What are the common flange sizes?
1. Introduction
Flanges play a crucial role in connecting pipes, valves, and other mechanical components in various industries. These flat, circular discs with holes allow for easy assembly, disassembly, and maintenance of piping systems. Flanges are vital for ensuring leak-free connections and supporting the flow of fluids, gases, and other materials.
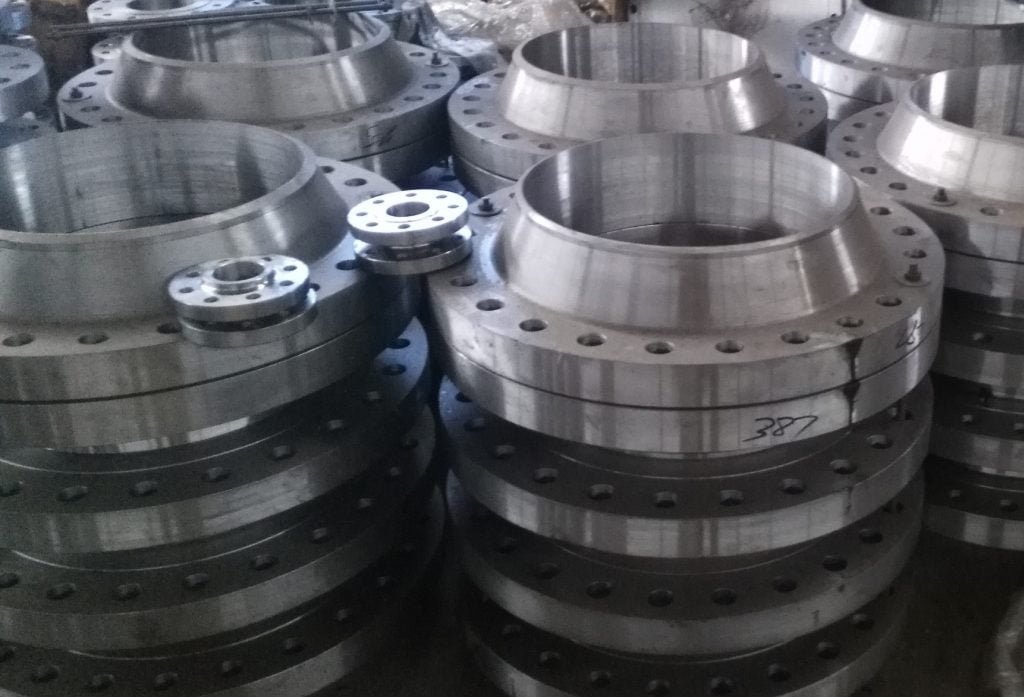
When it comes to flange manufacturing, YANHAO emerges as a leading company with years of expertise and a strong reputation. With a commitment to producing high-quality flanges, YANHAO has become a trusted provider in the industry. Their dedication to precision, reliability, and customer satisfaction sets them apart from the competition.
In this blog post, we will explore the common flange sizes, diving into the depths of industry standards, dimensions, and applications. YANHAO’s professional insights and expertise will guide us along the way, ensuring you have a comprehensive understanding of flange sizes and their significance in various sectors.
2. Importance of Correct Flange Sizes
Selecting the right flange size is of utmost importance for achieving optimal performance and ensuring safety in various industrial applications. Here are a few reasons why correct flange sizing is crucial:
- Sealing Integrity: Flanges are primarily used to create leak-free connections between pipes or equipment. If the flange size is not accurately matched to the pipe or equipment it connects to, there is a high risk of leaks, which can lead to product loss, environmental hazards, and compromises in system efficiency.
- Pressure and Stress Distribution: Flanges are designed to withstand specific pressure ratings and stress loads. Inadequate flange sizing may result in excessive stress concentration or insufficient strength to handle the internal pressure of the system. This can lead to flange deformation, leakage, or even catastrophic failures, posing significant safety risks.
- Efficient Flow Characteristics: Flange sizes are optimized to ensure smooth and continuous fluid or gas flow through the pipeline. Incorrect flange sizing may cause flow disruptions, turbulence, or pressure drops, resulting in reduced system efficiency, increased energy consumption, and decreased overall performance.
- Compatibility: Flanges need to be compatible with the pipes, valves, and equipment they connect. If the flange size does not match the mating components, it can lead to misalignment, misfit, or even complete incompatibility, hindering the proper functioning of the system.
