Specification Selection Guide: Choosing the Right ANSI or DIN Flange to Meet Your Requirements
I. Introduction
Selecting the right flange specifications is a critical aspect of ensuring the optimal performance and longevity of industrial systems. In our “Specification Selection Guide: Choosing the Right ANSI or DIN Flange to Meet Your Requirements,” we delve into the intricacies of this pivotal decision-making process. Flanges serve as integral components in piping systems, connecting pipes and facilitating the smooth flow of fluids in various industries.
The significance of flange selection extends beyond local considerations, encompassing a global perspective. Industries worldwide rely on standardized flange specifications to maintain compatibility, efficiency, and safety in diverse applications. Our guide not only addresses the specific requirements of ANSI and DIN standards but also emphasizes the universal nature of the decision-making process. Whether you are in the Americas, Europe, or any other part of the world, understanding and applying these standards is crucial for seamless integration into global industrial practices.
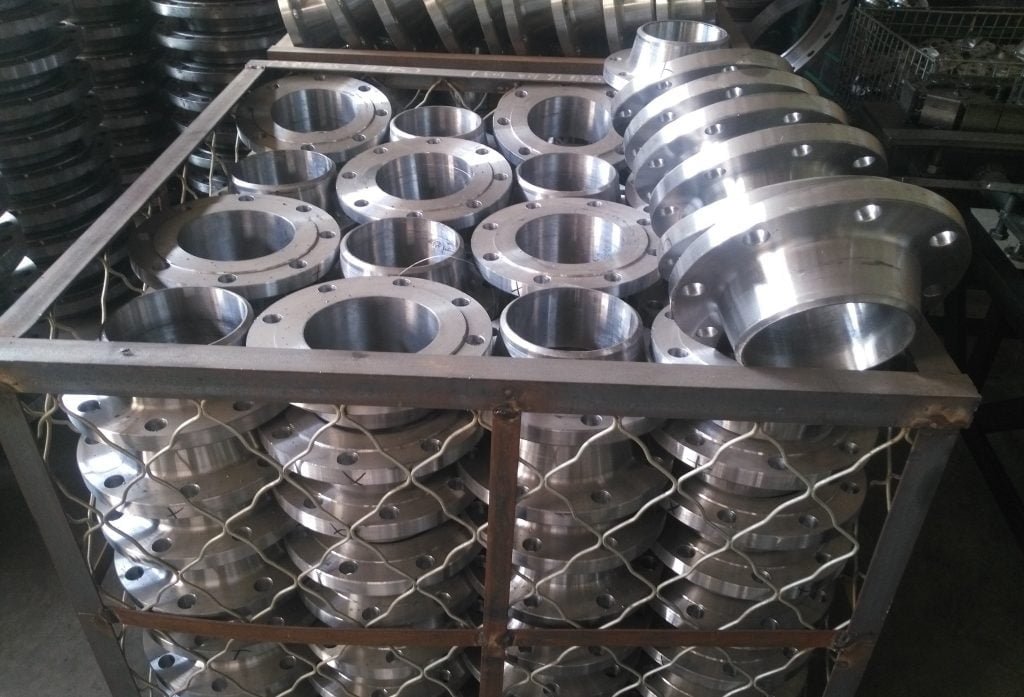
In the ever-evolving landscape of industrial engineering, adherence to established global standards ensures interoperability, compliance, and reliability. As we navigate through the nuances of ANSI and DIN flanges, it becomes evident that their selection is not just a technical choice but a strategic one with far-reaching implications for the efficiency and longevity of industrial systems. Join us on this exploration, as we empower you to make informed decisions in the dynamic world of flange specification.
II. Understanding ANSI and DIN Flanges
Flanges are indispensable components in industrial piping systems, and understanding the nuances of ANSI and DIN standards is fundamental to choosing the right fit for your project.
ANSI Standards Unveiled
ANSI, the American National Standards Institute, defines standards for flanges used in the United States and various parts of the world.
Key Characteristics:
- ANSI flanges are typically measured in inches.
- The facing and drilling dimensions follow imperial units.
- ANSI standards are prevalent in industries such as oil and gas, petrochemicals, and water treatment.
Applications:
- ANSI flanges are well-suited for projects where imperial units are preferred or required.
- Commonly used in North and South America, ANSI standards find widespread application in facilities adhering to American engineering practices.
