Why are flanges so important for pipe fittings?
Flanges play a vital role in pipe fittings, providing reliable connections, sealing, and structural support to ensure the integrity, safety, and efficiency of piping systems. They serve a variety of functions and are suitable for different types, sizes, and materials of pipes. Flanges adhere to industry standards and provide convenient access for inspection and maintenance work. This article will discuss why flanges are crucial and explore their key functions and advantages.

1. Connection
Flanges serve as a crucial element in connecting pipes and pipe components, providing a secure and leak-proof connection. By using bolts or welding, flanges firmly join two pipes together, ensuring a robust and reliable connection. The use of flanges allows for easy installation, disassembly, and maintenance of the pipeline system. With their adjustable nature, flanges enable flexible positioning of pipes, allowing for proper alignment and avoiding misalignment or deviation. This ensures fluid or gas can flow smoothly through the pipeline without any leakage or loss of pressure. Furthermore, flanges provide a convenient means to connect pipes of different sizes or materials, making them indispensable in various industrial applications.
2. Strength and stability
Flanges not only provide a secure connection but also significantly contribute to the strength and stability of pipe joints. The design and material composition of flanges enable them to distribute the load, pressure, and stress evenly across the joint, minimizing the risk of pipe failure or leakage.
When pipes are connected using flanges, the forces exerted on the joint are spread out over a larger area, reducing the concentration of stress. This helps to prevent the premature deterioration of the pipe by minimizing the potential for fatigue cracking or deformation. The load-bearing capacity of flanges allows them to withstand high-pressure applications commonly encountered in industries such as oil and gas, petrochemicals, and power generation.
Moreover, flanges offer enhanced stability to pipe connections. By providing rigid support and reinforcement, they help to prevent the movement or displacement of pipes under dynamic or vibrational conditions. This stability is particularly crucial in systems where pipes are subject to mechanical stresses, such as cooling water, steam, or fluid transmission pipelines.
The robustness of flange connections also gives them the ability to resist bending or distortion. When exposed to external forces or temperature fluctuations, flanges maintain their structural integrity, ensuring the reliability and durability of the piping system. Additionally, the use of proper gaskets further enhances the sealing capability of the flange connection by providing an additional layer of protection against leakage.
In summary, flanges contribute to the strength and stability of pipe connections by distributing the load and stress evenly, resisting bending or distortion, and providing rigid support. Their ability to withstand high pressures and maintain a secure joint makes them essential for ensuring the integrity and longevity of piping systems under various operating conditions.

3. Sealing capabilities
Flanges, in conjunction with gaskets, offer excellent sealing capabilities, providing a crucial barrier against the leakage of fluids or gases in a piping system. The gasket placed between the flange faces acts as a compressible material, creating a tight and reliable seal.
The gasket’s selection and installation play a significant role in achieving an effective seal. Different types of gaskets, such as spiral wounds, ring joints, or soft-cut gaskets, are available to suit various applications and operating conditions. Factors such as temperature, pressure, chemical compatibility, and flange surface finish are considered when choosing the appropriate gasket.
Flange gaskets are designed to deform under pressure, filling any irregularities or imperfections in the flange faces. This ensures a uniform distribution of the compressive forces and helps to compensate for any slight misalignment between the flanges. The gasket material, typically made from materials like rubber, Teflon, or graphite, provides elasticity and resilience, allowing it to conform to the flange surfaces and maintain a leak-free joint.
The sealing capabilities of flanges and gaskets are crucial in processes that involve hazardous or corrosive substances. Even a small leak can have severe consequences, such as environmental contamination, safety hazards, or loss of valuable resources. Flanges with properly selected and installed gaskets effectively contain the flow of materials, preventing any escape or contamination.
Regular inspection and maintenance of flange connections are essential to ensure the integrity of the sealing system. This includes checking for signs of leakage, tightening bolts if necessary, and replacing gaskets as needed. Maintaining a reliable seal, flanges and gaskets contribute to the overall efficiency, safety, and environmental sustainability of the piping system.

