Pipeline Flange Maintenance Process
Introduction
Pipeline flanges are crucial components that connect pipes and equipment, serving important functions such as sealing, support, and rotation. As key connecting points within the entire pipeline system, the maintenance of pipeline flanges plays a vital role in ensuring safe and efficient operation. Regular flange maintenance is essential for preventing leaks, corrosion, and other potential issues. The failure of a flange can have serious consequences, including environmental pollution and costly downtime. Therefore, proper maintenance of flanges is of utmost importance.

In this blog post, we will provide a detailed overview of the pipeline flange maintenance process and the application of international standards. We will also introduce Hebei Yanhao Pipeline Equipment Co., Ltd., a trusted expert in flange production and maintenance. Whether it is flange sizing or the actual maintenance process, we can offer professional guidance and provide high-quality products and services. By choosing to work with Yanhao, you will benefit from the expertise of a reliable global supplier, ensuring that your pipeline flanges remain in optimal condition and provide a safe operational environment.
Understanding Pipeline Flanges
Pipeline flanges are essential components used in connecting pipes and equipment within a pipeline system. They serve multiple functions, including:
- Sealing: Flanges provide a secure and leak-proof connection between pipes, preventing any fluid or gas leakage.
- Support: Flanges ensure the stability and structural integrity of the pipeline by holding the pipes together.
- Accessibility: Flanges allow for easy access to the pipeline for inspection, maintenance, and repairs.
There are various types of flanges available, each designed for specific applications and conditions. Common types include:
- Weld Neck Flanges: These flanges have a long tapered hub and are typically used in high-pressure and high-temperature applications. They provide excellent strength and resistance to bending and distortion.
- Slip-On Flanges: These flanges slide over the pipe and are then welded in place. They are easy to install and suitable for low-pressure applications.
- Socket Weld Flanges: Similar to slip-on flanges, these flanges are welded to the pipe. They provide a smooth inner surface, ideal for applications where flow turbulence needs to be minimized.
- Blind Flanges: These flanges are used to close off the end of a pipe or a valve. They are commonly used for testing, inspection, or to isolate sections of the pipeline.
- Lap Joint Flanges: These flanges consist of two separate components – a stub end and a flange. They are easy to align and are suitable for systems requiring frequent dismantling.
In addition to different types of flanges, there are also industry standards that regulate flange sizing and specifications. These standards ensure compatibility and interchangeability between different manufacturers. Common standards include:
- ASME (American Society of Mechanical Engineers): ASME B16.5 and B16.47 establish the dimensions, pressure ratings, and materials for flanges used in North America.
- DIN (Deutsches Institut für Normung): DIN EN 1092-1 specifies the requirements for flanges used in Europe.
- JIS (Japanese Industrial Standards): JIS B2220 provides the dimensions and materials for flanges used in Japan.
Adhering to these industry standards ensures that flanges are properly sized, rated, and compatible with their intended application, promoting safe and efficient operation within the pipeline system.

Significance of Proper Maintenance
Routine maintenance of pipe flanges is crucial in ensuring the safe and efficient operation of a pipeline system. Regular maintenance helps to prevent various issues that can arise with flanges, including leaks, corrosion, and other potential problems. Here are some key reasons why proper maintenance is essential:
- Leak Prevention: Flanges are key points where pipes are connected, making them susceptible to leaks if not properly maintained. Regular inspections and maintenance help identify and address any potential leaks before they become major issues. By preventing leaks, the risk of environmental contamination and costly repairs is minimized.
- Corrosion Mitigation: Flanges are exposed to different environmental conditions and the fluids flowing through the pipes can be corrosive. Without proper maintenance, flanges can suffer from corrosion, which weakens the integrity of the connection. Regular cleaning, coating, and corrosion control measures can help mitigate the risk of corrosion and extend the lifespan of the flanges.
- Operational Efficiency: Flange failure can lead to costly downtime for repairs and replacements. Proper maintenance ensures that flanges are in optimal working condition, reducing the chances of unexpected failures and subsequent disruptions to pipeline operations. This helps to maintain operational efficiency and minimize financial losses.
- Safety Assurance: Flanges play a critical role in maintaining the integrity of a pipeline system. Failure of a flange can result in hazardous situations, such as the release of toxic or flammable substances, leading to safety risks for personnel and the surrounding environment. Regular maintenance helps to identify any potential weaknesses or signs of deterioration, allowing for timely repairs or replacements to ensure safety.
