What materials are used for flanges?
Flanges serve as vital components in connecting pipes and ensuring leak-free operations across various industries. The selection of appropriate materials for flange construction is crucial for optimal performance and longevity. In this blog, we will explore the different materials commonly used for flanges and delve into their unique characteristics. By understanding these materials, you can make informed decisions to meet the specific requirements of your projects or applications. Let’s dive into the world of flange materials and unlock the secrets behind their strength, durability, and reliability.
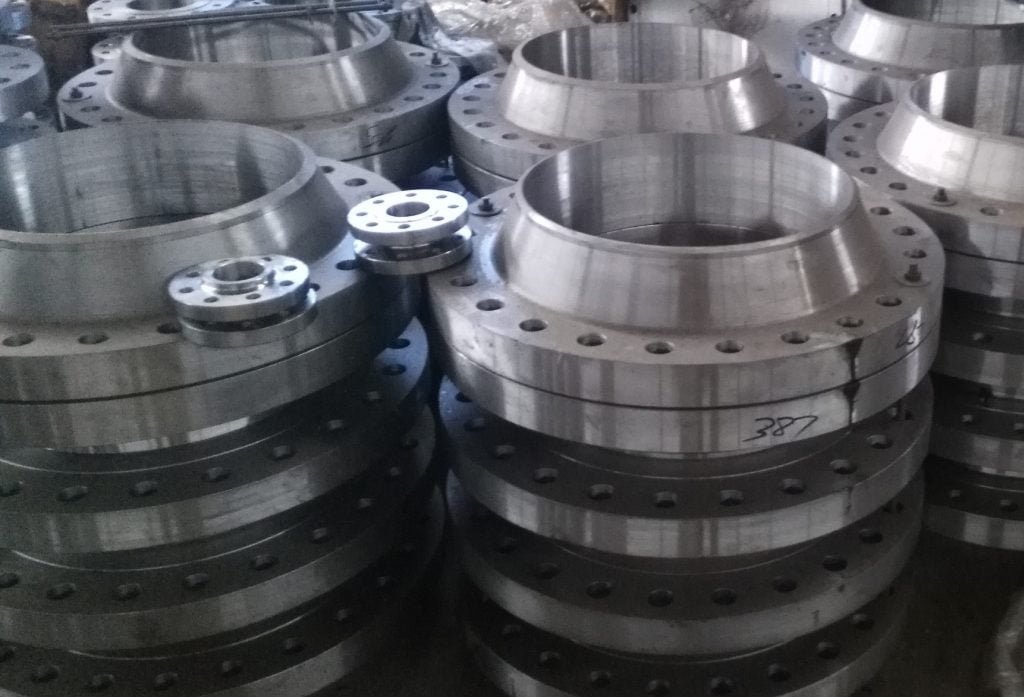
I. Understanding Flanges
A. Definition and function of flanges:
Flanges are mechanical components that are used to connect pipes, valves, pumps, and other equipment together. They provide a secure and leak-proof joint, ensuring the fluid or gas contained within the system remains contained. Flanges are typically flat, circular discs with evenly spaced holes for bolts or studs to pass through, enabling easy assembly and disassembly of the joint.
B. Significance of selecting appropriate materials for flange construction:
Selecting the right material for flange construction is crucial as it directly impacts the performance and reliability of the joint. The material needs to be compatible with the fluids or gases being transported, resist corrosion and wear, withstand high temperatures and pressures, and maintain structural integrity.
Using inappropriate material can lead to leaks, failures, and potential safety hazards. Additionally, the right material choice can help reduce maintenance costs, improve system efficiency, and extend the lifespan of the flange. Therefore, thoroughly understanding the properties and limitations of different materials is essential for selecting the appropriate material for flange construction.