4. Versatility
Flanges offer a high level of versatility due to their availability in various types, sizes, and materials. This allows for seamless integration into different piping systems and the connection of diverse pipe materials.
Flanges are available in different types such as slip-on, weld neck, blind, lap joint, threaded, and socket weld. Each type is designed for specific applications and offers distinct advantages in terms of installation ease, strength, and sealing capabilities. The ability to choose from different flange types enables engineers and designers to select the most suitable option for their specific needs.
In addition to different types, flanges come in various sizes and pressure ratings. This ensures compatibility with the pipe dimensions and system requirements. Whether it is a small, low-pressure pipe or a large, high-pressure pipeline, flanges can be selected to match the specific size and pressure requirements.
Furthermore, flanges are compatible with different pipe materials, including steel, stainless steel, cast iron, and PVC. This compatibility allows for versatility in connecting pipes made from different materials. For example, a steel flange can be used to connect a steel pipe to a cast iron pipe, providing a secure and reliable joint.
The ability to connect different pipe materials using flanges is particularly valuable in situations where different materials may be required for specific purposes. For instance, a stainless steel pipe may be necessary in a corrosive environment, while a PVC pipe may be suitable for a non-corrosive application. Flanges enable the seamless integration of these pipes by providing a common connection point.
Overall, the availability of different flange types, sizes, and materials enhances the versatility of flanges, allowing them to be used in a wide range of applications and enabling the connection of various pipe materials. This flexibility contributes to the adaptability and efficiency of piping systems in diverse industries and applications.
5. Accessibility
Flanges provide excellent accessibility for inspection and servicing, making maintenance activities more efficient and convenient. When a specific section of the pipeline requires repair or maintenance, flanges allow for easy disconnection and reconnection of the affected component without disrupting the entire system.
By using flanges, maintenance personnel can disconnect two flanged components by simply removing the bolts connecting them. This enables easy access to the specific area that needs attention, whether it’s a valve, pump, or any other component. Since the flanges can be easily separated, there is no need to dismantle the entire pipeline, which saves considerable time and effort.
Flanges also facilitate swift reconnection once the repair or maintenance work is complete. The component can be easily reattached by aligning the flange bolt holes and securing the bolts. This quick reconnection minimizes downtime during maintenance activities, allowing the system to be brought back online promptly.
The accessibility provided by flanges is particularly beneficial in situations where regular inspection and servicing are required. Flanges enable routine checks of components, such as valves or filters, ensuring optimal performance and identifying any potential issues promptly.
Additionally, the use of flanges allows for easier replacement of components when necessary. If a valve or pump needs to be replaced, it can be readily disconnected and a new one installed using flanges, saving time and minimizing disruption to the overall system.
In summary, the accessibility provided by flanges simplifies inspection and servicing activities. By allowing easy disconnection and reconnection of pipeline components, flanges facilitate efficient maintenance, minimize downtime, and contribute to the overall reliability and longevity of the system.
