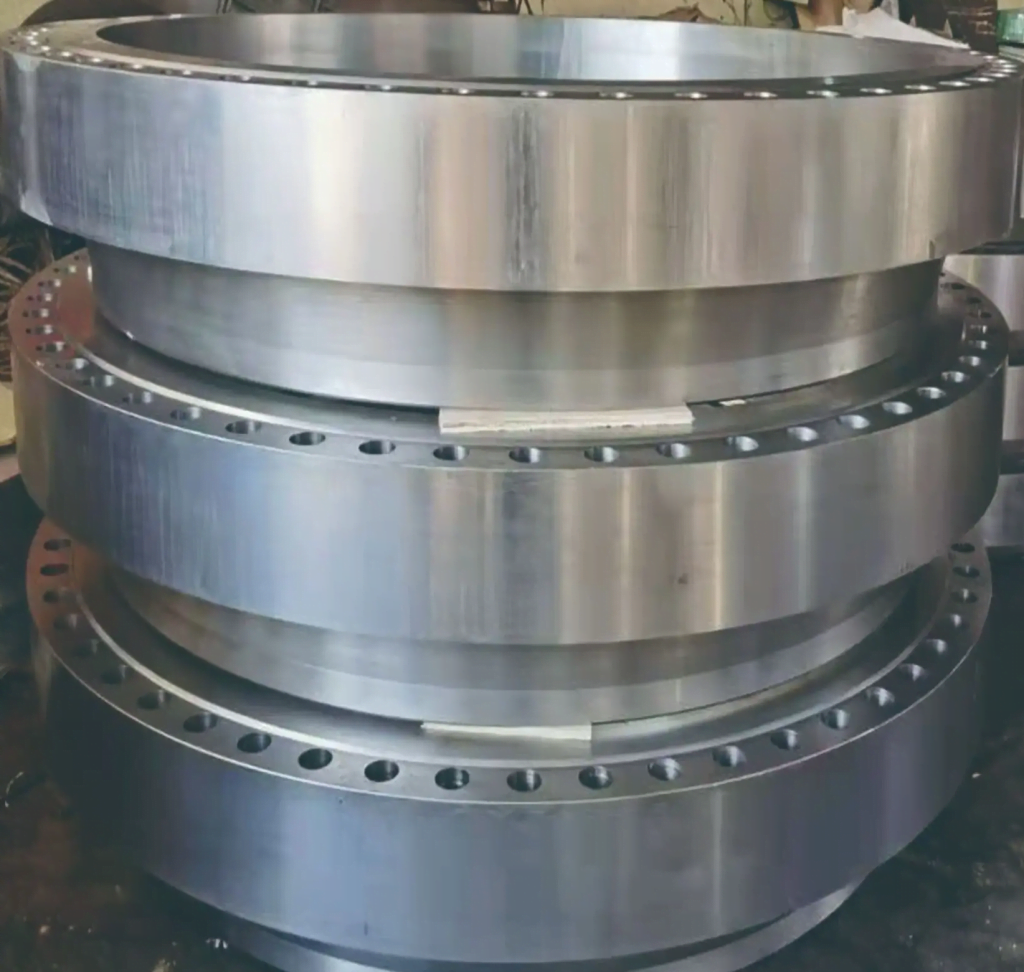
In the world of industrial engineering, high-pressure and high-temperature environments pose unique challenges. Flanges operating under such conditions are subject to extreme stresses and demanding conditions, requiring specialized design and materials to ensure optimal performance. Understanding these challenges is crucial for industries where precision and reliability are paramount.
The purpose of this blog is to delve into the intricacies of flange performance, particularly in high-pressure, high-temperature environments. YANHAO recognizes the need for a comprehensive understanding of the challenges posed by these conditions. Through insightful analysis and expert commentary, we aim to shed light on the factors influencing flange functionality, providing valuable knowledge for professionals seeking to enhance system resilience and efficiency. Join us on this journey as we unlock the secrets behind superior flange performance.
II. Understanding Flange Design
At YANHAO, we recognize the critical role that a detailed understanding of flange design plays in achieving optimal performance within industrial systems, especially when confronted with the challenges presented by high-pressure, high-temperature environments. Let’s delve into the intricacies of flange structure, explore the diverse types available, and underscore the meticulous design considerations essential for navigating the complexities of demanding operational conditions.
