What are the different material classifications of flanges?
I. Introduction:
Flanges are unsung heroes in the world of engineering and manufacturing, playing a pivotal role in connecting, sealing, and supporting various components in a wide array of industries. Whether you’re in the energy sector dealing with pipelines, the chemical industry handling corrosive substances, or even in construction, you’ll encounter flanges at the heart of these operations.
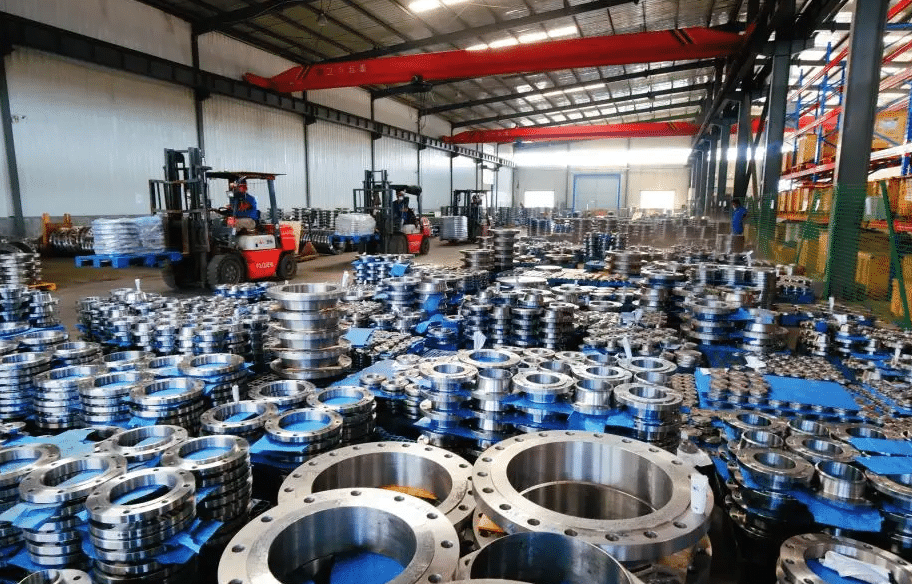
In this blog, we’re diving deep into the world of flanges, shedding light on their significance in industrial applications. Our primary focus? The intricate web of different material classifications that make flanges so adaptable and reliable in diverse settings. From heavy-duty carbon steel to specialized materials for unique challenges, we’ll explore how the choice of flange material can make or break your projects.
So, fasten your seatbelts and get ready to journey through the materials that hold our world together – flanges!
II. Flanges and Their Significance:
Flanges might seem like simple, unassuming components, but their role in industrial systems is nothing short of crucial. They serve as the unsung heroes that keep everything connected and running smoothly. Here, we’ll delve into their vital importance:
Connecting the Dots: Flanges act as connectors, bridging the gap between pipes, valves, and equipment in complex industrial systems. Think of them as the sturdy handshake between different components, ensuring a tight and secure connection. This connection, in turn, is what allows fluids, gases, and even solids to flow seamlessly from one point to another within a system.
Sealing the Deal: Beyond their connection role, flanges are also responsible for creating a leak-proof seal. In environments where containment and integrity are paramount, such as chemical plants, refineries, or even nuclear facilities, flanges prevent hazardous substances from escaping and keep the system operating safely.
Versatility in Action: The applications of flanges span far and wide, transcending geographical and industrial boundaries. You’ll find flanges wherever fluid or gas transport is involved. They’re integral in oil and gas pipelines, water treatment plants, power generation facilities, and even in the food and beverage industry. The versatility of flanges makes them indispensable in global industries, making sure that vital resources reach their destinations reliably.
In Summary: Flanges are the linchpin of industrial systems, providing connectivity, sealing, and versatility that are essential for various applications worldwide. Their significance lies in their ability to maintain the integrity of systems and ensure the efficient flow of materials, which, in turn, impacts industries and economies on a global scale.
