Are there any significant price differences between flanges made from different materials?
Introduction:
Flanges play a crucial role in ensuring the efficiency and safety of pipeline systems. Selecting the right flange material is essential to meet project requirements and budgetary considerations. In this blog post, we will delve into the topic of significant price differences between flanges made from different materials. We will explore the factors that influence flange prices, discuss industry standards for flange sizing, and highlight the expertise and reliability of Hebei Yanhao Pipeline Equipment Co., Ltd. (YANHAO) as a trusted provider of high-quality flanges. Join us in navigating the complexities of flange selection and understanding the importance of material choices in pipeline projects.
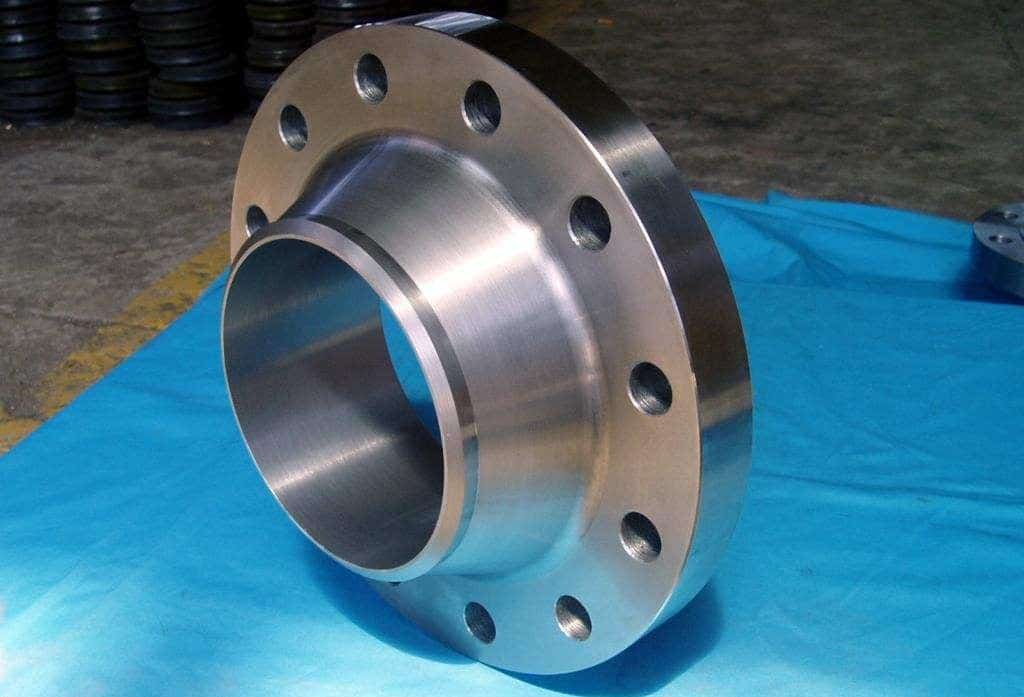
Understanding Flange Materials
Common materials used in flange manufacturing:
Flanges can be manufactured from various materials, each offering different characteristics and suitability for specific applications. The most commonly used materials for flange manufacturing include stainless steel, alloy steel, and carbon steel.
Stainless steel flanges are known for their corrosion resistance and durability. They are suitable for applications where exposure to moisture or chemicals is a concern. Stainless steel flanges are available in different grades such as 304, 316, and 321, each with varying levels of corrosion resistance.
Alloy steel flanges are highly robust and can withstand high temperatures and pressures. They are often used in industries such as oil and gas, petrochemical, and power generation. Alloy steel flanges can be made from various grades, including ASTM A182 F5, F9, F11, F22, and F91, to meet specific project requirements.
Carbon steel flanges are cost-effective and widely used in various industries. They offer good mechanical properties, making them suitable for most low-to-moderate temperature and pressure applications. Carbon steel flanges are typically manufactured from ASTM A105 or ASTM A350 LF2 materials.
When selecting flange materials, it is important to consider the specific requirements of the project, such as temperature, pressure, and medium. Adhering to international standards, such as ASME, DIN, and JIS, ensures compatibility and functional reliability.
At Hebei Yanhao Pipeline Equipment Co., Ltd. (YANHAO), we specialize in supplying both standard and non-standard flanges made from various materials. Our expertise allows us to meet unique project demands and provide custom flanges tailored to specific requirements.