A. Basics of flange structure and functionality
Flanges are not mere connectors; they are the linchpins that ensure the integrity of industrial systems. Understanding the nuances of flange structure is imperative for comprehending their functionality. Flanges feature a disc-like structure with evenly spaced holes for bolts, providing a secure connection between pipes and equipment. Beyond this basic design, it’s crucial to delve into how flanges function, supporting fluid flow, distributing loads evenly, and enabling efficient maintenance practices. This section will provide a detailed exploration of the fundamental principles governing flange structure and functionality, offering a solid foundation for further comprehension.
- Structural Anatomy of Flanges:
- Disc-like Architecture: Flanges, at their core, feature a distinctive disc-like structure with meticulously crafted dimensions.
- Bolt Hole Arrangement: Understanding the evenly spaced holes for bolts is pivotal to comprehending the secure connection that flanges provide within industrial systems.
- Functional Dynamics of Flanges:
- Fluid Flow Facilitation: Delve into how flanges serve as conduits for fluid flow, ensuring a seamless and efficient transfer within pipelines.
- Load Distribution Mechanisms: Explore the role of flanges in evenly distributing loads, contributing to the overall stability and resilience of interconnected components.
- Maintenance Efficiency: Uncover the ways in which flanges play a key role in facilitating efficient maintenance practices, crucial for sustained operational excellence.
B. Types of flanges and their applications
YANHAO acknowledges the diverse requirements across industrial applications, necessitating various flange types tailored to specific tasks. Let’s delve deeply into the characteristics and applications of each flange type. The slip-on and weld neck flanges, widely used for their versatility, will be examined alongside specialized options such as lap joint and socket weld flanges. Each type serves a unique purpose, and this section aims to provide a comprehensive overview, empowering industry professionals with the knowledge needed to make informed decisions about flange selection for specific applications.
- Slip-On Flanges:
- Versatile Adaptability: Explore how slip-on flanges, known for their ease of installation, find versatile applications across a spectrum of industries.
- Sealing Mechanisms: Delve into the unique sealing mechanisms of slip-on flanges, contributing to their efficiency in various operational contexts.
- Weld Neck Flanges:
- Enhanced Structural Integrity: Understand the structural advantages of weld neck flanges, particularly their ability to withstand high-stress environments.
- Critical Applications: Uncover the critical applications where weld neck flanges excel, emphasizing their prevalence in industries demanding robust performance.
- Lap Joint Flanges:
- Easy Dismantling: Examine the distinctive feature of lap joint flanges—easy dismantling—that caters to industries requiring frequent modifications and adjustments.
- Applications in Piping Systems: Learn about their specific applications within piping systems, showcasing their adaptability in diverse scenarios.
- Socket Weld Flanges:
- High Pressure Resilience: Explore how socket weld flanges, designed for high-pressure applications, contribute to the reliability of systems in demanding environments.
- Precision Connections: Understand the precision in connections offered by socket weld flanges, ensuring leak-free performance in critical operations.
By providing this in-depth overview, our aim is to empower industry professionals with the nuanced understanding needed to align flange selection with specific applications. Whether it’s the adaptability of slip-on flanges, the structural robustness of weld neck flanges, the flexibility of lap joint flanges, or the precision of socket weld flanges, YANHAO ensures that you have the insights required to make informed decisions, fostering efficiency and reliability in your industrial systems.
C. Importance of proper flange design in challenging environments
In an era where industries frequently operate in harsh conditions, the significance of meticulous flange design cannot be overstated. Flanges operating in high-pressure, high-temperature environments face severe stress, requiring careful consideration of various design aspects. This section will conduct an in-depth analysis of critical elements in proper flange design. From the selection of materials based on environmental demands to considerations of structural integrity and the implementation of effective sealing mechanisms, we will explore how each facet contributes to the resilience and durability of flanges in challenging environments. This detailed exploration aims to serve as a comprehensive guide for engineers and decision-makers, equipping them with the insights needed to navigate the intricacies of designing flanges for demanding operational conditions.
- Material Selection:
- Environmental Adaptability: Examine the crucial role of material selection in tailoring flanges to specific environmental conditions.
