How to Prevent Pipe Flange Corrosion?
I. Introduction
Pipe flanges are the essential components used to connect pipes, valves, and other equipment to create a pipeline system. However, these flanges are often exposed to harsh and corrosive environments that can lead to their failure over time. The failure of pipe flanges can result in costly downtime, loss of production, and even hazardous material leaks. Therefore, preventing pipe flange corrosion is crucial to ensure the continued operation and safety of the equipment.
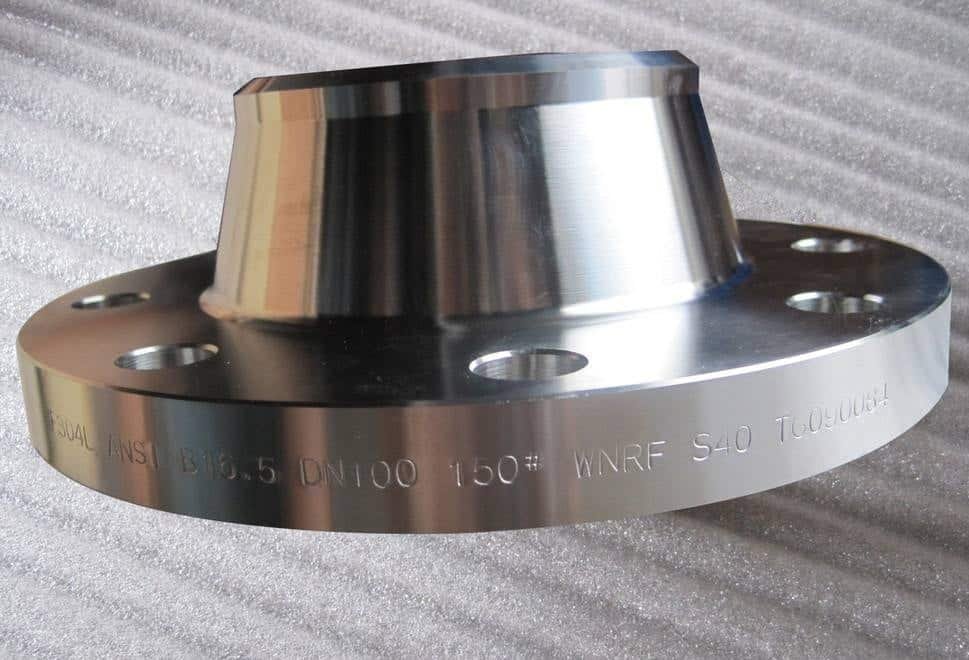
The purpose of this blog is to provide expert insights on how to prevent pipe flange corrosion. This blog will discuss the various types of corrosion, factors that influence corrosion, and prevention techniques such as material selection, design considerations, and maintenance strategies. Real-world examples and case studies will be presented to illustrate the importance of preventing pipe flange corrosion. By the end of this blog, readers will gain a deep understanding of pipe flange corrosion and learn effective strategies to prevent it.
II. Causes of Pipe Flange Corrosion
A. Chemical corrosion: This type of corrosion occurs when the material is attacked by a chemical agent, such as acids, bases, or salts. Chemical corrosion can occur on various materials used to make flanges, including stainless steel, carbon steel, and nickel alloys.
B. Electrochemical corrosion: Electrochemical corrosion is the most common type of corrosion that affects pipe flanges. This type of corrosion occurs when two different metals come into contact with each other, causing a flow of electric current. The flow of electrical current leads to the breakdown of the metal and causes corrosion.
C. Microbiologically induced corrosion: Microbiologically induced corrosion is caused by microorganisms, such as bacteria and fungi, that grow inside or on the surface of the flange material. The microorganisms produce biogenic sulfides that react with the material causing corrosion.
Understanding the main causes of pipe flange corrosion is essential for preventing corrosion and determining the proper prevention technique for a specific type of corrosion.
III. Prevention Methods
A. Material selection:
The selection of the right material for the flange is crucial to prevent corrosion. The following materials can be used for flanges to prevent corrosion:
- Stainless steel: Stainless steel flange is corrosion-resistant and does not rust or stain easily. It is ideal for use in corrosive environments.