- Regulatory Compliance: Many industry regulations and standards require regular maintenance of pipeline components, including flanges. Adhering to these requirements ensures compliance with safety and environmental regulations, reducing the risk of penalties and legal consequences.
Failure to properly maintain pipeline flanges can have severe consequences. In addition to environmental damage and the associated costs of remediation, flange failures can result in costly downtime, reputational damage, and potential injuries to personnel. Therefore, investing in regular maintenance is vital to prevent these potential risks and ensure the safe and efficient operation of a pipeline system.
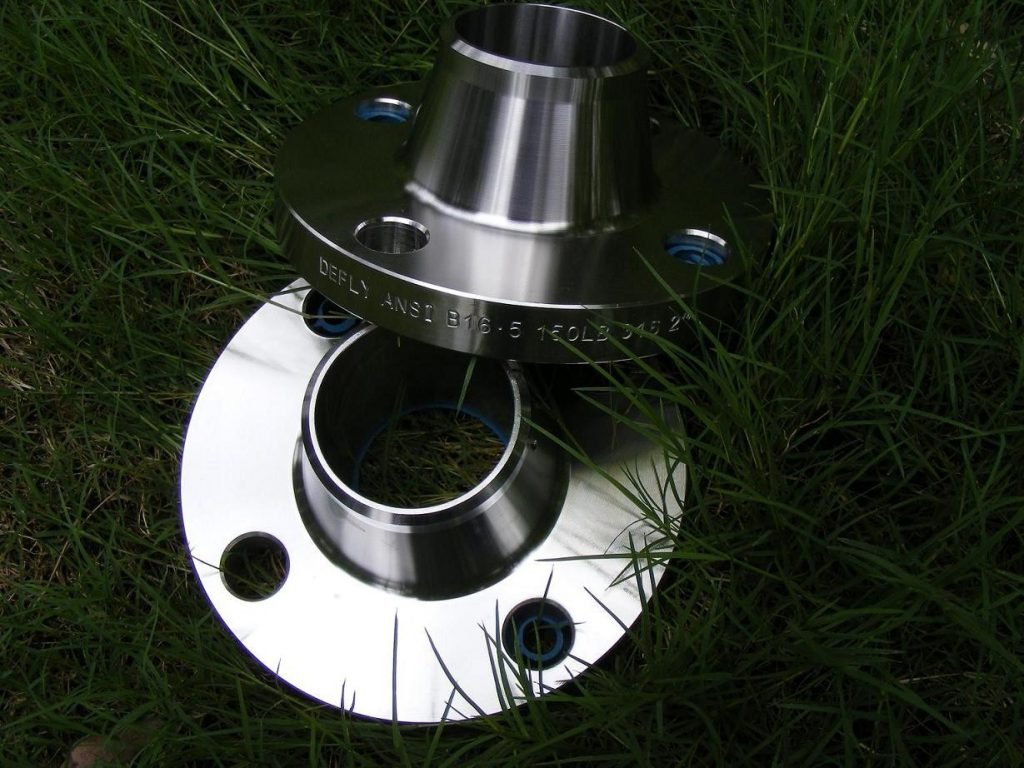
Flange Maintenance Process
Proper maintenance of pipeline flanges involves several steps, including inspection, cleaning, and reassembly. Here is a step-by-step guide to flange maintenance:
Inspection:
- Begin by visually inspecting the flange for any signs of damage, such as cracks, deformation, or corrosion.
- Check the alignment of the flange and ensure that it is properly seated on the pipe.
- Verify that the flange rating and dimensions meet the requirements of the pipeline system.
Cleaning:
- Thoroughly clean the flange and surrounding area to remove dirt, debris, rust, or any other contaminants.
- Use appropriate cleaning agents and tools such as brushes or wipes.
- Ensure that the flange surface is clean and smooth to provide a proper seal.
Gasket Installation:
- Select a gasket suitable for the specific application, taking into account factors such as temperature, pressure, and media compatibility.
- Carefully place the gasket on the flange, ensuring that it is centered and properly aligned with bolt holes.
- If required, apply a suitable gasket lubricant or sealant to facilitate installation and enhance sealing effectiveness.
Torqueing and Bolting:
- Proper torquing of bolts is crucial for achieving a tight and secure connection. Follow the manufacturer’s recommended torque values and the specified tightening sequence.
- Use calibrated torque wrenches to apply the correct torque to each bolt in a systematic and even manner.
- For large or critical flange connections, consider using additional techniques such as tensioning or hydraulic bolt tensioning to ensure proper bolt preload.