- Corrosion Resistance: Understand how materials are chosen to resist corrosion, a pivotal consideration in environments where corrosive elements pose a threat.
- Structural Integrity:
- Withstanding Stress and Pressure: Explore the engineering considerations involved in ensuring the structural integrity of flanges, particularly in high-pressure scenarios.
- Temperature Resilience: Delve into how the design accounts for temperature variations, ensuring that flanges maintain their integrity under extreme heat conditions.
- Sealing Mechanisms:
- Ensuring Leak-Free Performance: Examine the implementation of effective sealing mechanisms, a critical element in preventing leaks and maintaining operational efficiency.
- Adaptability to Dynamic Conditions: Understand how these sealing mechanisms adapt to dynamic changes, offering consistent performance in fluctuating operational environments.
This detailed exploration serves as a comprehensive guide, equipping engineers and decision-makers with the insights needed to make strategic choices in the design of flanges. By understanding the interconnected role of material selection, structural integrity, and sealing mechanisms, industry professionals can navigate the challenges of demanding operational conditions with confidence. YANHAO is committed to fostering excellence in industrial systems by providing the knowledge necessary to design resilient and durable flanges that stand up to the rigors of challenging environments.
III. Challenges in High-Pressure, High-Temperature Environments: Navigating the Rigors of Extreme Conditions
Operating within high-pressure, high-temperature environments poses unique challenges to flange performance. In this section, we delve into the specific hurdles faced, addressing the impact on material integrity and durability, thermal expansion considerations, and the challenges posed by corrosion and erosion. YANHAO is dedicated to providing a nuanced understanding of these challenges, offering insights that will aid engineers and decision-makers in enhancing the resilience of flanges operating in such demanding conditions.
A. Impact on Material Integrity and Durability:
In the realm of high-pressure environments, flanges undergo significant stress and fatigue, presenting challenges to their material integrity and long-term durability. This subsection delves into the intricacies of these challenges, offering insights into the effects of extreme stress and fatigue on flange materials, and emphasizing strategic material selection as a key factor in ensuring resilience in the face of demanding mechanical forces.
- Extreme Stress and Fatigue:
- Unveiling the Forces: Explore the intense mechanical forces exerted on flanges in high-pressure environments, contributing to stress accumulation over time.
- Long-Term Impact: Delve into how prolonged exposure to extreme stress levels can lead to fatigue, potentially compromising the structural integrity of flange materials.
- Material Selection Strategies:
- Tailoring Materials to Conditions: Examine the strategic considerations behind selecting materials capable of withstanding high-pressure scenarios.
- Resilience Criteria: Explore the criteria for material resilience, including factors such as tensile strength, corrosion resistance, and fatigue endurance, crucial in ensuring the longevity of flanges.
By navigating through the impact of extreme stress and fatigue on flange materials, and delving into the strategic considerations guiding material selection, this section aims to equip professionals with a profound understanding of the challenges posed by high-pressure environments. YANHAO recognizes the importance of material integrity and durability in sustaining optimal flange performance, and we are committed to providing actionable insights for industry experts to make informed decisions in their material selection processes.
B. Thermal Expansion Considerations:
In the demanding landscape of high-pressure, high-temperature environments, thermal expansion emerges as a critical factor influencing flange performance. This section meticulously examines the challenges posed by dynamic temperature variations on flanges, emphasizing the substantial impact of thermal expansion. Additionally, we delve into innovative engineering solutions designed to mitigate these effects, ensuring the structural stability of flanges in environments characterized by significant temperature fluctuations.
- Dynamic Temperature Variations:
- Understanding Thermal Dynamics: Delve into the intricate dynamics of temperature variations within high-pressure environments, gaining insights into how these variations directly impact the materials and structure of flanges.
- Challenges Posed by Thermal Expansion: Explore the challenges introduced by thermal expansion, including dimensional changes and increased stresses on flanges, and understand the implications for their long-term performance.
- Engineering Solutions:
- Material Engineering:* Examine the advancements in material engineering aimed at minimizing the impact of thermal expansion on flanges. This includes materials with specific coefficients of thermal expansion to enhance adaptability.
