Corrosion-Resistant Flanges: Key Factors and How to Choose
The first thing you should understand about corrosion-resistant flanges is that they are not interchangeable with stainless steel flanges. Due to its exceptional corrosion resistance, stainless steel flanges are frequently utilized in corrosive media, high temperature, and high pressure pipeline systems; however, stainless steel is not the only material that can be used to create corrosion-resistant flanges.
Carbon steel flanges are a viable option in several application circumstances because they are reasonably priced, have good mechanical and processing properties, and both. Furthermore, the implementation of corrosion-resistant flanges is contingent upon the flange’s material composition as well as additional protective measures, including clamp seals, protective covers, and the like, which can enhance the flanges’ resistance to corrosion.
Let’s first look at the common types of concentrated flange corrosion

Crevice corrosion: Due to the complex geometry of the flange connection, gaps between the two flange surfaces are very likely to appear. These gaps provide conditions for corrosion, especially in a small space, impurities such as dust and salt are easy to accumulate, leading to rapid corrosion.

Galvanic corrosion: When there is a difference in potential between different metals, a galvanic pair is formed, causing the metal with lower potential to corrode. If you do not pay attention to the selection of materials in flange design, especially when connecting flange surfaces of different materials together, or using metal gaskets of different materials from the flange surface, galvanic corrosion will occur.
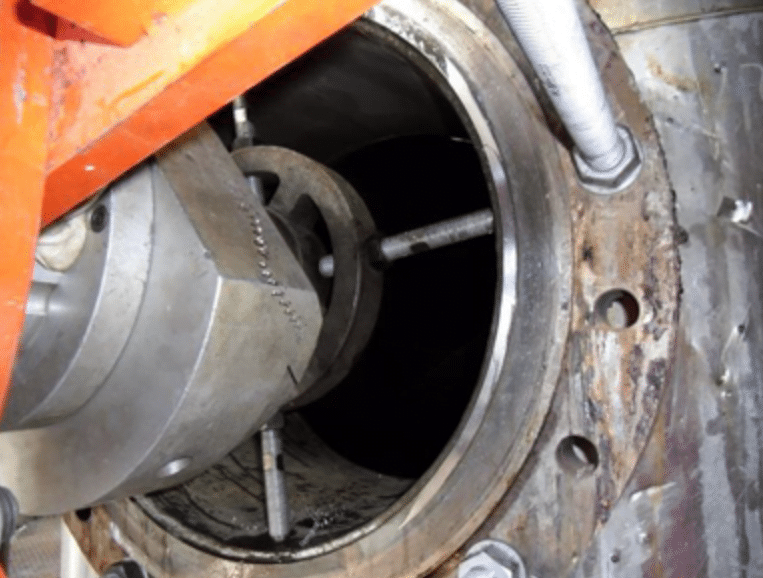
Chemical corrosion: Metal deterioration is caused by a direct chemical reaction between the metal and the surrounding medium that does not produce current. This type of corrosion comprises non-electrolytic solution and high-temperature dry gas corrosion of metal.

Atmospheric corrosion: Caused by oxidation events that take place when a metal comes into direct contact with the atmosphere. These reactions are brought on by the presence of oxygen, humidity, temperature, and other elements in the atmosphere. Because of the high levels of moisture and salt in the air, this corrosion phenomena is more noticeable, especially in coastal areas.