Incorrect flange sizing can cause an array of problems across different applications. For instance, in the oil and gas industry, mismatches can lead to oil or gas leaks, posing environmental and safety hazards. In the petrochemical industry, improper sizing can result in system inefficiencies, compromising product quality and profitability. In water treatment facilities, incorrect flange sizes can hinder the flow of water, reducing treatment capacity and increasing maintenance requirements.
To avoid these issues, it is crucial to consult experts like YANHAO, who possess the knowledge and experience to determine the correct flange sizes based on specific application requirements. Their expertise ensures seamless and safe operations, minimizing risks and maximizing efficiency.
3. Industry Standards for Flange Sizes
In the world of flange manufacturing, several industry standards define the dimensions, materials, and specifications of flanges. Here are some commonly used standards:
- ASME (American Society of Mechanical Engineers): ASME standards, specifically ASME B16.5 and B16.47, are widely followed in North America and many other parts of the world. These standards provide guidelines for the dimensions, pressure ratings, and materials of flanges used in various industries, including oil and gas, chemical, and power generation.
- API (American Petroleum Institute): API standards, such as API 6A and API 17D, focus on the oil and gas industry. API standards specify the use of flanges in critical applications like wellheads, Christmas trees, and subsea equipment. These standards cover both the dimensions and pressure ratings of flanges, ensuring reliability and safety in oil and gas operations.
- DIN (Deutsches Institut für Normung): DIN standards, prevalent in Germany and Europe, define flange sizes and specifications. DIN standards, including DIN 2631-2638 and DIN EN 1092-1, provide guidelines for flanges used in a wide range of applications, from chemical and petrochemical plants to water treatment facilities and general mechanical engineering.
- JIS (Japanese Industrial Standards): JIS standards, particularly JIS B2220, are commonly used in Japan and some Asian countries. JIS standards outline the dimensions, materials, and pressure ratings for flanges used in industries like shipbuilding, automotive, and construction.
These industry standards play a critical role in defining flange sizes for different applications. They provide guidelines on flange dimensions, including the outer diameter, bolt-hole spacing, and thickness, to ensure compatibility and interchangeability between components from different manufacturers.
Furthermore, these standards specify pressure ratings and materials for flanges, ensuring that they can handle the specific operating conditions and environmental factors they will encounter. This standardization allows for easier procurement, installation, and maintenance of flanges, fostering industry-wide consistency and safety.
YANHAO, as a reputable flange manufacturer, understands the significance of adhering to these industry standards. Their flange manufacturing processes conform to the specifications outlined in ASME, API, DIN, and JIS standards, guaranteeing that their products meet the necessary requirements for various applications.
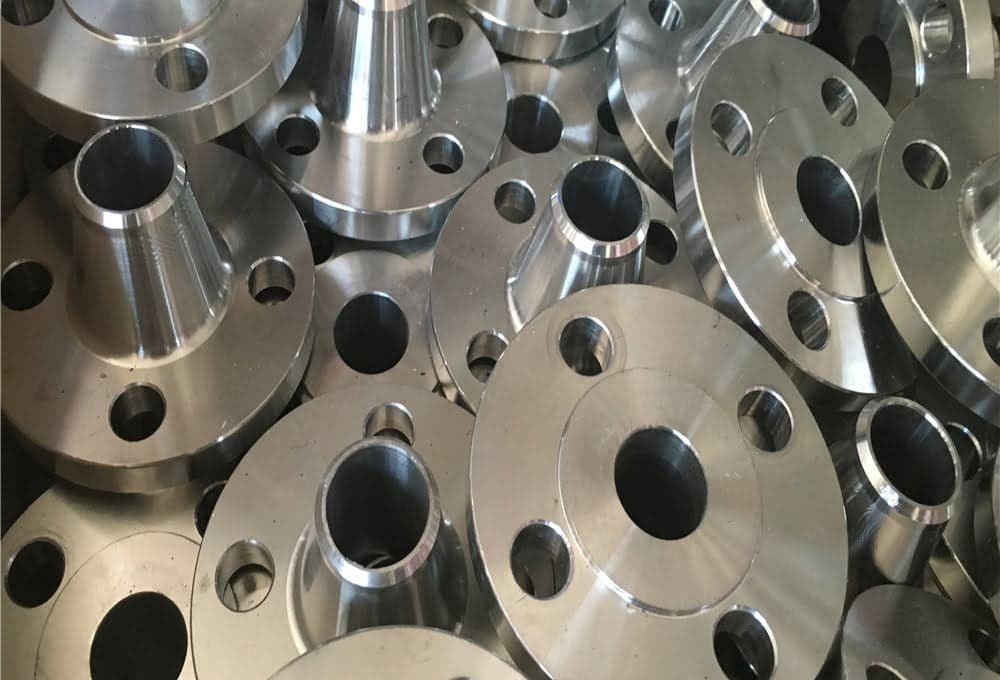
4. Flange Size Chart
Flange Type | Size Range | Pressure Rating |
Slip-On Flange | 1/2″ – 48″ | 150 lbs – 2500 lbs |
Weld Neck Flange | 1/2″ – 96″ | 150 lbs – 2500 lbs |
Blind Flange | 1/2″ – 96″ | 150 lbs – 2500 lbs |
Threaded Flange | 1/2″ – 48″ | 150 lbs – 2500 lbs |
Socket Weld Flange | 1/2″ – 48″ | 150 lbs – 2500 lbs |
Please note that these specifications are general and may vary depending on the applicable industry standards, such as ASME, API, DIN, or JIS. It is essential to consult the specific standard or refer to the manufacturer’s documentation for detailed and accurate flange size information.