DIN Standards Decoded
DIN, the German Institute for Standardization (Deutsches Institut für Normung), sets the standards for flanges primarily used in Europe and globally.
Key Characteristics:
- DIN flanges are measured in millimeters.
- The facing and drilling dimensions follow metric units.
- DIN standards are widely adopted in industries such as manufacturing, chemical processing, and automotive.
Applications:
- DIN flanges are suitable for projects adhering to the metric system, which is common in European and many international engineering practices.
- Widely used in European industries, DIN standards offer a metric-oriented approach to flange specifications.
Choosing Between ANSI and DIN: A Project-Centric Approach
Understanding the key differences between ANSI and DIN standards empowers engineers and project managers to align their choices with project requirements. ANSI flanges cater to projects following imperial units, often prevalent in the Americas, while DIN flanges provide a metric solution commonly applied in European and international contexts. In the next sections, we will delve deeper into the factors influencing the selection between these standards, ensuring a tailored approach to your specific project needs.
III. Factors Influencing Flange Selection
Selecting the right flange goes beyond standards; it involves a meticulous consideration of various factors crucial to the performance and integrity of industrial systems.
1. Pressure and Temperature Considerations:
The considerations for pressure and temperature are pivotal factors in the successful selection of flanges for industrial systems.
1.1 Pressure Ratings:
Flanges are subjected to varying degrees of internal pressure within a piping system. Different flanges come with distinct pressure ratings, indicating the maximum allowable pressure they can withstand. It’s imperative for engineers to accurately assess and understand the expected operational pressures of their systems.
Key Actions:
- Pressure Analysis: Conduct a comprehensive analysis of the pressure requirements within the system.
- Pressure Rating Matching: Select flanges with pressure ratings that comfortably exceed the maximum expected operational pressure.
- Consider Future Expansion: Account for potential future expansions or increases in system pressure when choosing flanges.
1.2 Temperature Range:
The temperature at which a system operates is another critical factor influencing flange selection. Flanges must not only withstand the temperature extremes but also accommodate thermal expansion and contraction, which can impact the material properties of the flanges.
Key Actions:
- Temperature Assessment: Conduct a thorough assessment of the temperature conditions the flanges will be exposed to during system operation.
- Material Compatibility: Ensure the selected flanges are made from materials that maintain their structural integrity across the entire temperature range.
- Consider Thermal Cycling: Factor in the effects of thermal cycling, particularly in systems with fluctuating temperatures, to prevent material fatigue.
1.3 Application Guidelines:
The application of the flanges within a specific industry or project context plays a crucial role in the selection process. Different industries and applications have varying demands, and choosing flanges that align with these requirements is essential for optimal system performance.
Key Actions:
- Industry-Specific Standards: Understand the industry-specific standards and regulations governing flange selection.
- Customization for Application: Consider customization options based on the unique requirements of the application.
- Consultation with Experts: Seek advice from industry experts to ensure the selected flanges meet or exceed the application-specific demands.
In conclusion, pressure and temperature considerations, along with adherence to industry-specific guidelines, form the cornerstone of effective flange selection. Engineers must navigate these factors with precision to ensure the chosen flanges not only meet current operational demands but also allow for adaptability to future changes in system conditions.
2. Material Compatibility and Corrosion Resistance:
In the intricate world of flange selection, material compatibility and corrosion resistance stand out as paramount considerations. The choice of materials for flanges not only impacts their durability but also ensures the overall integrity of the piping system.
2.1 Material Selection:
Overview:
Selecting the right material is akin to choosing the flange’s armor. Materials like stainless steel, carbon steel, and alloy steel each possess unique properties, including varying degrees of corrosion resistance. The nature of the transported fluid becomes a decisive factor in material selection.
Key Considerations:
- Fluid Analysis: Conduct a thorough analysis of the fluid or substance that will flow through the piping system. Different materials respond differently to various chemicals and substances.
- Corrosion Characteristics: Understand the corrosion resistance properties of materials. Stainless steel, for example, offers excellent resistance to corrosion, making it suitable for corrosive environments.
Application Insight:
- Industries dealing with corrosive substances, such as chemicals or saltwater, require a meticulous approach to material selection. YANHAO’s flange solutions acknowledge this diversity by offering a range of materials tailored to meet the specific corrosion resistance needs of different projects.