Microbial corrosion: Under some conditions, microbes can potentially corrode metal. Through their metabolic processes, these microbes create acidic chemicals, which speeds up the metal’s corrosive process.
Flange corrosion may lead to serious consequences

Flange corrosion is a complex process that involves chemical or electrochemical reactions between the metal and the surrounding medium, causing the metal to enter an oxidized (ion) state. This corrosion will significantly reduce the strength, plasticity, toughness and other mechanical properties of metal materials, destroy the geometric shape of metal components, increase wear between parts, deteriorate physical properties such as electrical and optical properties, and thus shorten the service life of the equipment.
Corrosion not only affects the flange itself, but may also affect the bolts connected to it, causing the bolt strength to decrease and unable to withstand the shared tensile force, which in turn causes fracture. When a severely corroded bolt cannot withstand the shared tensile force and breaks, the tensile force normally borne by the bolt is instantly shared by other bolts on the same flange, which can easily cause other bolts with similar corrosion to break in a chain, thereby causing a large amount of leakage of the medium inside the pipeline.
This leakage may not only cause production interruption, but also cause catastrophic accidents such as fire or explosion due to the leakage of the medium encountering open flames or other heat sources.
Common methods to deal with flange corrosion
The methods to deal with flange corrosion mainly include paint maintenance, protective cover protection, tape or semi-solid anti-corrosion tape protection, hot-melt plastic anti-corrosion, etc.

Be sure to regularly inspect and maintain the flanges and replace any problematic flanges in time. If you have any questions about the maintenance and care of the flanges, you can contact YANHAO at any time, and our professional engineers will answer your questions.
Methods above can effectively prevent corrosion of flanges, but choosing the appropriate flange material from the beginning can prevent corrosion to the greatest extent.
Choose the right flanges material
The materials of anti-corrosion flanges include carbon steel, stainless steel, alloy steel, copper and copper alloys, plastics, ceramics, aluminum alloys, nickel alloys, etc. The anti-corrosion requirements of flanges vary in different industrial applications, so it is crucial to choose the right material. The following are some common anti-corrosion flange materials and their applicable scenarios:

Carbon steel flanges: Suitable for general low and medium pressure occasions, with good mechanical properties and processing properties, and relatively low prices.

Stainless steel flanges: Suitable for corrosive environments or occasions that require wear resistance, such as chemical and food industries, with excellent corrosion resistance.
Our company provides Stainless Steel Flanges in various types>>
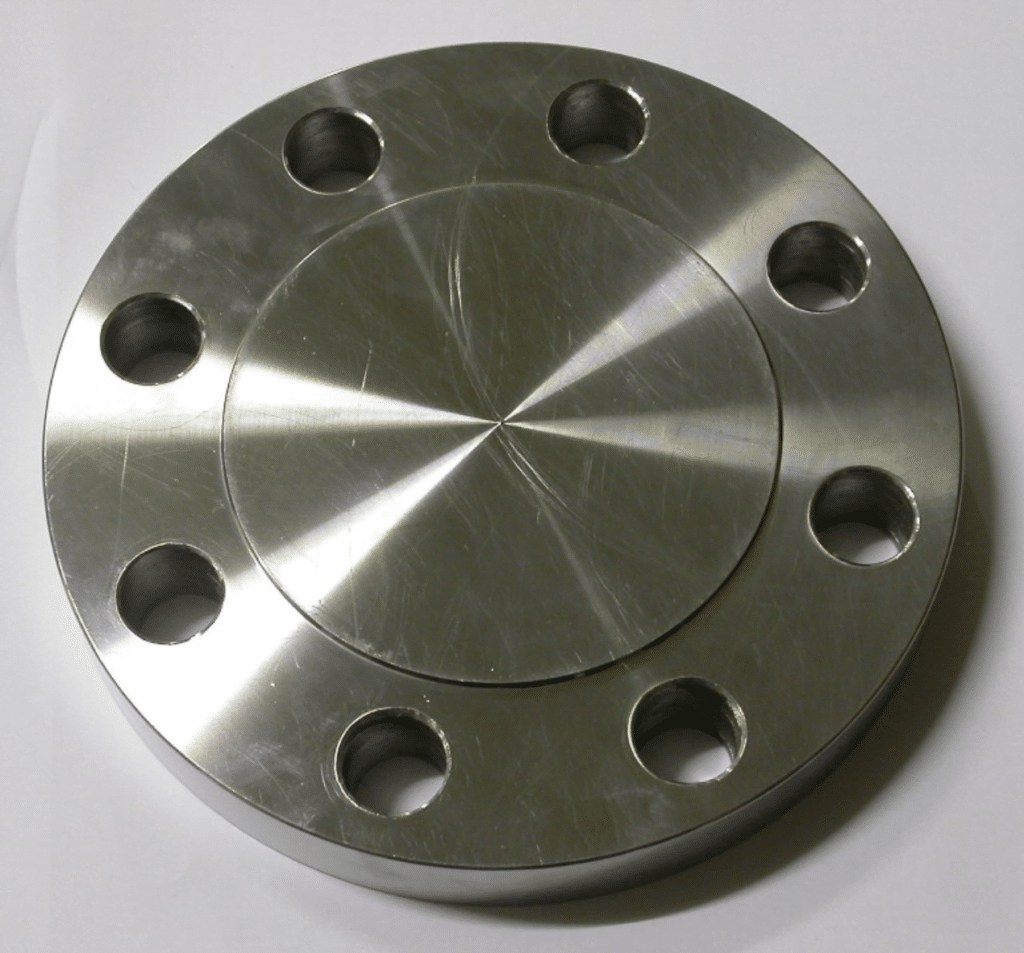
Alloy steel flanges: Suitable for high pressure or high temperature environments, such as high-pressure boilers, high-temperature pipelines, etc., with good strength and corrosion resistance.
Copper and copper alloys: Suitable for low temperature and non-corrosive occasions, such as refrigeration equipment, water supply and drainage systems, etc.