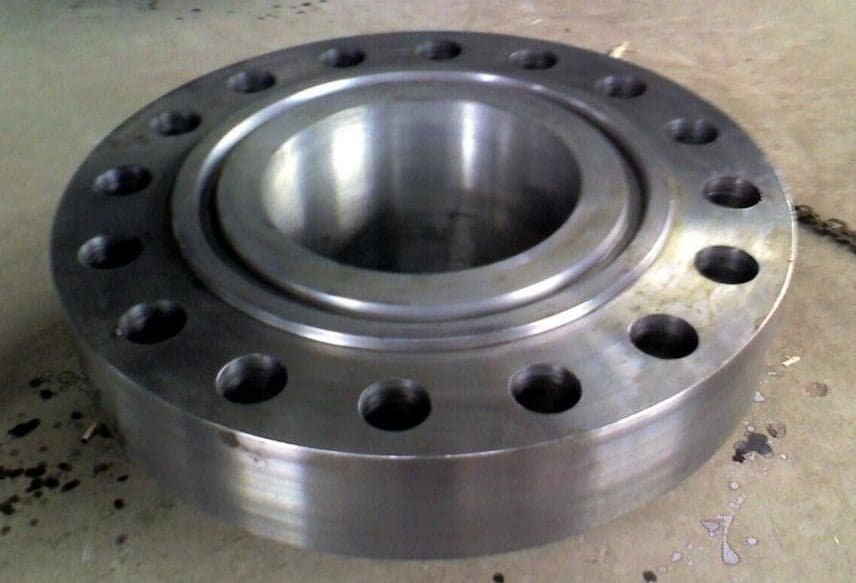
III. Common Flange Materials and Their Detailed Steel Grade Classifications
Flanges come in a multitude of materials, each with its unique properties and characteristics. Let’s explore the most commonly used flange materials and delve into their detailed steel grade classifications:
1. Carbon Steel Flanges:
- Steel Grades: Carbon steel flanges encompass a range of steel grades, including A105, A350 LF2, A694 F52, and more.
- Characteristics: Carbon steel flanges are known for their strength and durability. They excel in high-pressure and high-temperature environments.
- Advantages: These flanges are cost-effective, readily available, and offer excellent corrosion resistance in many settings.
- Suitable Scenarios: Carbon steel flanges are prevalent in industries such as oil and gas, petrochemicals, power generation, and construction.
2. Stainless Steel Flanges:
- Steel Grades: Stainless steel flanges are available in various grades, including 304, 316, 321, and 347, among others.
- Characteristics: Stainless steel flanges are prized for their exceptional corrosion resistance, making them ideal for harsh environments.
- Advantages: They excel in applications demanding hygiene, longevity, and resistance to corrosion and staining.
- Suitable Scenarios: Stainless steel flanges are commonly used in chemical processing, food and pharmaceutical industries, water treatment, and marine applications.
3. Alloy Steel Flanges:
- Steel Grades: Alloy steel flanges encompass a wide array of grades, such as F5, F9, F11, F22, and F91.
- Characteristics: Alloy steel flanges combine the strength of carbon steel with enhanced corrosion resistance and wear resistance.
- Advantages: Their versatility makes them suitable for high-stress environments requiring a combination of strength and corrosion resistance.
- Suitable Scenarios: Alloy steel flanges find applications in aerospace, automotive, offshore drilling, and other industries with demanding operating conditions.
In addition to the broad categories mentioned above, each of these flange materials offers a spectrum of steel grades with specific alloy compositions, ensuring precise suitability for a wide range of applications. When selecting a flange material, consider factors such as temperature, pressure, and the nature of the materials being transported, and refer to the detailed steel grade classifications to make an informed choice for your specific needs.

IV. Specialized Flange Materials
While carbon steel, stainless steel, and alloy steel are the workhorses of the flange world, there are situations where specialized materials are essential for unique industrial settings. Let’s take a closer look at some of these unconventional choices, highlighting their advantages and limitations:
1. Ceramic Flanges:
- Advantages: Ceramic flanges are prized for their exceptional resistance to extreme temperatures, corrosion, and abrasion. They are also chemically inert, making them ideal for highly corrosive environments.