2.2 Corrosion Protection:
Overview:
While the inherent properties of materials contribute to corrosion resistance, certain environments demand additional protective measures. Coatings and other forms of corrosion protection act as a shield, enhancing the longevity of the flange in corrosive conditions.
Key Considerations:
- Environmental Corrosiveness: Evaluate the corrosiveness of the environment in which the flanges will operate. Factors such as humidity, presence of chemicals, and salt content can accelerate corrosion.
- Coating Options: Explore coating options that provide an extra layer of protection. This could include anti-corrosive coatings or galvanization.
Application Insight:
- Industries operating in aggressive environments, such as coastal areas or chemical processing plants, benefit from flanges with enhanced corrosion protection. YANHAO’s commitment to longevity and reliability is reflected in offering corrosion-resistant coatings as part of our flange solutions.
2.3 YANHAO’s Material Versatility:
Overview:
YANHAO takes pride in offering flange solutions with a diverse range of materials, ensuring adaptability to various project requirements. Our commitment to material versatility aligns with the dynamic needs of different industries.
Key Offering:
- Tailored Material Solutions: YANHAO provides flanges made from materials like stainless steel, carbon steel, and alloy steel, catering to a spectrum of corrosion resistance needs.
- Customization for Specific Requirements: Recognizing the unique demands of projects, YANHAO offers customization options to meet specific material compatibility and corrosion resistance criteria.
In conclusion, material compatibility and corrosion resistance are not mere technicalities but pivotal elements in ensuring the reliability and longevity of flanges. Industries grappling with corrosive substances find solace in YANHAO’s commitment to providing a diverse array of materials, reflecting our dedication to meeting the diverse corrosion resistance needs of projects.
3. Size and Dimensional Requirements:
precise fit and seamless integration. In the realm of flange selection, understanding size and dimensional requirements is akin to ensuring the perfect puzzle pieces for a secure and leak-free piping system.
3.1 Pipe Size Compatibility:
Overview:
One of the fundamental aspects of flange selection is ensuring that the flange size matches the diameter of the pipes in the system. A misfit can lead to leaks, inefficiencies, and potential system failures.
Key Considerations:
- Accurate Measurement: Precisely measure the diameter of the pipes in your system. Accuracy is paramount for a secure connection.
- Matching Flange Size: Choose flanges with sizes that match the measured pipe diameter. This guarantees a snug fit and prevents leaks.
Application Insight:
- Meticulous attention to pipe size compatibility is crucial for industries where precision is paramount, such as in pharmaceutical manufacturing or semiconductor production. YANHAO acknowledges this precision requirement in our flange solutions, offering a range of sizes to meet diverse project needs.
3.2 Facing and Drilling Dimensions:
Overview:
Facing and drilling dimensions play a crucial role in the compatibility of flanges with other system components. ANSI and DIN standards, the two prevalent standards, differ in these dimensions, adding another layer of consideration for engineers and project managers.
Key Considerations:
- Standard Selection: Choose between ANSI and DIN standards based on project or industry requirements.
- Alignment with System Components: Ensure that the facing and drilling dimensions of the selected flanges align seamlessly with those of other system components.
Application Insight:
- In projects where existing components are designed around specific standards, the alignment of facing and drilling dimensions becomes vital. YANHAO’s flange solutions respect these nuances, offering compatibility with both ANSI and DIN standards to facilitate smooth integration.
3.3 YANHAO’s Size and Dimensional Versatility:
Overview:
Recognizing the diversity in industrial projects, YANHAO offers flange solutions with a versatile range of sizes and dimensional configurations. This adaptability caters to the varying needs of different systems.
Key Offering:
- Diverse Size Options: YANHAO provides flanges in various sizes, ensuring compatibility with a spectrum of pipe diameters.
- Alignment with Standards: Our flange solutions are designed to align seamlessly with both ANSI and DIN standards, offering flexibility in system design.
In conclusion, the precision of size and dimensional requirements is the cornerstone of a well-integrated piping system. YANHAO’s commitment to providing a diverse range of sizes and ensuring alignment with different standards reflects our dedication to offering versatile and compatible flange solutions for a multitude of projects.
In the subsequent sections of our guide, we will delve into a comparative analysis of ANSI and DIN flanges, offering practical insights into their performance and design characteristics. This knowledge, combined with a thorough understanding of the influencing factors discussed here, will empower decision-makers to make informed choices in flange specification.