- Innovative Design Approaches:* Explore cutting-edge design approaches, such as the incorporation of expansion joints and flexible connectors, intended to accommodate thermal expansion while maintaining the structural integrity of flanges.
By elucidating the intricacies of thermal expansion challenges and presenting forward-thinking engineering solutions, this section aims to empower professionals with the knowledge needed to address this critical aspect of high-pressure, high-temperature environments. YANHAO is committed to facilitating informed decision-making, ensuring that flanges not only withstand dynamic temperature variations but also uphold structural stability for sustained performance in challenging operational conditions.
C. Corrosion and Erosion Challenges:
In the realm of high-pressure, high-temperature environments, the interplay of chemical reactions, corrosion, and abrasive erosion poses substantial challenges to the integrity of flanges. This section meticulously examines the nuances of these challenges, shedding light on the chemical reactions that induce corrosion and the abrasive forces contributing to erosion. Moreover, we explore proactive measures and protective strategies engineered to mitigate the detrimental effects of corrosion and erosion on flanges.
- Chemical Reactions and Corrosion:
- Environmental Impact: Examine the chemical reactions prevalent in high-temperature environments and understand how they contribute to corrosion challenges for flanges.
- Corrosion Mechanisms: Explore the mechanisms through which corrosion occurs, emphasizing the impact on flange materials and the potential consequences for long-term performance.
- Abrasive Erosion:
- Challenges in High-Pressure Environments: Understand how abrasive erosion becomes a prominent concern, particularly in high-pressure environments where the velocity of fluids intensifies the erosive forces.
- Protective Measures Against Erosion:* Explore advanced protective measures, including coatings and materials engineered to resist erosive forces, ensuring the longevity of flanges in challenging operational conditions.
By unraveling the complexities of corrosion and erosion challenges, and presenting strategic measures for protection, this section aims to equip professionals with the knowledge needed to safeguard flanges against environmental forces. YANHAO is committed to providing comprehensive insights that empower decision-makers to implement effective strategies, ensuring the durability and reliability of flanges in the face of corrosive and erosive challenges within high-pressure, high-temperature environments.
IV. Flange Performance Analysis: Decoding Excellence in Extreme Conditions
In this section, we embark on a thorough analysis of flange performance under extreme conditions. We’ll evaluate the resilience of flanges, examine successful applications through case studies, and delve into industry standards and compliance specific to high-pressure environments. YANHAO is committed to providing a comprehensive understanding of how flanges excel in challenging conditions, showcasing their reliability and efficiency.
A. Evaluation of Flange Performance Under Extreme Conditions:
In the crucible of extreme conditions, the performance of flanges undergoes rigorous evaluation to ensure resilience and reliability. This subsection scrutinizes the methodologies employed in stress testing flanges, examining how they perform in high-pressure and high-temperature environments. We’ll delve into the intricacies of resilience metrics, shedding light on considerations such as material integrity, dimensional stability, and long-term durability.
- Stress Testing Protocols:
- Simulating Extreme Environments: Explore the methodologies used in stress testing to replicate high-pressure and high-temperature conditions, mimicking the harsh operational environments flanges are likely to encounter.
- Identifying Thresholds: Understand how stress testing helps identify the thresholds at which flanges may exhibit signs of strain, allowing for preemptive measures to enhance their performance.
- Resilience Metrics:
- Material Integrity Considerations: Delve into the metrics that assess material integrity, ensuring that flanges maintain their structural strength and resist degradation in extreme conditions.
- Dimensional Stability Measurements: Explore how dimensional stability metrics contribute to evaluating the ability of flanges to maintain their shape and form under stress, preventing deformations that could impact performance.
- Long-Term Durability Criteria: Understand the criteria for long-term durability, encompassing factors such as fatigue resistance and corrosion resilience, crucial for sustained performance over the operational lifespan.
By navigating through stress testing protocols and resilience metrics, this section aims to provide professionals with a comprehensive understanding of how flanges are meticulously evaluated under extreme conditions. YANHAO is committed to transparency in the assessment of flange performance, ensuring that industry experts have the insights needed to make informed decisions in enhancing the resilience and reliability of flanges in demanding operational environments.