II. Common Materials Used for Flanges
A. Carbon Steel
- Description and properties:
Carbon steel is a widely used material for flanges due to its strength, affordability, and versatility. It contains a combination of iron and carbon, with carbon content ranging from 0.05% to 1.5%. The properties of carbon steel can vary depending on the carbon content and heat treatment, but it generally offers good tensile strength, durability, and resistance to high temperatures. - Advantages and limitations:
i. Advantages:- Cost-effective: Carbon steel flanges are relatively inexpensive compared to other materials, making them ideal for budget-conscious projects.Good mechanical properties: Carbon steel provides excellent strength and rigidity, ensuring reliable performance under high pressures and temperatures.Easy availability: Carbon steel is readily available in various grades and sizes, making it accessible for most applications.
- Corrosion susceptibility: Carbon steel is prone to corrosion, especially in environments with high moisture or aggressive chemicals. To mitigate this, coatings or surface treatments may be required.
- Lower resistance to certain chemicals: Carbon steel may not be suitable for applications involving strong acids or corrosive substances without proper protection.
- Suitable applications:
Carbon steel flanges are commonly used in a wide range of applications, including:
- Oil and gas pipelines
- Water and wastewater systems
- Power plants
- Petrochemical industries
- HVAC systems
- General plumbing and industrial piping
B. Stainless Steel
- Description and properties:
Stainless steel is a popular choice for flanges due to its excellent corrosion resistance and aesthetic appeal. It is an alloy of iron with a minimum chromium content of 10.5%, which provides a protective layer of chromium oxide on the surface, preventing rust and corrosion. Stainless steel is available in various grades, each offering unique properties to suit different applications. - Advantages and limitations:
i. Advantages:- Superior corrosion resistance: Stainless steel flanges exhibit excellent resistance to corrosion from moisture, chemicals, and high temperatures, making them suitable for a wide range of environments.Hygienic properties: Stainless steel is non-porous, easy to clean, and resistant to bacterial growth, making it ideal for applications in the food, pharmaceutical, and medical industries.Aesthetic appeal: Stainless steel flanges have an attractive and modern appearance, making them suitable for architectural and decorative purposes.
- Higher cost: Compared to carbon steel, stainless steel is generally more expensive, which can impact project budgets.
- Lower temperature capability: Certain grades of stainless steel may have lower resistance to extremely high or low temperatures, affecting their suitability for specific applications.
- Suitable applications:
Stainless steel flanges are commonly used in a variety of applications, including:
- Food and beverage processing
- Chemical processing plants
- Water treatment facilities
- Pharmaceutical industries
- Marine and offshore systems
- Architectural and decorative purposes
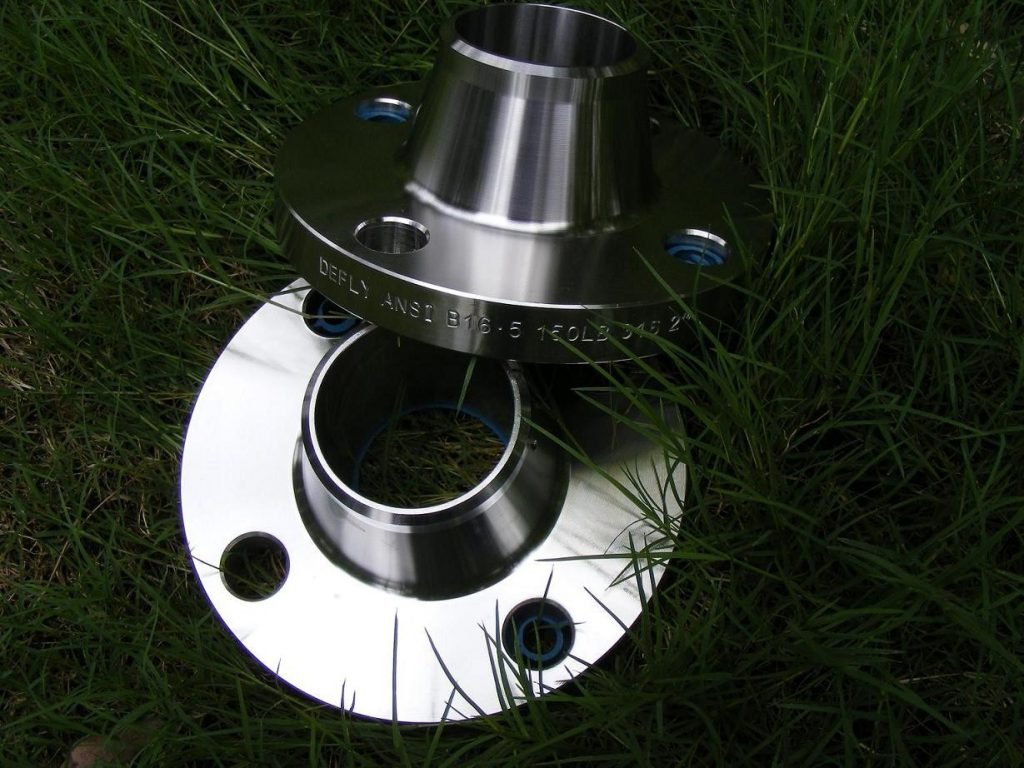
C. Alloy Steel
- Description and properties:
Alloy steel is a type of steel that is alloyed with various elements to enhance its properties. Common alloying elements include chromium, nickel, molybdenum, and vanadium. The addition of these elements improves the strength, hardness, and corrosion resistance of the steel. Alloy steel flanges have superior mechanical properties compared to carbon steel flanges. - Advantages and limitations:
i. Advantages:- High strength and toughness: Alloy steel flanges possess excellent strength and toughness, making them suitable for applications with high pressure and temperature requirements.Enhanced corrosion resistance: Alloying elements such as chromium and nickel improve the corrosion resistance of alloy steel flanges.
- Higher cost: Alloy steel flanges are generally more expensive than carbon steel flanges due to the cost of alloying elements.
- Specific temperature limitations: Some alloy steels may have limitations in high-temperature applications, requiring careful selection based on the specific temperature range.
- Suitable applications:
Alloy steel flanges are commonly used in various applications that require higher strength, corrosion resistance, and temperature resistance, including:
- Oil and gas industry
- Power plants
- Chemical processing plants
- Aerospace industry
- High-pressure and high-temperature systems
D. Duplex Steel
- Description and properties:
Duplex steel is a type of stainless steel that contains a balanced mixture of ferrite and austenite microstructures. It typically consists of high levels of chromium, nickel, and molybdenum, which provide excellent corrosion resistance and mechanical properties. Duplex steel flanges are known for their exceptional strength and resistance to stress corrosion cracking. - Advantages and limitations:
i. Advantages:- Superior corrosion resistance: Duplex steel flanges offer excellent resistance to a wide range of corrosive environments, such as chloride-containing solutions, making them suitable for applications in the chemical industry and offshore environments.High strength: Duplex steel has higher strength compared to standard stainless steel, allowing for thinner flanges and reducing weight and cost.Good weldability: Duplex steel has good weldability, enabling ease of fabrication.
- Higher cost: Duplex steel may be more expensive than standard stainless steel, which can impact project budgets.
- Limited availability of sizes: Duplex steel flanges might have limited availability in certain sizes and configurations compared to other materials.
- Suitable applications:
Duplex steel flanges are commonly used in various industries where high strength and excellent corrosion resistance are required, including:
- Oil and gas industry
- Chemical processing plants
- Desalination plants
- Marine and offshore systems
- Pulp and paper industry

E. Non-Metallic Materials (e.g., PVC, HDPE)
- Description and properties:
Non-metallic materials such as PVC (Polyvinyl Chloride) and HDPE (High-Density Polyethylene) are commonly used for flanges in certain applications. These materials offer specific properties that make them suitable for certain environments. PVC is a thermoplastic material known for its chemical resistance and affordability. HDPE is a thermoplastic polymer with high strength, durability, and excellent chemical resistance. - Advantages and limitations:
i. Advantages:- Chemical resistance: Non-metallic flanges made of materials like PVC and HDPE are highly resistant to chemicals, acids, and alkalis, making them suitable for handling corrosive fluids. Lightweight: Non-metallic flanges are lighter compared to metallic flanges, making them easier to handle and install. Cost-effective: PVC and HDPE flanges are often more economical compared to metallic flanges.
- Temperature limitations: Non-metallic flanges may have limitations in high-temperature applications as they may deform or lose their strength.