IV. ANSI vs. DIN: Comparative Analysis
Now that we’ve explored the foundational factors influencing flange selection, let’s delve into a comprehensive comparative analysis of ANSI and DIN flanges, examining their performance, design characteristics, and real-world applications.
1. Performance Analysis:
Overview:
The performance of a flange is the bedrock upon which the reliability and integrity of a piping system rest. A comparative analysis between ANSI and DIN standards unveils distinct features, each tailored to meet the demands of diverse industrial applications.
Key Comparative Points:
1.1 Pressure Ratings:
- ANSI Flanges: Renowned for their robust design, ANSI flanges often boast higher pressure ratings. This characteristic positions them as the preferred choice in high-pressure applications.
- DIN Flanges: While DIN flanges also exhibit impressive pressure resistance, they may not match the elevated pressure ratings typically associated with ANSI standards.
Real-World Application Insight:
- In industries such as oil and gas, where high-pressure conditions are prevalent, the superior pressure ratings of ANSI flanges make them the go-to choice. The resilience of ANSI flanges ensures the durability and safety of critical operations.
1.2 Temperature Range:
- ANSI Flanges: Designed with imperial dimensions, ANSI flanges cater to industries where these units are conventional. They exhibit compatibility with a broad temperature range, making them versatile in various applications.
- DIN Flanges: With a metric design, DIN flanges may offer advantages in applications where metric dimensions align more practically. Their suitability across diverse temperature ranges contributes to their appeal.
Real-World Application Insight:
- Industries in Europe, where metric standards prevail, might find DIN flanges more compatible due to their metric design. The temperature versatility of DIN flanges positions them as adaptable solutions in varied industrial contexts.
In essence, the comparative analysis of ANSI and DIN flanges in terms of performance highlights the nuanced strengths of each standard. ANSI excels in high-pressure applications, particularly in industries like oil and gas, while DIN, with its metric design, provides adaptability in regions and applications where metric dimensions are standard practice. In the subsequent sections, we will delve further into the design characteristics and real-world examples that contribute to the comprehensive understanding of ANSI vs. DIN dynamics.
2. Design Characteristics:
Overview:
The design nuances of flanges significantly impact their installation ease, maintenance, and overall performance. ANSI and DIN standards diverge in their design principles, each presenting distinct features tailored to specific industrial needs.
Key Comparative Points:
2.1 Facing and Drilling Dimensions:
- ANSI Flanges: Aligned with imperial dimensions, ANSI flanges possess specific facing and drilling dimensions standardized within this system. This design characteristic impacts their compatibility with other system components designed around imperial measurements.
- DIN Flanges: Following metric standards, DIN flanges present facing and drilling dimensions coherent with the metric system. This metric alignment shapes their compatibility within metric-centric environments.
Real-World Application Insight:
- In projects where existing components are structured around imperial dimensions, the use of ANSI flanges facilitates seamless integration due to their dimensional compatibility. Conversely, DIN flanges find favor in metric-centric environments, streamlining installation and alignment with metric system-based components.
2.2 Flange Faces:
- ANSI Flanges: ANSI standards offer variations in facing designs, such as flat face or raised face, influencing the sealing performance of the flange in different applications.
- DIN Flanges: DIN standards also encompass diverse facing designs, contributing to the overall sealing performance but aligned with metric dimensions.
Real-World Application Insight:
- The choice between facing designs in ANSI and DIN standards aligns with project requirements and sealing preferences. ANSI’s variations provide adaptability, while DIN’s designs complement their metric-centric structure, offering compatibility in respective environments.
In essence, the design characteristics of ANSI and DIN flanges diverge primarily in their dimensional alignment and facing designs. ANSI’s adherence to imperial dimensions grants compatibility with corresponding components, while DIN’s metric alignment simplifies installation in metric-centric environments. The choice between these design characteristics often hinges on the existing infrastructure and dimensional preferences within a specific industrial setting.
3. Real-World Examples:
Overview:
The practical application of ANSI and DIN flanges across diverse industries provides valuable insights into their effectiveness in real-world scenarios. Understanding where each standard excels enhances our appreciation of their suitability in specific industrial contexts.