B. Case Studies Highlighting Successful Flange Applications:
In this section, we present real-world success stories that underscore the exceptional performance of flanges in various industries and challenging operational environments. These case studies offer concrete examples of how flanges have excelled, showcasing their resilience, reliability, and contribution to operational efficiency.
- Real-World Success Stories:
- Oil and Gas Exploration:
- Challenge: Operating in remote and harsh environments with extreme temperatures and pressures.
- Flange Solution: High-grade alloy flanges engineered for corrosion resistance and durability.
- Outcome: Significantly reduced maintenance frequency, ensuring uninterrupted operations in challenging conditions.
- Power Generation:
- Challenge: High-temperature conditions and thermal cycling in power plant piping systems.
- Flange Solution: Thermal expansion-resistant flanges designed with advanced alloys.
- Outcome: Improved structural integrity, minimizing the impact of temperature fluctuations on system performance.
- Chemical Processing:
- Challenge: Corrosive chemical environments leading to accelerated material degradation.
- Flange Solution: Corrosion-resistant coatings and material selection tailored to chemical compatibility.
- Outcome: Extended service life, reduced corrosion-related downtime, and enhanced safety.
2. Performance Metrics:
- Operational Efficiency Metrics:
- Reduced Downtime: Case studies highlight instances where flanges contribute to reduced downtime through enhanced reliability, minimizing disruptions to operations.
- Efficient Fluid Flow: Metrics showcase how well-designed flanges optimize fluid flow, improving overall system efficiency.
- Reliability Indicators:
- Consistent Performance: Examining cases where flanges exhibit consistent performance under extreme conditions, contributing to the reliability of the entire system.
- Minimal Maintenance Requirements: Highlighting instances where well-engineered flanges require minimal maintenance, reducing operational costs.
By presenting these tangible case studies and discussing the performance metrics that define their success, this section aims to provide practical insights for professionals. YANHAO is dedicated to showcasing the real-world achievements of flanges, empowering decision-makers to make informed choices and optimize their own operational processes based on proven success stories.
C. Industry Standards and Compliance in High-Pressure Environments:
In this section, we navigate the regulatory landscape governing flange design and performance in high-pressure environments. By exploring existing industry standards and regulations, as well as discussing compliance best practices, we aim to provide a comprehensive understanding of the measures essential for ensuring the quality and safety of flanges.
- Regulatory Landscape:
- International Standards: Delve into widely recognized international standards governing flange design, materials, and performance in high-pressure environments.
- National Regulations: Explore country-specific regulations that may further refine or supplement international standards, ensuring adherence to local safety and quality requirements.
2. Compliance Best Practices:
- Certifications and Testing Protocols: Discuss the significance of certifications, such as ISO, ASME, or API, and their role in validating that flanges meet or exceed industry standards.
- Quality Assurance Processes: Explore best practices in implementing robust quality assurance processes throughout the manufacturing and testing phases, ensuring consistent compliance.
- Documentation and Traceability: Emphasize the importance of thorough documentation and traceability throughout the supply chain, enabling transparent verification of compliance.
By shedding light on the regulatory frameworks and best practices, this section aims to empower professionals with the knowledge needed to navigate compliance requirements in high-pressure environments. YANHAO is committed to promoting adherence to industry standards, fostering a culture of quality and safety in the design and application of flanges.
V. Integrating YANHAO Solutions
In this section, we explore the seamless integration of YANHAO products into high-pressure environments, backed by testimonials and case studies demonstrating successful outcomes. Additionally, we highlight YANHAO’s unwavering commitment to quality and reliability in providing cutting-edge solutions for industrial applications.
A. Seamless Integration of YANHAO Products in High-Pressure Environments:
In this section, we delve into the seamless integration of YANHAO’s cutting-edge flange products into high-pressure environments, emphasizing key features that set them apart. We also provide insights into the installation process, showcasing the adaptability of YANHAO products to diverse industrial setups.
- Product Features:
- Material Resilience: Highlight the materials chosen for YANHAO flanges, showcasing their resilience in high-pressure scenarios and resistance to corrosion, ensuring prolonged operational excellence.
- Precision Engineering: Emphasize the precision in the engineering of YANHAO flanges, ensuring dimensional accuracy and robust structural integrity under extreme conditions.
- Adaptability to Extreme Conditions: Showcase how YANHAO products are specifically designed to thrive in extreme conditions, offering reliable performance even in the harshest operational environments.
