The Importance of Quality Control in Pipe Flange Manufacturing
The manufacturing industry is constantly evolving, and it is essential to maintain high-quality standards to ensure product reliability and customer satisfaction. In the context of pipe flange manufacturing, quality control is critical to ensure that the final product meets industry standards and regulations. Pipe flanges are essential components in piping systems, and their failure can result in significant consequences, including production downtime, environmental damage, and financial losses. Therefore, it is vital to implement quality control measures throughout the manufacturing process to prevent defects, reduce costs, and improve product quality. In this blog, we will explore the importance of quality control in pipe flange manufacturing, the challenges faced in implementing these measures, and the benefits that result from ensuring high-quality standards.
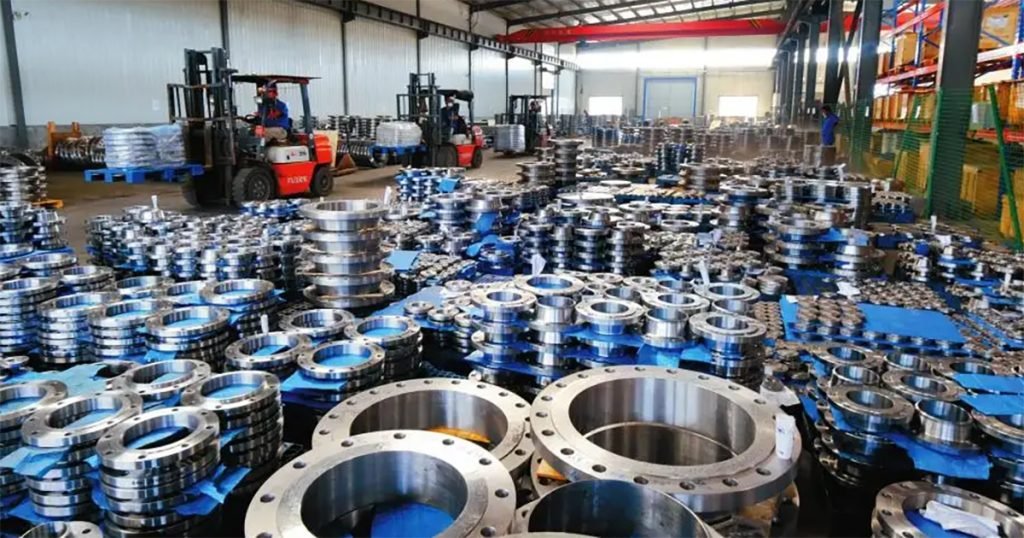
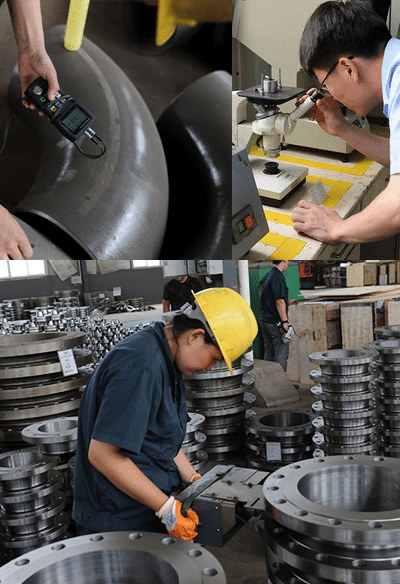
I. Introduction
A. What is a pipe flange?
A pipe flange is a component used to connect sections of piping or other equipment together, such as valves, pumps, and vessels. It is essentially a flat or raised rim or collar that is attached to the end of a pipe, allowing it to be bolted to another flange or component. The flange provides a surface for connecting and sealing the joint, and it also allows for easy disassembly and maintenance of the piping system. Pipe flanges come in different shapes and sizes, and they can be made from various materials, including steel, stainless steel, and aluminum. Flanges must be designed and manufactured to meet industry standards and regulations to ensure the proper functioning and prevent failures.