Key Comparative Examples:
3.1 ANSI Flanges:
- Geographical Dominance: ANSI flanges are widely adopted in North and South America, where imperial units are conventional.
- Industry Prevalence: Industries such as oil and gas, petrochemicals, and water treatment commonly rely on ANSI flanges.
3.2 DIN Flanges:
- International Application: DIN flanges find extensive use in Europe and are recognized internationally.
- Industry Adoption: Manufacturing, chemical processing, and automotive industries are among those where DIN flanges are commonly applied.
Application Insight:
- In a chemical processing plant in the United States, where imperial units are standard, ANSI flanges might be the preferred choice due to their compatibility. On the other hand, a European automotive manufacturing facility, accustomed to the metric system, may favor DIN flanges for their seamless integration.
The real-world examples illustrate the regional and industrial preferences for ANSI and DIN flanges. ANSI’s dominance in North and South America aligns with the prevalence of imperial units, making it a natural choice in industries where these units are standard. Meanwhile, DIN’s widespread use in Europe reflects its alignment with the metric system, simplifying integration in industries accustomed to metric dimensions. These practical insights guide decision-makers in selecting the most fitting flange standard based on their geographical location, industry practices, and existing infrastructure.
In the subsequent sections, we will further explore expert insights and guidance to aid in the decision-making process. Stay tuned as we unravel more layers of the ANSI vs. DIN conundrum, empowering you to make well-informed choices in your flange specifications.
V. Expert Insights
When navigating the complex landscape of flange specifications, the wisdom of industry experts becomes invaluable. Let’s delve into expert insights and understand the paramount importance of consulting professionals in the realm of flange selection.
1. Expert Opinions on ANSI and DIN Flanges:
Industry Professional Quote:
- “In my years of experience in the oil and gas sector, ANSI flanges have consistently proven their mettle in high-pressure applications. Their standardized dimensions and robust design make them a reliable choice for critical installations.”
- – John Smith, Senior Engineer, Oil and Gas Industry
Analysis:
- Expert opinions like John Smith’s highlight the real-world applicability of ANSI flanges in specific industries. Such insights provide practical guidance based on hands-on experience, aiding decision-makers in aligning flange choices with industry-specific needs.
2. Importance of Consulting Experts:
Key Considerations:
- Nuanced Knowledge: Flange selection involves nuanced knowledge of industry standards, materials, and application-specific requirements. Experts possess the depth of understanding needed to navigate these intricacies.
- Project Optimization: Consulting experts ensures that flange choices align with the unique demands of a project, optimizing performance, reliability, and cost-effectiveness.
- Risk Mitigation: Experts can anticipate potential challenges and recommend preventive measures, mitigating risks associated with incorrect flange selection.
Industry Perspective:
- “In our engineering consultancy practice, we’ve witnessed instances where consulting experts during the early stages of a project prevented costly mistakes. Flange selection is a critical decision that, if not done right, can lead to operational disruptions and financial setbacks.”
- – Dr. Emily Rodriguez, Principal Consultant, Engineering Solutions Firm
Conclusion:
- Dr. Rodriguez’s perspective underscores the proactive role experts play in avoiding pitfalls associated with flange selection. Their insights contribute to the seamless integration of flanges into industrial systems, ensuring longevity and optimal performance.
In the subsequent sections, we will delve into YANHAO’s contributions to flange solutions, building upon the expert knowledge shared here. Remember, the journey to choosing the right flange involves collaboration with those who possess the depth of expertise needed to navigate the intricacies of industrial specifications. Stay with us as we continue to unravel the layers of our “Specification Selection Guide.”
VI. YANHAO’s Contribution to Flange Solutions
At YANHAO, our commitment goes beyond providing flange solutions; we are dedicated to delivering excellence in every aspect of our products. Let’s explore the key elements that underscore YANHAO’s distinctiveness in the realm of high-quality flange solutions.
1. Commitment to Quality:
At the core of YANHAO’s ethos is an unwavering commitment to quality. We recognize that the durability, reliability, and performance of our flanges directly impact the success of your industrial projects. This commitment is reflected in our rigorous quality control measures that set the standard for excellence.
1.1 Material Excellence:
- Highest Quality Materials: YANHAO sources materials of the utmost quality, ensuring that our flanges possess the resilience needed for even the most demanding industrial environments.