Plastics: Fit for low-pressure, lightweight applications like gas pipes, residential water supply and drainage systems, etc.
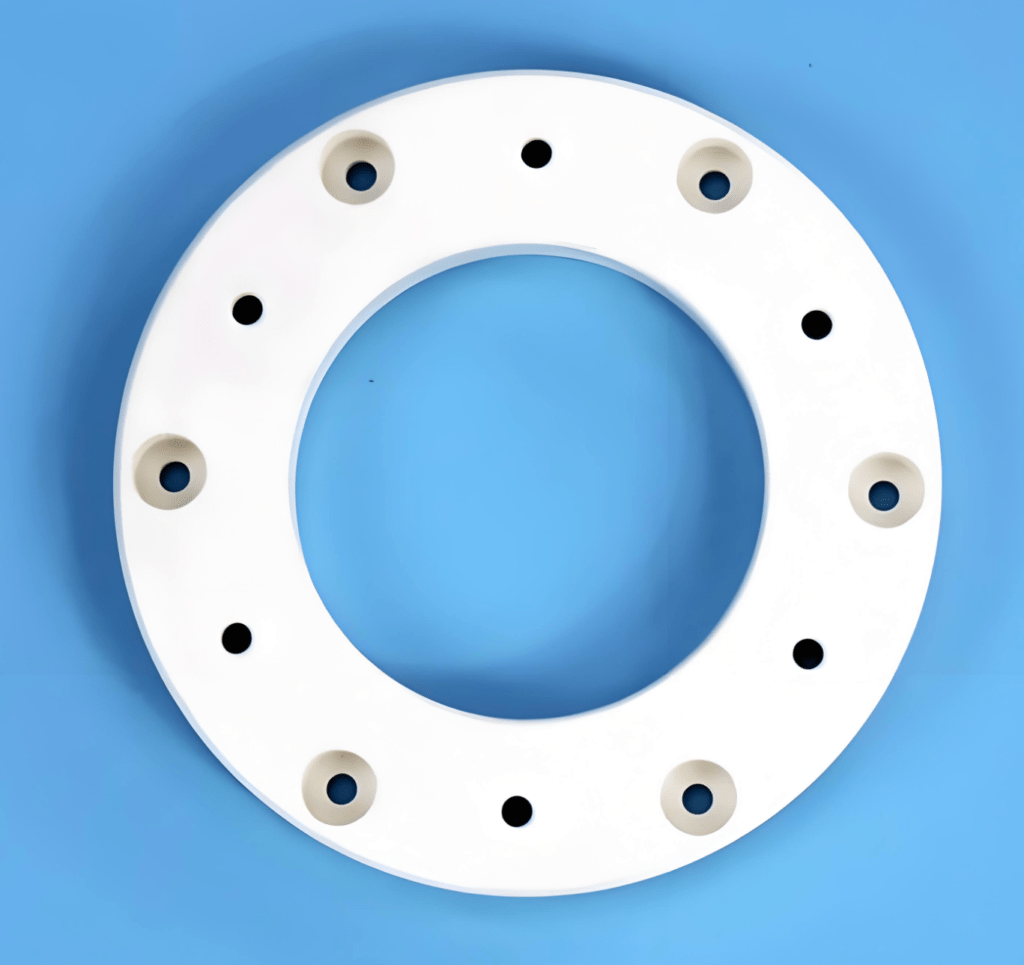
Ceramics flanges: Applicable in non-corrosive, high temperature environments, including industrial furnaces and aircraft.