B. The important role of pipeline flanges in pipeline systems
Pipe flanges play a critical role in piping systems by providing a secure and reliable connection between different components, such as pipes, valves, and fittings. These flanges help to ensure the safe and efficient operation of the entire system by preventing leaks, maintaining pressure and flow, and allowing for easy access and maintenance. Additionally, pipe flanges can withstand high temperatures and pressures, making them ideal for use in a wide range of applications, including oil and gas, chemical processing, and water treatment plants. Flanges also enable the system to be modified or expanded easily by allowing new components to be added or replaced without having to disassemble the entire system. Overall, pipe flanges are a critical component of any piping system, and their proper design, installation, and maintenance are essential for ensuring the safety, efficiency, and reliability of the system.
C. Explanation of the importance of Quality Control in Pipe Flange Manufacturing
The importance of quality control in pipe flange manufacturing cannot be overstated. Pipe flanges are essential components in piping systems, and their failure can result in significant consequences, including production downtime, environmental damage, and financial losses. Quality control measures are critical in ensuring that the final product meets industry standards and regulations and that it is safe and reliable for use in various applications.
Effective quality control measures can help to prevent defects, reduce production costs, and improve product quality. By identifying and addressing potential issues early in the manufacturing process, manufacturers can avoid costly production delays, recalls, or repairs caused by product failures. Quality control measures can also help to ensure that the product meets customer expectations, leading to increased customer satisfaction and loyalty.
Moreover, in many industries, compliance with industry standards and regulations is mandatory. Therefore, implementing quality control measures is necessary to meet these requirements and maintain legal compliance. Failure to comply with these regulations can result in fines, legal action, and damage to a company’s reputation.
In summary, quality control is critical in pipe flange manufacturing to ensure product reliability, meet industry standards and regulations, prevent failures, and improve customer satisfaction. It is a necessary investment for manufacturers to make to ensure the safety, efficiency, and reliability of their products.
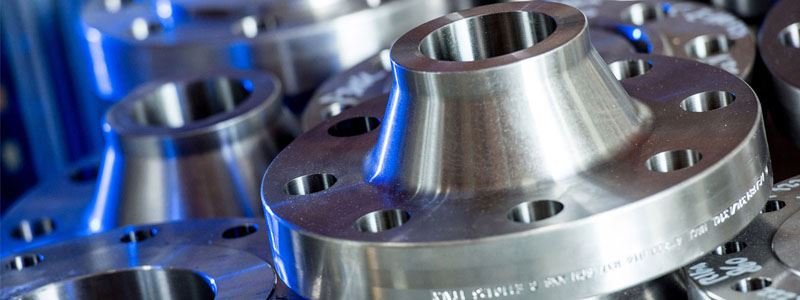

II. Standards and Regulations for Pipe Flange Manufacturing
A.Overview of Pipeline Flange Industry Standards and Regulations
The manufacturing of pipeline flanges is subject to various industry standards and regulations to ensure the safety and reliability of the products. These standards and regulations provide guidelines for the design, materials, testing, and inspection of pipeline flanges, and compliance with them is mandatory in many industries. Some of the most commonly recognized pipeline flange standards and regulations include:
American Society of Mechanical Engineers (ASME) – ASME is a professional organization that develops standards and codes for the design and manufacture of pressure vessels and piping systems, including pipeline flanges. The ASME Boiler and Pressure Vessel Code (BPVC) contains standards for the design, materials, testing, and inspection of pipeline flanges.
American Petroleum Institute (API) – API is an industry organization that develops standards and codes for the oil and gas industry, including pipeline flanges. The API 6A standard provides requirements for the design, materials, testing, and inspection of pipeline flanges used in the oil and gas industry.
International Organization for Standardization (ISO) – ISO is a non-governmental organization that develops standards for various industries, including pipeline flanges. The ISO 7005 standard provides specifications for pipeline flanges used in different pressure and temperature conditions.
European Committee for Standardization (CEN) – CEN is a European standards organization that develops standards for various industries, including pipeline flanges. The EN 1092 standard provides specifications for flanges used in various pressure and temperature conditions.
Occupational Safety and Health Administration (OSHA) – OSHA is a government agency that sets and enforces safety and health standards for workplaces in the United States. Compliance with OSHA regulations is mandatory for workplaces, including those that manufacture pipeline flanges.