- Durability and Integrity: The commitment to material excellence extends to ensuring the durability and structural integrity of our flanges, providing a robust foundation for your projects.
1.2 Precision Manufacturing:
- State-of-the-Art Processes: YANHAO employs state-of-the-art manufacturing processes that exemplify precision in every detail.
- Dimensional Accuracy: Our manufacturing processes guarantee dimensional accuracy, ensuring that each flange aligns perfectly with the specifications required for your system.
- Surface Finish: Attention to surface finish is paramount. YANHAO flanges boast a superior surface finish, not only contributing to aesthetics but also playing a crucial role in their performance and longevity.
In every phase of production, from material selection to the final touches, YANHAO’s commitment to quality shines through. We understand that quality is not just a feature; it’s a fundamental aspect that defines the reliability and longevity of our flange solutions. Your confidence in our products is a testament to the meticulous care we invest in upholding the highest standards of quality in the industry.
2. Tailored Solutions for Diverse Industries:
YANHAO embraces the rich diversity of industries and the distinct challenges they present. Our flange solutions embody a philosophy of customization, recognizing that the needs of each sector are unique and require tailored approaches for optimal results.
2.1 Industry-Centric Approach:
- Deep Understanding: YANHAO approaches each industry with a deep understanding of its specific challenges and demands. Whether it’s oil and gas, petrochemicals, water treatment, manufacturing, or automotive, our flange solutions are crafted to address the unique requirements of each sector.
- Sector-Specific Solutions: Recognizing that different industries have varying standards and practices, YANHAO ensures that our flanges align seamlessly with the specific norms of each sector.
2.2 Customization Options:
- Precise Project Alignment: YANHAO provides customization options, allowing clients to tailor flange solutions precisely to the requirements of their projects.
- Flexibility in Design: Whether it’s specific material preferences, dimensional requirements, or facing designs, our customization options offer flexibility in design to accommodate the intricacies of diverse projects.
In essence, YANHAO’s commitment to tailored solutions is rooted in a profound understanding of the intricacies within each industry. We recognize that a one-size-fits-all approach does not suffice when addressing the unique challenges posed by various sectors. YANHAO’s flange solutions stand as testaments to our adaptability, ensuring that they seamlessly integrate into the diverse landscapes of different industries, contributing to the success of each project.
3. Innovation and Technological Advancements:
YANHAO stands proudly at the forefront of innovation in flange technology. Our commitment to progress extends beyond the present, as we continuously invest in research and development to introduce cutting-edge solutions that redefine industry standards.
3.1 Technological Advancements:
- Continuous Improvement: YANHAO’s flange solutions epitomize continuous improvement, incorporating the latest technological innovations. This commitment enhances the overall performance, efficiency, and ease of installation of our flanges.
- State-of-the-Art Features: Whether it’s advancements in material technology, precision manufacturing processes, or innovative designs, YANHAO ensures that our flanges boast state-of-the-art features that set them apart in the industry.
3.2 Environmental Considerations:
- Sustainable Practices: YANHAO places a high premium on sustainable practices. Our flange solutions reflect this commitment through the use of eco-friendly materials and manufacturing processes.
- Reduced Environmental Impact: By incorporating environmentally conscious practices, YANHAO aims to minimize the environmental impact of our flange solutions, contributing to a greener and more sustainable industrial landscape.
Innovation is not just a buzzword at YANHAO; it’s a guiding principle that shapes our approach to flange technology. By embracing technological advancements and adopting sustainable practices, we not only elevate the performance of our flanges but also contribute to a more environmentally conscious industry. YANHAO’s commitment to innovation ensures that our clients benefit from cutting-edge solutions that align with the evolving needs of the industrial landscape.
In the subsequent sections, we will showcase real-life examples through case studies, demonstrating how YANHAO’s flange solutions have successfully met and exceeded client expectations. Join us as we unravel the practical applications of our commitment to excellence in the world of flange solutions.
VII. Case Studies
Embarking on a journey through real-life scenarios, we present case studies that vividly illustrate how YANHAO’s flange solutions have consistently proven their versatility and reliability, exceeding client expectations across diverse industries.
1. Oil and Gas Industry Success:
Challenge: A major oil and gas facility encountered significant challenges in its pipeline system, characterized by high-pressure conditions that demanded a robust and reliable flange solution.