Price Differences Among Different Material Options:
The price of flanges can vary depending on the material used. Factors that influence flange prices include the cost of raw materials, manufacturing processes, and market demand.
Stainless steel flanges generally tend to be more expensive compared to carbon steel flanges due to the higher cost of stainless steel alloys. Alloy steel flanges can also have a higher price range compared to carbon steel due to their enhanced properties and composition.
It is important to consider the overall project costs when selecting flange materials. While certain materials may have a higher upfront cost, they can provide long-term cost savings by reducing maintenance, repair, and replacement expenses.
At YANHAO, we have established strong relationships with renowned steel suppliers, allowing us to offer competitive prices for high-quality flanges. Our cost-effective labor and efficient manufacturing processes further contribute to providing competitive pricing options for our customers.
In conclusion, the selection of flange materials can significantly impact the overall project costs. Consideration should be given to the specific requirements of the application, industry standards, and budgetary considerations. YANHAO is committed to providing a wide range of flange materials, both standard and non-standard, at competitive prices, ensuring optimal solutions for pipeline projects.
Factors Influencing Flange Prices
Flange prices are influenced by a variety of factors that impact the overall cost of production. Understanding these factors is crucial in making informed decisions and optimizing project budgets. Some key factors that influence flange prices include:
- Material Cost: The cost of raw materials significantly affects flange prices. Different materials have varying costs based on availability, production processes, and market demand. Stainless steel and alloy steel flanges typically have higher material costs compared to carbon steel due to their unique properties and alloy composition.
- Manufacturing Processes: The complexity and precision of manufacturing processes can impact the cost of producing flanges. For example, complex shapes or intricate designs may require specialized machinery and skilled labor, leading to higher production costs. The use of advanced technologies and automation can also influence the cost of manufacturing.
- Market Demand: Flange pricing is influenced by market dynamics such as supply and demand. High demand for certain materials or specific flange types can drive up prices. Conversely, market fluctuations and increased competition may lead to price variations.
The selection of flange materials plays a vital role in determining overall project costs. While materials like stainless steel and alloy steel may have higher upfront costs, they offer enhanced durability and resistance to corrosion. This can result in lower maintenance, repair, and replacement expenses over the lifespan of the pipeline system. On the other hand, carbon steel flanges are more cost-effective for applications that do not require the advanced properties provided by stainless steel or alloy steel.
At Hebei Yanhao Pipeline Equipment Co., Ltd. (YANHAO), we have the advantage of strong relationships with renowned steel suppliers. This allows us to obtain raw materials at competitive prices, minimizing material costs for our customers. Additionally, our company benefits from cost-effective labor and efficient manufacturing processes, optimizing production expenses and offering cost-effective solutions to our clients.
By leveraging our sourcing advantages and expertise in flange manufacturing, YANHAO strives to provide high-quality flanges at competitive prices. Our commitment to delivering value to our customers is reflected in our ability to balance material costs, manufacturing efficiency, and market demand, ensuring the best possible pricing options for pipeline projects.
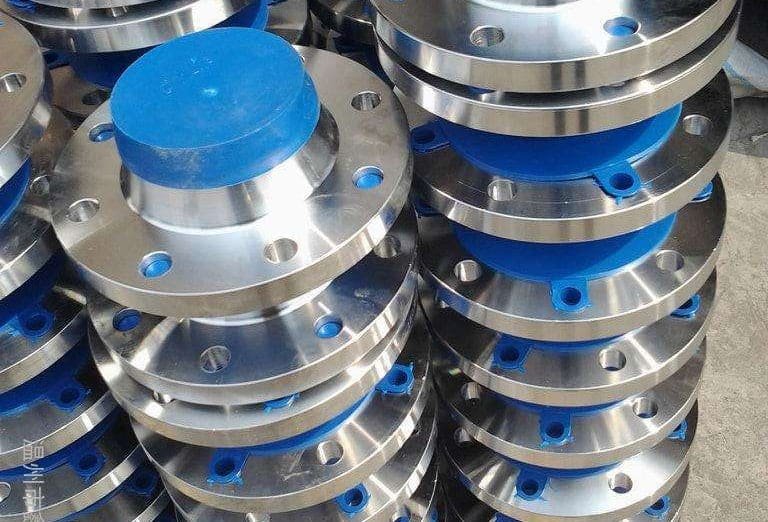
Navigating Flange Sizing: Industry Standards and Their Application
When it comes to flange sizing, adhering to industry standards is crucial to ensure compatibility and reliability in pipeline systems. These standards govern the dimensions, materials, and performance requirements of flanges, allowing for seamless integration and efficient operation. Here are some key points to consider:
- Importance of Industry Standards: Industry standards provide a common language and set of guidelines for engineers, manufacturers, and end-users. Adhering to these standards ensures that flanges from different manufacturers can be interchangeable, simplifying installation and maintenance processes. It also guarantees that the flanges meet the necessary safety and performance requirements for the specific application.