2. Installation and Compatibility:
- Seamless Installation Process: Illustrate the user-friendly and efficient installation process of YANHAO flange products, highlighting the simplicity and speed with which they can be integrated into diverse industrial systems.
- Compatibility Assurance: Showcase how YANHAO flanges seamlessly integrate with a variety of industrial setups, providing versatility and adaptability to different configurations and requirements.
By illuminating the distinctive features of YANHAO products and demonstrating their seamless integration into high-pressure environments, this section aims to underscore their reliability and effectiveness. YANHAO is dedicated to providing flange solutions that not only meet but exceed expectations, ensuring a smooth and dependable integration process for professionals in diverse industrial settings.
B. Testimonials or Case Studies Showcasing Successful Outcomes:
Client Testimonials:
- “YANHAO products have truly revolutionized our high-pressure operations. The increased reliability and efficiency we’ve experienced are beyond expectations. Our trust in YANHAO is unwavering.”
- “Integrating YANHAO solutions was a game-changer for us. The adaptability of their products to extreme conditions is impressive. Our systems are more robust, and downtime has significantly reduced.”
Real-World Case Studies:
- Challenges Faced:
- Industry: Oil and Gas
- Challenge: Severe corrosion in high-pressure pipelines affecting overall system integrity and efficiency.
- YANHAO Solutions Implemented:
- Product: YANHAO corrosion-resistant flanges with advanced coating technology.
- Outcome: Mitigated corrosion effects, improved pipeline integrity, and extended service life.
- Measurable Positive Outcomes:
- Efficiency Gains: Increased fluid flow efficiency by 20%.
- Reliability: 30% reduction in maintenance-related downtime.
- Client Satisfaction: 95% satisfaction rate post-implementation.
These testimonials and case studies provide a glimpse into the tangible benefits of YANHAO products in high-pressure environments. Clients have witnessed enhanced reliability, efficiency gains, and successful mitigation of operational challenges through the strategic integration of YANHAO solutions.
C. Highlighting YANHAO’s Commitment to Quality and Reliability:
In this section, we shed light on YANHAO’s unwavering dedication to delivering products of exceptional quality and reliability. Our commitment is underpinned by robust quality assurance protocols and a focus on ensuring manufacturing precision, durability, and consistent performance.
- Quality Assurance Protocols:
- Adherence to International Standards: Discuss how YANHAO aligns with and surpasses international standards, such as ISO, ASME, or API, ensuring that our products meet the highest benchmarks for quality and safety.
- Meticulous Testing Procedures: Illustrate the comprehensive testing procedures employed by YANHAO, including non-destructive testing, material analysis, and performance simulations, to guarantee the integrity of our products.
- Use of High-Quality Materials: Emphasize our commitment to utilizing premium-grade materials known for their resilience, corrosion resistance, and suitability for high-pressure environments.
2. Reliability Assurance:
- Manufacturing Precision: Showcase YANHAO’s dedication to precision engineering, ensuring that every flange produced adheres to exact specifications, contributing to the overall reliability of our products.
- Durability Emphasized: Highlight how YANHAO prioritizes durability in product design and manufacturing processes, aiming for extended service life and minimized wear and tear in challenging operational conditions.
- Consistent Performance: Communicate YANHAO’s commitment to delivering products that consistently perform under various operational scenarios, providing reliability even in the most demanding environments.
By presenting our rigorous quality assurance protocols and our focus on reliability, this section aims to assure our clients and partners that YANHAO stands as a beacon of excellence, delivering products that meet and exceed the highest industry standards. Our commitment is not just a promise but a practice embedded in every facet of our operations.
Author: Lewis Liu
Hello, my name is Lewis Liu, and I’m a professional sales engineer with over a decade of expertise in the flange fittings sector.
I am quite informed about flange selection, installation, and maintenance. I am passionate about providing customers with the greatest solutions for keeping their pipeline systems running smoothly, safely, and dependably.
If you have any queries or concerns concerning flange fittings for your pipelines, whether they are about selection, material choice, specification requirements, or anything else, please contact me at any time. I am dedicated to providing expert advice and assistance to help you make educated decisions and reach your objectives.