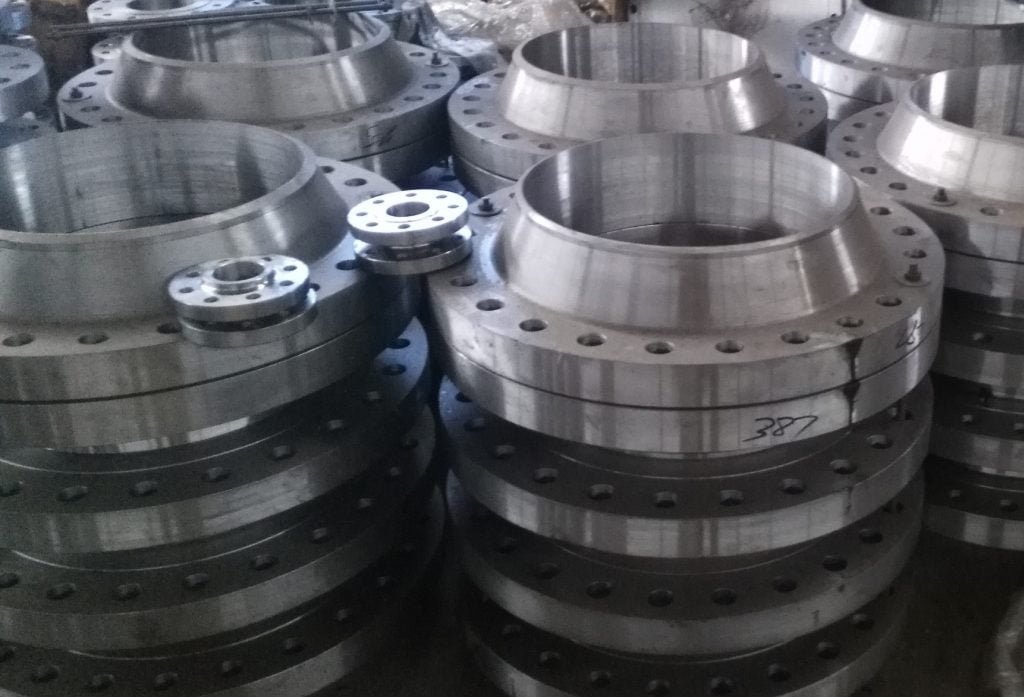
6. Standardization
Flanges adhere to widely recognized industry standards, such as ANSI (American National Standards Institute), ASME (American Society of Mechanical Engineers), and API (American Petroleum Institute), among others. These standards ensure uniformity and compatibility among different manufacturers and suppliers, simplifying the selection process and promoting interchangeability.
One of the key advantages of standardization is that it establishes guidelines for the dimensions, materials, and ratings of flanges. This means that flanges produced by different manufacturers will have consistent sizes, allowing for easy integration into various piping systems. Engineers and designers can rely on these standardized dimensions when selecting flanges, ensuring that they will fit and function properly with other pipeline components.
Moreover, the use of standard materials specified in these industry standards guarantees the necessary strength, corrosion resistance, and durability of flanges. For example, the ASME B16.5 standard specifies materials such as carbon steel, stainless steel, and alloy steel for flanges, ensuring compatibility with different applications and environments. This standardization of materials allows engineers to confidently choose flanges that will meet the specific requirements of their projects.
Industry standards also provide ratings for flanges, such as pressure classes, temperature ranges, and load capacities. These ratings ensure that flanges are suitable for the intended applications and operating conditions. By following these established guidelines, manufacturers can produce flanges with the necessary strength and performance characteristics, and users can select flanges that meet the required specifications.
The standardization of flanges simplifies the selection process for engineers and designers, as it ensures that flanges with the required dimensions, materials, and ratings are readily available in the market. This reduces the time and effort spent on sourcing and ensures compatibility among different components from various suppliers.
In summary, adherence to recognized industry standards for flanges promotes standardization, uniformity, and compatibility. This simplifies the selection process, guarantees interchangeability among different manufacturers, and ensures that flanges meet the necessary specifications for dimensions, materials, and ratings.
7. Conclusion
In conclusion, flanges are critical components in piping systems that play a vital role in ensuring the integrity, safety, and efficiency of the system. They provide reliable connections, leak-proof sealing, and structural support, contributing to the smooth operation of pipelines in various industries. By preventing accidental disconnection and leakage, flanges help maintain the overall performance of the system and minimize downtime. Their ability to withstand challenging operating conditions makes them essential for maintaining the integrity of the piping system. Overall, flanges are integral for the effective and safe functioning of piping systems.
Author: Lewis Liu
Hello, my name is Lewis Liu, and I’m a professional sales engineer with over a decade of expertise in the flange fittings sector.
I am quite informed about flange selection, installation, and maintenance. I am passionate about providing customers with the greatest solutions for keeping their pipeline systems running smoothly, safely, and dependably.
If you have any queries or concerns concerning flange fittings for your pipelines, whether they are about selection, material choice, specification requirements, or anything else, please contact me at any time. I am dedicated to providing expert advice and assistance to help you make educated decisions and reach your objectives.