2. International Standards: Several international standards are widely used in the industry, including ASME (American Society of Mechanical Engineers), DIN (Deutsches Institut für Normung, German Institute for Standardization), and JIS (Japanese Industrial Standards). These standards have their own unique specifications regarding materials, dimensions, pressure ratings, and flange types.
- ASME Standards: ASME B16.5 and ASME B16.47 are commonly referenced for flange dimensions and ratings in the United States. These standards cover flanges from ½” to 60″ in size and provide detailed specifications for various types of flanges, such as welding neck, slip-on, threaded, and blind flanges.
- DIN Standards: DIN standards, particularly DIN 2501 and DIN 2633, are widely used in Europe. They define flange dimensions, pressure ratings, and materials for applications ranging from PN6 to PN100.
- JIS Standards: JIS B2220 is the Japanese standard for flange dimensions and pressure ratings. It covers a range of sizes and classes for flanges used in various industries.
3. Comprehensive Range of Flange Sizes: At our company, we offer a comprehensive range of flange sizes to meet diverse project requirements. Our catalog includes standard flange sizes that comply with international standards such as ASME, DIN, and JIS. These flanges are readily available and provide a reliable and cost-effective solution for most applications.
4. Customization for Non-Standard Flanges: In addition to standard sizes, we also have the capability to customize non-standard flanges to meet specific project requirements. Our engineering team works closely with clients to understand their unique needs and design customized flanges accordingly. By leveraging our manufacturing expertise and capabilities, we can produce flanges of different sizes, materials, and configurations, ensuring a perfect fit for even the most complex pipeline systems.
Navigating flange sizing involves understanding and adhering to industry standards to ensure compatibility and performance. Our comprehensive range of flange sizes, along with the ability to customize non-standard flanges, allows us to provide tailored solutions that meet the specific needs of our client’s projects. With our commitment to quality and compliance, we ensure that our flanges adhere to international standards and deliver reliable performance in various applications.
Conclusion
In conclusion, the choice of flange materials can have a significant impact on pricing. Different materials have varying costs and performance characteristics, which need to be carefully considered when selecting flanges for pipeline systems.
At Hebei Yanhao Pipeline Equipment Co., Ltd., we understand the importance of industry standards and their application in flange sizing. We are committed to providing high-quality flanges that adhere to these standards, ensuring compatibility and reliability in your projects.
Our comprehensive range of flange sizes, along with our capability to customize non-standard flanges, enables us to meet the specific needs of your projects. With years of experience and expertise in the industry, we are confident in our ability to deliver exceptional products and services.
If you have any flange needs or require assistance with navigating flange sizing, we encourage you to contact us. Our team of experts is here to provide you with the necessary support, showcasing our expertise, authority, and trustworthiness in the industry.
Trust Hebei Yanhao Pipeline Equipment Co., Ltd. for all your flange requirements. We are dedicated to delivering reliable solutions that meet the highest standards of quality and performance. Contact us today to discuss your project needs and let us help you find the right flanges for your pipeline systems.
Author: Lewis Liu
Hello, my name is Lewis Liu, and I’m a professional sales engineer with over a decade of expertise in the flange fittings sector.
I am quite informed about flange selection, installation, and maintenance. I am passionate about providing customers with the greatest solutions for keeping their pipeline systems running smoothly, safely, and dependably.
If you have any queries or concerns concerning flange fittings for your pipelines, whether they are about selection, material choice, specification requirements, or anything else, please contact me at any time. I am dedicated to providing expert advice and assistance to help you make educated decisions and reach your objectives.