In summary, compliance with industry standards and regulations is critical in the manufacturing of pipeline flanges to ensure the safety and reliability of the products. Manufacturers must be aware of and adhere to these standards and regulations to avoid legal and reputational risks and ensure customer satisfaction.
B.The Importance of Pipe Flange Standards and Regulations
The importance of pipe flange standards and regulations lies in their ability to ensure the safety, reliability, and quality of pipeline flanges used in various industries. These standards and regulations provide guidelines for the design, manufacturing, testing, and inspection of pipeline flanges, ensuring that they meet specific requirements for strength, durability, and performance.
One of the key benefits of adhering to pipe flange standards and regulations is improved safety. Flange failures can result in hazardous situations, including leaks, fires, and explosions, that can endanger workers, damage equipment, and harm the environment. By following industry standards and regulations, manufacturers can produce pipeline flanges that meet specific safety requirements, reducing the risk of catastrophic incidents.
Additionally, adhering to pipe flange standards and regulations can lead to improved quality and reliability of the products. These standards provide detailed specifications for materials, dimensions, and manufacturing processes that ensure that the pipeline flanges are of consistent quality and meet specific performance requirements. This can help to reduce production costs, minimize product defects, and increase customer satisfaction.
Compliance with pipe flange standards and regulations can also help manufacturers remain competitive in the marketplace. Companies that produce high-quality products that meet industry standards and regulations are more likely to attract customers and secure contracts. Furthermore, compliance with regulations can prevent costly fines, legal action, and damage to a company’s reputation.
In summary, adherence to pipe flange standards and regulations is essential for ensuring the safety, reliability, and quality of pipeline flanges. It is critical for manufacturers to comply with these standards and regulations to protect workers, equipment, and the environment, as well as to remain competitive in the marketplace.
III.Types of methods for quality control of pipe flanges and their importance
Here are some types of quality control methods for pipeline flanges and their importance:
Incoming inspection: This is important to ensure that the raw materials used in the manufacturing process meet the required specifications. It helps to prevent defective materials from being used in the production process, which could lead to substandard products.
In-process inspection: This is important to detect any defects or inconsistencies that may affect the quality of the final product. By monitoring the manufacturing process, manufacturers can identify and correct any issues early on, which helps to prevent defects and reduce waste.
Non-destructive testing (NDT): This is important to detect defects in pipeline flanges without damaging them. NDT methods such as ultrasonic and magnetic particle testing are essential for ensuring the safety and reliability of pipeline flanges by detecting defects that may not be visible to the naked eye.
Destructive testing: This is important to evaluate the strength, durability, and other properties of pipeline flanges. By subjecting samples of pipeline flanges to extreme conditions, manufacturers can ensure that the products meet the required standards for performance and safety.
Dimensional inspection: This is important to ensure that pipeline flanges meet the required specifications for size and shape. This helps to prevent issues such as leaks and malfunctions that could occur if the flanges do not fit properly.
Visual inspection: This is important to detect defects such as cracks, surface imperfections, and deformations that may affect the safety and reliability of pipeline flanges.
Performance testing: This is important to ensure that pipeline flanges meet the required performance standards under simulated operating conditions. By testing the products under realistic conditions, manufacturers can ensure that they will perform reliably in real-world applications.
Statistical process control (SPC): This is important to monitor the manufacturing process and detect any variations that may affect the quality of the final product. By using statistical methods to identify trends and patterns in the manufacturing process, manufacturers can make adjustments to improve quality and efficiency.
Overall, these quality control methods are essential for ensuring the safety, reliability, and performance of pipeline flanges. By using these methods, manufacturers can produce high-quality products that meet the required standards and specifications, reducing the risk of accidents and ensuring customer satisfaction.