- Corrosion-resistant alloys: Corrosion-resistant alloys, such as Monel, Inconel, and Hastelloy, are specially designed to withstand corrosive environments.
- Coatings: Protective coatings, such as paint and epoxy coatings, can also be applied to flanges to prevent corrosion.
B. Design considerations:
Proper gasket selection, appropriate flange face finish, and corrosion-resistant bolts and nuts can also help prevent pipe flange corrosion.
- Proper gasket selection: Selecting the right gasket material is essential to prevent galvanic corrosion and other types of corrosion.
- Appropriate flange face finish: Maintaining an appropriate flange face finish can help prevent leaks and minimize corrosion.
- Corrosion-resistant bolts and nuts: Using corrosion-resistant bolts and nuts, such as Teflon-coated or stainless steel, can also prevent corrosion.
C. Maintenance and inspection:
- Regular cleaning and inspection: Regular cleaning and inspection of the flange and the surrounding environment can identify corrosion issues and prevent further corrosion damage.
- Prompt repair of defects: Prompt repair or replacement of damaged parts can prevent corrosion from spreading and further damaging the pipeline system.
- Use of inhibitors and cathodic protection: The use of inhibitors and cathodic protection can also prevent pipe flange corrosion by slowing down the rate of corrosion.
By implementing these prevention methods, it is possible to prevent pipe flange corrosion and ensure the continuous operation and safety of the pipeline system.
IV. Case Studies
A. Real-world examples of pipe flange corrosion:
There are many real-world examples of pipe flange corrosion, including:
- A chemical processing plant experienced multiple leaks in its pipeline system due to severe corrosion of the flanges. The corrosion was caused by exposure to acidic substances, and the plant had to shut down for repairs.
- A drilling rig in the offshore oil and gas industry had frequent issues with flange corrosion due to saltwater exposure and stress cracking. This led to costly maintenance and safety concerns for the workers.
B. Analysis of corrosion causes and prevention methods:
In both examples, the root cause of the flange corrosion was identified to be exposed to corrosive substances and environments. The prevention methods used to address these issues include:
- Material selection: Using corrosion-resistant materials such as stainless steel or corrosion-resistant alloys helped prevent corrosion.
- Coatings: Applying protective coatings to the flanges can help prevent corrosion.
- Design considerations: Designing the flanges with an appropriate flange face finish and selecting the right gasket material can reduce the risk of corrosion.
- Maintenance and inspection: Regular cleaning and inspection can help identify corrosion issues and prevent further damage.
C. Lessons learned and best practices:
The lessons learned from these real-world examples include:
- Proper material selection is crucial in preventing corrosion in flanges.
- Regular maintenance and inspection can help identify corrosion issues before they become major problems.
- The use of protective coatings can help prevent corrosion in corrosive environments.
Overall, by correctly identifying the causes of pipe flange corrosion, implementing prevention methods, and conducting regular maintenance, companies can minimize downtime, improve safety and reduce costs.
V. Conclusion
In conclusion, it is essential to implement the correct prevention methods to avoid pipe flange corrosion. This includes selecting the right materials, designing appropriate flanges, and following best practices for maintenance and inspection. Regular maintenance and inspection are crucial in identifying corrosion issues before they become major problems.
If you have pipe flange requirements or technical questions, feel free to reach out to our company for free technical support and detailed solutions. We recommend working with a professional flange company to ensure that the selected materials and designs meet the required usage and safety standards, ensuring equipment reliability and safety.
By taking effective preventative measures, companies can reduce maintenance costs, minimize downtime, improve production efficiency, and ensure equipment reliability and safety.
Author: Lewis Liu
Hello, my name is Lewis Liu, and I’m a professional sales engineer with over a decade of expertise in the flange fittings sector.
I am quite informed about flange selection, installation, and maintenance. I am passionate about providing customers with the greatest solutions for keeping their pipeline systems running smoothly, safely, and dependably.
If you have any queries or concerns concerning flange fittings for your pipelines, whether they are about selection, material choice, specification requirements, or anything else, please contact me at any time. I am dedicated to providing expert advice and assistance to help you make educated decisions and reach your objectives.