Post-Assembly Inspections:
- Once the flange is reassembled, conduct a final inspection to verify that all bolts are properly tightened and the gasket is in place.
- Ensure that there are no visible gaps or misalignments that could compromise the integrity of the connection.
It is important to note that specific maintenance procedures can vary depending on the type of flange, gasket material, and the requirements of the pipeline system. Refer to the manufacturer’s guidelines for precise instructions and adhere to industry standards and regulations.
Additionally, following best practices for flange maintenance can help improve the effectiveness and longevity of the connections. A few key best practices include using flange protectors when the flange is not connected, inspecting and addressing any signs of leaks promptly, and having a documented maintenance record to track inspections, repairs, and replacements.
By following proper maintenance procedures and incorporating best practices, the risk of flange failures and associated issues can be significantly reduced, ensuring the optimal performance and safety of the flange connections within a pipeline system.

Suggestions for Yanhao Flange Maintenance
When conducting flange maintenance, there are several additional points to be mindful of:
- Safety precautions: Always follow relevant safety procedures and wear required personal protective equipment during maintenance. Ensure the availability of safety glasses, gloves, earplugs, etc.
- Qualification requirements: For critical or high-pressure flange connections, ensure that maintenance personnel possess the necessary training and qualifications to properly understand and perform flange maintenance tasks.
- Compliance with standards: Follow applicable national or regional safety standards, industry guidelines, and regulatory requirements. Ensure that maintenance work is in compliance with these standards to reduce risks and maintain compliance.
- Material selection: While selecting gaskets, lubricants, and other materials, consider their compatibility with the media. Ensure that chosen materials can provide reliable sealing and durability under expected pressure and temperature conditions.
- Assembly sequence: Before reassembling flange connections, ensure that the correct assembly sequence is followed. Often, this entails tightening bolts in the specified order. Following the correct assembly sequence ensures even, tight, and stable connections.
- Regular inspections: In addition to routine maintenance, regular inspections of flange connections are essential. Check bolt tightness, gasket condition, and flange surface corrosion, among other issues. Regular inspections can identify potential problems and allow for timely remedial actions.
- Pressure testing: In certain situations such as equipment replacement, repairs, or system modifications, pressure testing of flange connections may be required. Before conducting the test, adhere strictly to relevant specifications and procedures to ensure safety and reliability.
Ensure to tailor the maintenance approach to specific circumstances and the type of flanges being used. By following correct maintenance steps and paying attention to these additional points, the reliability, safety, and performance of flange connections can be assured.

Benefits of Working with Yanhao
- High-quality products and services: Yanhao is known for providing top-notch products and services in the field of flange maintenance. Their reputation for excellence ensures that you will receive reliable and durable flanges that meet your requirements.
- Wide range of materials and customization options: Yanhao offers an extensive selection of flange materials, allowing you to choose the most suitable option for your specific needs. Additionally, they provide customization options to meet unique project requirements.
- Advanced production and testing equipment: Yanhao utilizes advanced equipment in its production process, ensuring high precision and quality in every flange. Their testing equipment helps to guarantee that the flanges meet industry standards and performance expectations.
- Adherence to industry standards and regulations: Yanhao is committed to complying with all relevant industry standards and regulations. This ensures that their flanges meet the necessary safety, quality, and performance requirements.
- Proven track record: Yanhao has a strong track record of delivering flange solutions to diverse industries worldwide. Their experience and expertise make them a reliable partner for flange maintenance projects.
Working with Yanhao ensures that you have access to high-quality products, customization options, advanced equipment, and compliance with industry standards. Their proven track record demonstrates their ability to meet the needs of various industries.
If you are in need of reliable flange maintenance services, don’t hesitate to contact Yanhao today. With its high-quality products, customization options, advanced equipment, and commitment to industry standards, Yanhao is well-equipped to meet your flange maintenance requirements. Take advantage of our proven track record and exceptional services by reaching out to us now. Contact Yanhao to discuss your flange maintenance needs and discover the benefits of working with a reputable and trusted partner.
Author: Lewis Liu
Hello, my name is Lewis Liu, and I’m a professional sales engineer with over a decade of expertise in the flange fittings sector.
I am quite informed about flange selection, installation, and maintenance. I am passionate about providing customers with the greatest solutions for keeping their pipeline systems running smoothly, safely, and dependably.
If you have any queries or concerns concerning flange fittings for your pipelines, whether they are about selection, material choice, specification requirements, or anything else, please contact me at any time. I am dedicated to providing expert advice and assistance to help you make educated decisions and reach your objectives.