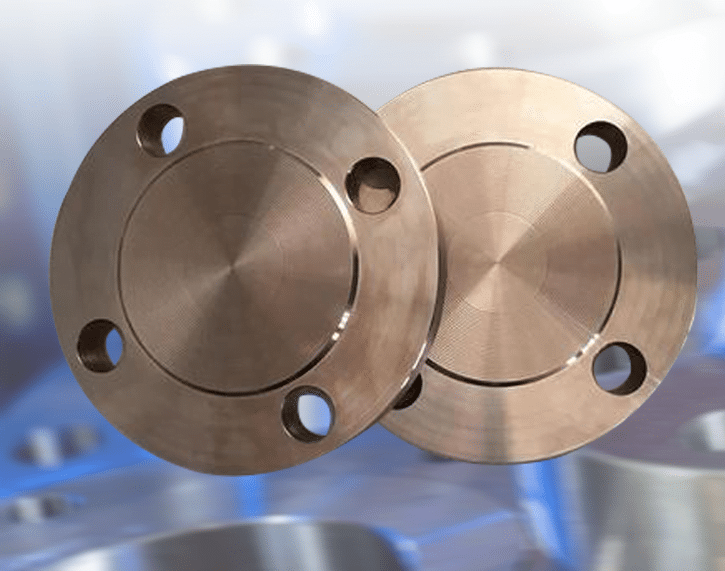


IV. Benefits of Quality Control in Pipe Flange Manufacturing
A. Enhanced Product Quality
Quality control ensures that pipe flanges are manufactured according to the required specifications and standards. This results in the production of high-quality flanges that are safe, reliable, and durable. The use of quality control methods such as non-destructive testing and visual inspection helps to detect defects and prevent them from reaching the market. This enhances the overall quality of the products, which can lead to increased customer satisfaction and improved brand reputation.
B. Reduction in Production Costs
Quality control helps to identify and eliminate defects in the manufacturing process, which reduces the cost of production. By detecting defects early on, manufacturers can avoid producing defective products, reducing the need for rework, repair, or replacement. This helps to reduce the overall production costs, which can lead to increased profitability for the company.
C. Prevention of Product Failures
Quality control helps to prevent product failures by ensuring that the pipe flanges are manufactured to the required standards and specifications. This reduces the risk of accidents, injuries, or damage to the equipment caused by faulty flanges. By preventing product failures, quality control helps to maintain the safety and reliability of the pipeline system, which is critical in industries such as oil and gas, chemical, and pharmaceuticals.
D. Improvement of Customer Satisfaction
Quality control helps to improve customer satisfaction by ensuring that the pipe flanges meet the customer’s requirements and expectations. By producing high-quality products that meet the required standards and specifications, manufacturers can build customer trust and loyalty. This can lead to repeat business, positive word-of-mouth, and increased sales.
In summary, quality control in pipe flange manufacturing has several benefits, including enhanced product quality, reduction in production costs, prevention of product failures, and improvement of customer satisfaction. These benefits contribute to the overall success of the company and its ability to compete in the market.
Chinese flange manufacturers have been implementing strict quality control measures to ensure the high quality of their products. They understand that quality is a critical factor in building a positive brand reputation and attracting customers. Therefore, they have invested heavily in technology, equipment, and skilled labor to improve their manufacturing process and implement various quality control methods, such as inspection, testing, and documentation. These measures ensure that their products meet the required standards and specifications, are safe, reliable, and durable, and can withstand the demands of the pipeline industry. Additionally, Chinese flange factories have also implemented continuous improvement processes to identify and eliminate defects, reduce production costs, and improve customer satisfaction. Through these efforts, Chinese flange factories have earned a reputation for producing high-quality products and have become leaders in the global flange industry.
V. Challenges of Quality Control in Pipe Flange Manufacturing
A. Complexity of Manufacturing Process
Pipe flange manufacturing involves a complex manufacturing process that includes several steps, such as cutting, forging, welding, and machining. Each step requires specialized equipment and skilled labor, and any error in any of these steps can result in defective flanges. Maintaining quality control throughout the entire manufacturing process is crucial to ensuring that the final product meets the required specifications and standards.
B. High degree of Precision Required
Pipe flanges are critical components of pipeline systems, and their performance depends on their accuracy and precision. Even small deviations in the dimensions or tolerances of the flanges can lead to leaks, failures, and accidents. Maintaining a high degree of precision in the manufacturing process requires advanced technology, specialized equipment, and skilled labor.