- Limitations: Ceramics can be brittle and less forgiving under mechanical stress. They are often more expensive than traditional materials.
2. Plastic Flanges:
- Advantages: Plastic flanges, often made from materials like PVC, CPVC, or PTFE, offer superb corrosion resistance, especially in chemical processing applications. They are lightweight and cost-effective.
- Limitations: Plastic flanges may not withstand high temperatures and pressures as well as metal counterparts. They can also degrade when exposed to UV radiation.
3. Composite Material Flanges:
- Advantages: Composite flanges combine the strength of fiber-reinforced materials with corrosion resistance. They are lightweight and can offer tailored properties for specific applications.
- Limitations: Composite materials may have limited operating temperature ranges, and their long-term durability under extreme conditions requires careful consideration.
4. Titanium Flanges:
- Advantages: Titanium flanges are exceptionally corrosion-resistant, even in aggressive environments. They are also lightweight and possess excellent strength-to-weight ratios.
- Limitations: Titanium is relatively expensive and can be challenging to machine. Specialized equipment and expertise are often required.
The choice of specialized flange materials should align with the unique demands of your industrial setting. These materials offer distinct advantages in specific applications but may come with trade-offs. Careful consideration of factors like temperature, pressure, chemical exposure, and budget constraints is crucial when opting for specialized flanges. They are the tailored solutions for industries where standard materials may fall short in meeting the demands of extreme conditions and corrosive environments.

V. Importance of Flange Material Selection
Selecting the right flange material is a critical decision that profoundly influences the performance, longevity, and safety of piping systems. Let’s delve into why this choice matters and offer guidance to help readers make informed decisions for their specific applications.
1. Impact on Performance:
- Flange materials directly affect the overall performance of a piping system. Choosing the wrong material can lead to leaks, corrosion, and premature system failures.
- For instance, in high-temperature environments, selecting a material with poor heat resistance can result in deformations and compromised sealing, jeopardizing system integrity.
2. Safety Considerations:
- Safety is paramount in industrial operations. Inadequate flange material selection can lead to hazardous situations, environmental damage, and financial losses.
- In corrosive environments, the wrong material can deteriorate rapidly, potentially leading to chemical leaks or system failures that endanger personnel and the surroundings.
3. Environmental Impact:
- The choice of flange material also has environmental implications. Leaks and failures can lead to material wastage, environmental contamination, and costly cleanup efforts.
- Opting for a material with excellent corrosion resistance can reduce the risk of leaks and environmental harm.
Guidance for Flange Material Selection:
- Understand Your Operating Conditions: Consider factors such as temperature, pressure, and the nature of transported materials. Detailed knowledge of your specific operating conditions is essential.
- Consult with Experts: Engage with materials and engineering experts who can provide guidance tailored to your unique requirements. They can help identify suitable materials and grades.
- Consider Life Cycle Costs: While upfront costs matter, evaluating the long-term costs associated with maintenance, repair, and replacement is equally crucial. Some materials may have a higher initial cost but lower life cycle costs.
- Assess Compatibility: Ensure that the chosen flange material is compatible with other system components, including gaskets, seals, and bolts.
- Review Industry Standards: Familiarize yourself with industry standards and regulations that may dictate material requirements for specific applications.
In summary, the importance of selecting the right flange material cannot be overstated. It impacts performance, safety, and environmental considerations. By understanding your operating conditions, seeking expert advice, and considering long-term costs, you can make an informed choice that ensures the reliability and integrity of your piping systems.