Aluminum alloy flanges: Flanges made of aluminum alloy are typically utilized in unique applications, such industrial or aeronautical machinery with particular needs.

Nickel alloy flanges: Nickel alloy flanges provide exceptional corrosion resistance and high temperature performance, making them ideal for a variety of unique working environments with demanding material performance requirements, including the chemical, petroleum, and nuclear industries.
To make sure that the flange will function and be reliable enough to satisfy the needs of the application, you still need to carefully evaluate a number of aspects when selecting the materials for the flange, including operating circumstances, media properties, temperature and pressure requirements, corrosion resistance, and cost.
Please feel free to contact us for corrosion-resistant flanges
YYANHAO has extensive experience, particularly in precision machining of carbon steel and stainless steel flanges. The company’s manufacturing process is meticulously detailed, employs cutting-edge technology, and is well-versed in the specific needs of many industrial applications.
YANHAO’s flanges meet or surpass the following criteria and benchmarks:
ASTM Standards:
- Compliance verification: Ensure that the stainless steel flange fulfills the American Society for Testing and Materials’ (ASTM) requirements.
- Quality assurance: ASTM standards serve as the baseline for material quality and performance. Ensuring compliance guarantees that the flange is reliable and durable in a variety of applications.
ASME Certification:
- Adhere to tight standards: Make sure the stainless steel flange fulfills the American Society of Mechanical Engineers (ASME) specifications.
- A Comprehensive Approach: ASME certification encompasses all elements of design, manufacture, and testing. This rigorous certification assures that flanges adhere to the highest industry requirements.
We offer ASME flanges in a variety of sizes and specifications>>
ISO Certification:
- Global Quality Standards: Look for ISO-certified stainless steel flanges.
- Performance Guarantee: ISO accreditation confirms adherence to globally accepted quality and performance standards, indicating a commitment to supplying products that consistently fulfill consumer expectations.
YANHAO’s commitment to quality, durability, and innovation is more than just a slogan, it is the cornerstone of the company’s identity. Every stainless steel flange is embedded with expertise and reflects a dedication to carefully crafted products that not only meet the needs of today’s industry, but also anticipate and adapt to tomorrow’s challenges. By choosing YANHAO, the industry is not just getting a flange, they are investing in a tradition of excellence that defines the essence of the company.
Author: Lewis Liu
Hello, my name is Lewis Liu, and I’m a professional sales engineer with over a decade of expertise in the flange fittings sector.
I am quite informed about flange selection, installation, and maintenance. I am passionate about providing customers with the greatest solutions for keeping their pipeline systems running smoothly, safely, and dependably.
If you have any queries or concerns concerning flange fittings for your pipelines, whether they are about selection, material choice, specification requirements, or anything else, please contact me at any time. I am dedicated to providing expert advice and assistance to help you make educated decisions and reach your objectives.