C. Cost of Equipment and Skilled Labor
Quality control in pipe flange manufacturing requires advanced technology, specialized equipment, and skilled labor. Investing in these resources can be expensive for manufacturers, especially for small and medium-sized enterprises. Additionally, skilled labor can be difficult to find and retain, which can further add to the cost of quality control.
In summary, the challenges of quality control in pipe flange manufacturing include the complexity of the manufacturing process, the high degree of precision required, and the cost of equipment and skilled labor. Overcoming these challenges requires a commitment to quality, investment in technology and equipment, and a skilled and dedicated workforce.



VI. Conclusion
A. Recap of the importance of Quality Control in Pipe Flange Manufacturing
In summary, quality control is critical in pipe flange manufacturing due to several reasons. Firstly, it helps to ensure that pipe flanges are manufactured according to the required standards and specifications, resulting in high-quality, safe, reliable, and durable products. Secondly, quality control helps to identify and eliminate defects, reducing the cost of production and improving the overall efficiency of the manufacturing process. Thirdly, quality control helps to prevent product failures, maintaining the safety and reliability of the pipeline system. Finally, quality control helps to improve customer satisfaction, build trust, and loyalty, and contribute to the overall success of the company. Despite the challenges, manufacturers must prioritize quality control to remain competitive in the market and maintain a positive brand reputation.
B. Call to Action for Manufacturers to Implement Quality Control Measures
the importance of quality control in pipe flange manufacturing cannot be overstated. As a manufacturer, it is crucial to prioritize quality control to ensure that your products meet the required standards and specifications, prevent defects and product failures, reduce production costs, and improve customer satisfaction. To achieve this, you need to implement various quality control measures such as inspection, testing, documentation, and continuous improvement processes. These measures require investment in technology, equipment, and skilled labor, but the benefits outweigh the costs in the long run. By prioritizing quality control, you can build a positive brand reputation, attract more customers, and achieve long-term success in the pipeline industry. So, take action today and implement quality control measures in your pipe flange manufacturing process to ensure the highest quality products for your customers.
C.China Flange Manufacturer High-Quality Low Price
There are several advantages to purchasing flanges from China. Firstly, China has a well-established flange manufacturing industry with many experienced and skilled manufacturers. This means that customers have a wide range of options when it comes to choosing a supplier, and can find one that meets their specific needs and requirements.
Secondly, Chinese flange manufacturers often offer competitive pricing compared to other global manufacturers, while still maintaining a high level of quality control. This is due to lower production costs in China, including lower labor and material costs.
Thirdly, many Chinese flange manufacturers have a strong commitment to customer service and are willing to work closely with their customers to ensure that they receive the products that they need. They also provide comprehensive after-sales support, including product warranties and technical support.
Lastly, the flange industry in China is constantly evolving, with manufacturers adopting new technologies and production methods to improve the quality and efficiency of their products. This means that customers can expect to receive high-quality flanges that meet the latest industry standards and specifications.
In conclusion, this blog has highlighted the importance of quality control in pipe flange manufacturing. We have discussed the significance of adhering to industry standards and regulations, the various quality control methods, and the benefits of implementing quality control measures, including enhanced product quality, cost reduction, prevention of product failures, and improvement of customer satisfaction. Additionally, we have also examined the challenges of quality control, such as the complexity of the manufacturing process, the high degree of precision required, and the cost of equipment and skilled labor. Despite these challenges, manufacturers must prioritize quality control to remain competitive in the market and maintain a positive brand reputation. By taking action and implementing quality control measures, manufacturers can produce high-quality, safe, and reliable pipe flanges that meet the needs of customers and the requirements of the pipeline industry.
Author: Lewis Liu
Hello, my name is Lewis Liu, and I’m a professional sales engineer with over a decade of expertise in the flange fittings sector.
I am quite informed about flange selection, installation, and maintenance. I am passionate about providing customers with the greatest solutions for keeping their pipeline systems running smoothly, safely, and dependably.
If you have any queries or concerns concerning flange fittings for your pipelines, whether they are about selection, material choice, specification requirements, or anything else, please contact me at any time. I am dedicated to providing expert advice and assistance to help you make educated decisions and reach your objectives.