- Lower pressure rating: Non-metallic flanges typically have lower pressure ratings compared to metallic flanges.
- Limited compatibility: Non-metallic materials may not be suitable for certain aggressive chemicals or extreme temperature environments.
- Suitable applications:
Non-metallic flanges are commonly used in various applications requiring corrosion resistance and moderate pressure/temperature conditions, including:
- Water and wastewater treatment plants
- Chemical processing industries
- Food and beverage industries
- Irrigation systems
- HVAC systems

III. Factors Influencing the Selection of Flange Materials
A. Pressure and temperature requirements:
The pressure and temperature conditions of the system play a crucial role in determining the suitable material for flanges. Materials with higher tensile strength and resistance to deformation are chosen for high-pressure applications. Similarly, materials with high-temperature resistance are selected for systems operating at elevated temperatures.
B. Corrosion resistance:
The corrosive nature of the fluid or environment in which the flanges will be used is another essential factor to consider. Different materials exhibit varying levels of resistance to corrosion from specific chemicals, acids, alkalis, or seawater. The material chosen should have appropriate corrosion resistance to ensure the longevity and reliability of the flanges.
C. Cost considerations:
Cost considerations play a significant role in material selection. The availability and market price of materials are important factors to consider while balancing the desired properties of the flanges with cost-effectiveness. Sometimes, alternative materials may be chosen if they offer similar performance at a lower cost.
D. Industry-specific requirements:
Various industries have specific requirements that influence the selection of flange materials. For example, industries such as oil and gas, chemical processing, and marine have unique demands for high-pressure, high-temperature, and corrosive environments. It is essential to consider industry-specific regulations, safety standards, and material certifications when choosing flange materials.
E. Future advancements and emerging materials for flanges:
Advancements in material science and engineering lead to the development of new materials or improved versions of existing materials. It is important to stay updated on the latest developments in flange materials and consider emerging materials that might offer enhanced properties or lower costs.
Overall, the selection of flange materials should be based on a comprehensive evaluation of various factors, including pressure and temperature requirements, corrosion resistance, cost considerations, industry-specific requirements, and awareness of future advancements in materials. Consulting with experts and considering the specific needs of the application is crucial for making the best material selection decision.

IV.Conclusion
Flanges are important components in piping systems because they provide a method to connect and disconnect pipes or equipment, facilitate fluid flow, and create a secure seal. They can be made from various materials, including both metallic and non-metallic options. Metallic materials such as carbon steel, stainless steel, and alloy steel offer high strength, excellent temperature resistance, and good corrosion resistance. Non-metallic materials like PVC and HDPE provide corrosion resistance, cost-effectiveness, and lightweight properties. Each material has its own advantages and limitations, making it suitable for specific applications.
Selecting the correct material for flange construction is crucial to ensure the performance, lifespan, and safety of the piping system. Factors such as pressure and temperature requirements, corrosion resistance, cost considerations, industry-specific requirements, and emerging materials must be taken into account. By carefully evaluating these factors and consulting with experts, the most suitable material can be chosen to meet the specific needs of the application. Careful material selection ultimately ensures that the flanges function optimally and contribute to efficient and reliable fluid handling processes.
As a leading China flange manufacturer, Hebei Yanhao Pipeline Equipment Co., Ltd. has extensive experience and expertise and is committed to providing customers with high-quality products and satisfactory services. We offer flanges in various materials and standard specifications. Our products are of good quality and affordable prices, creating the opportunity for long-term cooperation with stable supply. We look forward to establishing a long-term and stable partnership with you.
Author: Lewis Liu
Hello, my name is Lewis Liu, and I’m a professional sales engineer with over a decade of expertise in the flange fittings sector.
I am quite informed about flange selection, installation, and maintenance. I am passionate about providing customers with the greatest solutions for keeping their pipeline systems running smoothly, safely, and dependably.
If you have any queries or concerns concerning flange fittings for your pipelines, whether they are about selection, material choice, specification requirements, or anything else, please contact me at any time. I am dedicated to providing expert advice and assistance to help you make educated decisions and reach your objectives.