5. Application-based Flange Size Selection
When selecting the correct flange size for a specific application, several factors need to be considered. These factors include pressure ratings, pipe dimensions, flange materials, and application requirements. Here are some guidelines for choosing the appropriate flange size based on different applications:
- Pressure Ratings: The flange size should be selected to withstand the maximum operating pressure of the system. It is essential to ensure that the pressure rating of the flange matches or exceeds the system’s pressure requirements.
- Pipe Dimensions: The flange size should match the pipe dimensions to ensure a proper fit and connection. The flange’s inner diameter should match the outer diameter of the pipe, considering factors such as pipe size, wall thickness, and schedule.
- Flange Materials: The choice of flange material depends on the application’s specific requirements. Different materials have varying properties, including corrosion resistance, temperature resistance, and compatibility with the fluid being transported. Consider factors such as the type of fluid, operating conditions, and environmental factors when selecting flange materials.
- Application Requirements: Consider the specific application requirements to determine the appropriate flange size. This includes factors such as the type of industry (e.g., oil and gas, petrochemical, water treatment), temperature and pressure fluctuations, fluid characteristics (such as corrosiveness or viscosity), and regulatory standards that may dictate specific flange dimensions.
It is crucial to consult industry standards (e.g., ASME, API, DIN) and seek guidance from qualified engineers or flange manufacturers. These resources can provide more detailed information and recommendations based on the specific requirements of your application.

6. Conclusion
In conclusion, selecting the correct flange sizes is of paramount importance in ensuring safe and efficient operations in various industries. The right flange size ensures a proper fit, reliable sealing, and the ability to withstand the required pressure and temperature conditions. Incorrect flange sizing can lead to leaks, system failures, safety hazards, and costly downtime.
When it comes to sourcing flanges, YANHAO is a trusted and reliable choice. With its expertise, professionalism, and commitment to industry standards, YANHAO offers a wide range of high-quality flanges that meet the diverse needs of different applications. Whether it’s oil and gas, petrochemical, water treatment, or any other industry, YANHAO can provide flanges with the correct sizes and specifications tailored to your specific requirements.
By choosing YANHAO as your flange supplier, you can have confidence in the quality, reliability, and performance of their products. Their adherence to industry standards ensures that the flanges you receive meet the necessary specifications and comply with regulatory requirements. With YANHAO, you can expect exceptional service and support throughout the flange selection process, ensuring that you find the right flange sizes for your applications.
Choose YANHAO for your flange needs, and enjoy the peace of mind that comes with working with a trusted and reputable source in the industry.
Author: Lewis Liu
Hello, my name is Lewis Liu, and I’m a professional sales engineer with over a decade of expertise in the flange fittings sector.
I am quite informed about flange selection, installation, and maintenance. I am passionate about providing customers with the greatest solutions for keeping their pipeline systems running smoothly, safely, and dependably.
If you have any queries or concerns concerning flange fittings for your pipelines, whether they are about selection, material choice, specification requirements, or anything else, please contact me at any time. I am dedicated to providing expert advice and assistance to help you make educated decisions and reach your objectives.