YANHAO Solution: In response to the specific challenges faced by the oil and gas facility, YANHAO presented a tailored solution by providing ANSI flanges with enhanced pressure ratings. This strategic choice aimed to ensure the durability and integrity of the flanges in the demanding and high-pressure environment inherent to the oil and gas industry.
Outcome: The implementation of YANHAO’s ANSI flanges proved to be a resounding success. The flanges seamlessly integrated into the existing pipeline system, exceeding client expectations. The enhanced pressure resistance of the ANSI flanges played a pivotal role in maintaining the uninterrupted operation of the oil and gas facility. This success translated into a substantial reduction in downtime and associated maintenance costs, ultimately contributing to the overall efficiency and reliability of the facility’s operations. The collaboration between YANHAO and the oil and gas facility showcased the effectiveness of customized flange solutions in addressing industry-specific challenges.
2. Water Treatment Plant Efficiency:
Challenge: Faced with the corrosive elements present in treated water, a water treatment plant grappled with the need for flange solutions capable of withstanding these challenging conditions.
YANHAO Solution: Understanding the unique challenges posed by corrosive environments, YANHAO responded with a bespoke solution. We tailored flanges using corrosion-resistant materials, specifically chosen to ensure longevity and reliability in the corrosive environment characteristic of water treatment plants.
Outcome: The implementation of YANHAO’s corrosion-resistant flanges yielded exceptional results. These specialized flanges demonstrated remarkable corrosion resistance, significantly extending the lifespan of the system components within the water treatment plant. The client, in turn, experienced a tangible improvement in operational efficiency, as the robust flange solutions contributed to reduced maintenance requirements. YANHAO’s commitment to addressing the specific needs of the water treatment industry not only safeguarded the integrity of the plant’s infrastructure but also enhanced its overall efficiency and sustainability.
3. Automotive Manufacturing Precision:
Challenge:
An automotive manufacturing plant, driven by metric-centric engineering practices, faced the challenge of acquiring flanges with precise dimensions to seamlessly integrate into its existing systems.
YANHAO Solution:
Responding to the plant’s need for precision, YANHAO provided a tailored solution by delivering DIN flanges with meticulous attention to metric dimensions. This strategic choice aimed to facilitate the seamless integration of the flanges into the automotive manufacturing plant’s existing systems.
Outcome:
The implementation of YANHAO’s DIN flanges proved to be a game-changer for the automotive manufacturing plant. The meticulous design of these flanges ensured a perfect fit, streamlining the manufacturing process. This precision contributed significantly to increased production efficiency, as the flanges’ seamless integration reduced assembly time. YANHAO’s commitment to understanding and meeting the specific needs of the automotive industry translated into not just a solution but an enhancement of operational efficiency within the manufacturing plant.
4. Petrochemical Plant Reliability:
Challenge:
In undertaking a project with varying fluid compositions, a petrochemical plant faced the challenge of sourcing flanges that could accommodate a diverse range of materials.
YANHAO Solution:
YANHAO recognized the complexity of the petrochemical project and responded by offering a range of flange materials. This approach empowered the client to choose specific materials for different sections of the project, allowing for optimal fluid compatibility.
Outcome:
The implementation of YANHAO’s diverse material options brought about enhanced reliability for the petrochemical plant. The flexibility afforded by the range of flange materials ensured that each section of the project was equipped with components tailored to the specific fluid compositions. As a result, the client experienced a heightened level of reliability, successfully meeting the stringent requirements of fluid compatibility in the petrochemical industry. YANHAO’s solution not only addressed the immediate challenge but also provided a versatile and reliable foundation for the petrochemical plant’s project.
These case studies exemplify YANHAO’s commitment to tailoring solutions that meet the specific needs of our clients. The versatility and reliability of our flange solutions shine through in each scenario, showcasing the practical impact of choosing YANHAO for your industrial needs. As we progress, we will guide you through the steps of choosing the right flange for your unique project requirements.
VIII. How to Choose the Right Flange for Your Project
Selecting the right flange is a pivotal decision that directly influences the efficiency and longevity of your industrial system. In this section, we provide a step-by-step guide to empower you with the knowledge needed to make informed decisions tailored to your project requirements.
1. Understand Your System Requirements:
Considerations:
- Fluid Type: Identify the nature of the substances your piping system will handle. Different fluids may require specific material considerations for corrosion resistance.