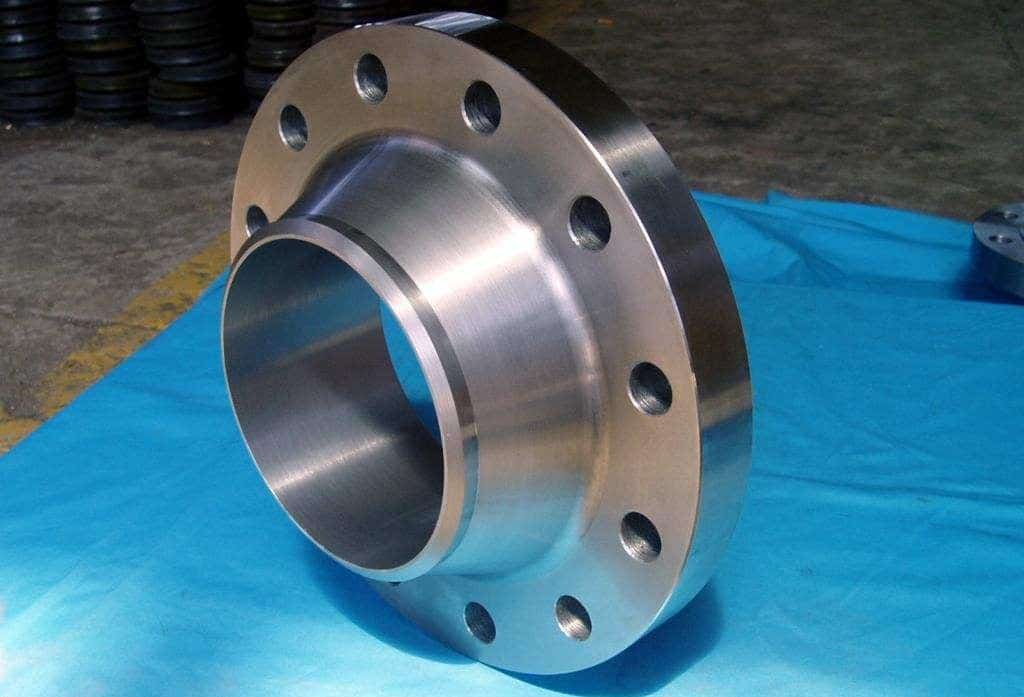
VI. Our Flange Solutions at YANHAO
At YANHAO, we take immense pride in our expertise and dedication to the world of flange manufacturing. With years of industry experience and a passionate team of experts, we’ve become a trusted name renowned for our commitment to precision engineering and unwavering customer satisfaction.
Our Extensive Flange Product Lineup:
At YANHAO, we offer a comprehensive range of flange products that cater to the diverse needs of industries across the globe. Our product lineup includes:
1. Carbon Steel Flanges: Our carbon steel flanges are designed to excel in applications where strength and reliability are paramount. Industries such as oil and gas have trusted our carbon steel flanges for their robust performance.
2. Stainless Steel Flanges: With a focus on corrosion resistance, our stainless steel flanges find their place in demanding environments like chemical processing and food production. They are built to withstand the toughest challenges.
3. Alloy Steel Flanges: YANHAO’s alloy steel flanges offer the perfect blend of strength and resistance, making them the preferred choice for projects in aerospace, automotive, and offshore drilling.
4. Specialized Flange Materials: We understand that sometimes, standard materials just won’t cut it. That’s why we offer specialized flange materials, including ceramics and composite materials, tailored for unique industrial settings.
At YANHAO, we recognize that material choice is a crucial aspect of any project. That’s why we provide a wide spectrum of options, ensuring that our customers have access to precisely what they need. Whether you require durability, corrosion resistance, or a specialized solution, YANHAO is here to meet your demands with the expertise and product range you can trust.
Author: Lewis Liu
Hello, my name is Lewis Liu, and I’m a professional sales engineer with over a decade of expertise in the flange fittings sector.
I am quite informed about flange selection, installation, and maintenance. I am passionate about providing customers with the greatest solutions for keeping their pipeline systems running smoothly, safely, and dependably.
If you have any queries or concerns concerning flange fittings for your pipelines, whether they are about selection, material choice, specification requirements, or anything else, please contact me at any time. I am dedicated to providing expert advice and assistance to help you make educated decisions and reach your objectives.