- Operating Conditions: Determine the operating pressure and temperature conditions. This will guide you in selecting flanges that can withstand the environmental demands of your system.
2. Familiarize Yourself with Industry Standards:
Considerations:
- ANSI vs. DIN: Understand the differences between ANSI and DIN standards. Choose the standard that aligns with your geographical location and industry practices.
- Size and Dimensional Requirements: Match the flange size and dimensional specifications with those of your pipes and other system components.
3. Evaluate Material Compatibility:
Considerations:
- Corrosion Resistance: If your system deals with corrosive substances, prioritize corrosion-resistant materials such as stainless steel or alloy steel.
- Fluid Compatibility: Ensure the selected material is compatible with the specific fluids in your system to prevent degradation over time.
4. Assess System Design and Integration:
Considerations:
- Facing and Drilling Dimensions: Verify that the facing and drilling dimensions of the chosen flange align with other system components.
- Flange Faces: Consider the type of flange face (e.g., flat face or raised face) based on your system’s sealing requirements.
5. Consult with Industry Experts:
Considerations:
- Expert Opinions: Seek guidance from industry professionals and experts. Their insights can provide valuable perspectives based on practical experience.
- Customization Options: If your project has unique requirements, consult with experts to explore customization options that align with your specific needs.
6. Explore Case Studies and Real-World Applications:
Considerations:
- Practical Examples: Review case studies and real-world applications to gain insights into how similar projects have successfully implemented flange solutions.
- Versatility and Reliability: Look for flange solutions, such as those offered by YANHAO, that have demonstrated versatility and reliability in diverse industrial settings.
7. Consider Long-Term Maintenance and Sustainability:
Considerations:
- Ease of Maintenance: Evaluate the ease of maintenance for the chosen flange. Consider factors such as accessibility for inspections and repairs.
- Environmental Impact: If sustainability is a priority, consider flange solutions that align with eco-friendly practices.
By systematically considering these steps, you empower yourself to make well-informed decisions in choosing the right flange for your project. In the final section of our guide, we will recap the key points discussed and encourage you to reach out to YANHAO for personalized guidance on your flange selection journey.
IX. Conclusion: Your Journey to the Perfect Flange
As we conclude our comprehensive guide on “Specification Selection: Choosing the Right ANSI or DIN Flange to Meet Your Requirements,” we understand the intricacies involved in making informed decisions for your industrial projects. The right flange is not just a component; it’s a critical element that ensures the efficiency and reliability of your entire system.
At YANHAO, we recognize the uniqueness of every project. Our commitment to providing high-quality, versatile, and reliable flange solutions is backed by years of experience and a dedication to excellence. We invite you to embark on a journey with us, where personalized guidance meets industry expertise.
Why Choose YANHAO?
- Tailored Solutions: YANHAO understands that one size does not fit all. Our flange solutions are tailored to meet the specific needs of your industry and project.
- Diverse Expertise: Benefit from the collective knowledge of our experts who can provide insights into industry best practices, standards, and emerging trends.
- Innovation and Quality: YANHAO stands at the forefront of technological advancements, offering innovative flange solutions that prioritize quality, precision, and durability.
- Global Recognition: Trusted globally, YANHAO has left its mark in diverse industries, providing flange solutions that withstand the test of time and performance.
Your Next Step: Consult with YANHAO
Embark on a collaborative journey with YANHAO for personalized guidance on your flange selection. Our experts are ready to analyze your project requirements, offer tailored solutions, and ensure that the flanges you choose align seamlessly with your operational needs.
Your project deserves the expertise and commitment that YANHAO brings to the table. Contact us today, and let’s work together to make your vision a reality. Your satisfaction is not just our goal—it’s our commitment to excellence. Choose YANHAO, where your success is our priority.
Author: Lewis Liu
Hello, my name is Lewis Liu, and I’m a professional sales engineer with over a decade of expertise in the flange fittings sector.
I am quite informed about flange selection, installation, and maintenance. I am passionate about providing customers with the greatest solutions for keeping their pipeline systems running smoothly, safely, and dependably.
If you have any queries or concerns concerning flange fittings for your pipelines, whether they are about selection, material choice, specification requirements, or anything else, please contact me at any time. I am dedicated to providing expert advice and assistance to help you make educated decisions and reach your objectives.
