How a Flange Is Made: The Flange Production/Manufacturing Process
The manufacturing process of flanges can be roughly divided into 10 steps. At YANHAO, we also produce according to these steps. In the actual production process, we will also change or upgrade some processes according to user needs. In this article, we will introduce these 10 steps in detail, including both forged flanges and cast flanges.
10 Steps of Flange Production
1. Raw material

The journey of creating forged flanges begins with the careful preparation of raw materials. This step is crucial, as it includes a thorough examination of the materials’ appearance, mechanical properties, and chemical composition.
Whether it is stainless steel, carbon steel, or alloy steel, ensuring these materials meet production standards is essential for a successful manufacturing process.
Material traceability holds significant importance as well. By carefully managing furnace numbers and batches, we can guarantee the quality and consistency of every batch of materials. It is all about precision and attention to detail!
At YANHAO, we only use raw materials from well-known steel mills in China.
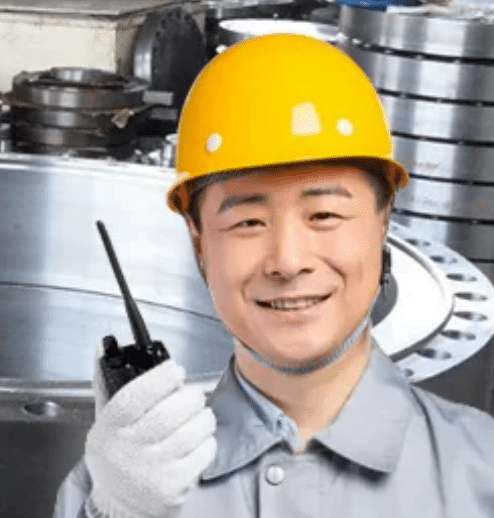
Our customers will pay attention to whether the raw materials used in flanges meet relevant quality standards, including chemical composition, physical properties, and surface quality. The quality of raw materials directly affects the performance and reliability of the final product.
2. Sawing & cutting
During the stage of sawing and cutting material, precision in geometric dimensions is crucial. Plus, we’re keen on minimizing material waste and boosting production efficiency by fine-tuning those cutting parameters. This is truly revolutionary! Getting this step right is crucial for maintaining the dimensional accuracy of the flange.
For flange cutting, YANHAO typically uses the following two kinds of equipment:
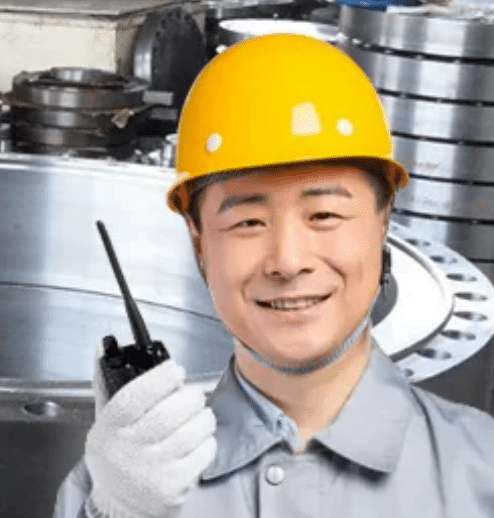
The dimensional accuracy of the flange is also a matter of great concern to our customers because it is related to whether the flange can be installed correctly and ensure the sealing. Excessive dimensional error may cause connection problems or leakage.
3. Heating
The heating process is an important link before forging. By accurately controlling the heating temperature and time, the deformation force during forging can be reduced, the plasticity of the metal can be improved, and problems such as oxidation and decarburization can be avoided.
4. Forging
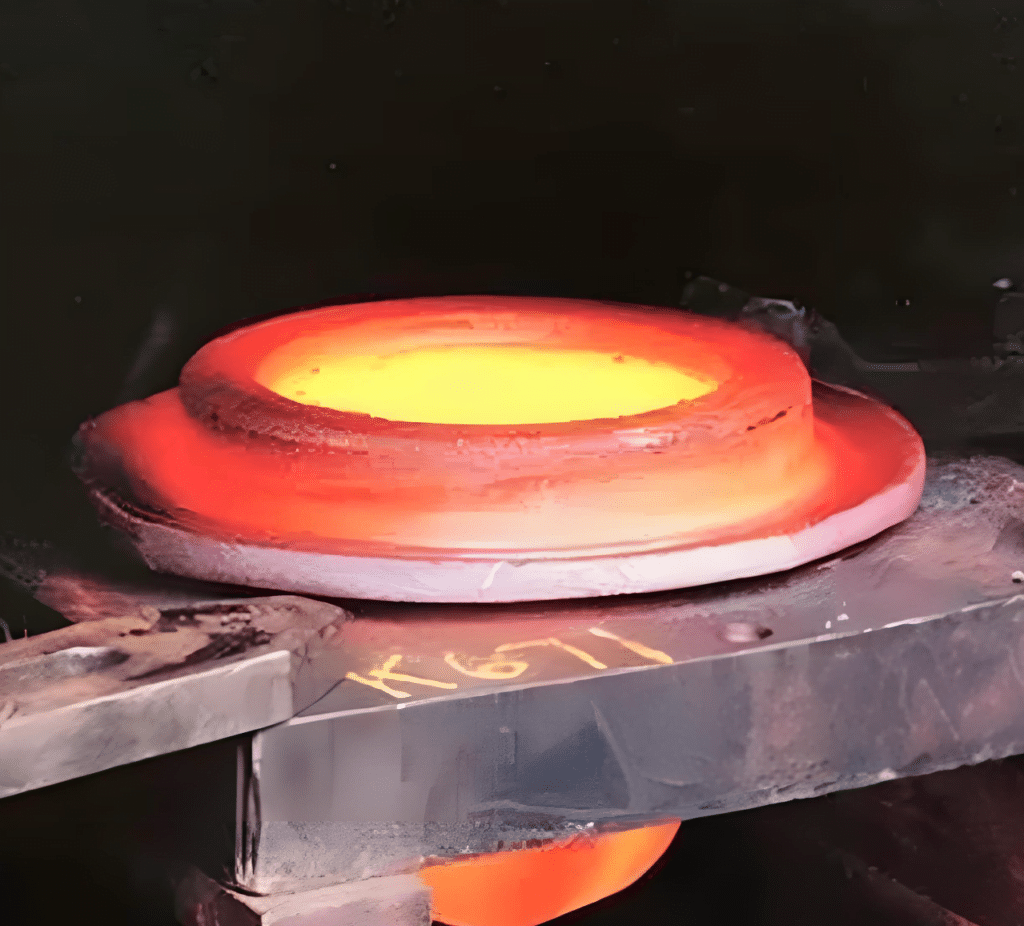
During the forging process, the microstructure and mechanical properties of the flange can be optimized by controlling the forging ratio, speed, and pressure.
Flange forging personnel’s abilities and expertise are critical to ensuring forging quality. Forging personnel must understand the properties of various materials, such as carbon steel, stainless steel, alloy steel, and so on, as well as how they behave when heated and forged.
At YANHAO, we have the most qualified engineers and laborers to execute this operation.
5. Heat treatment
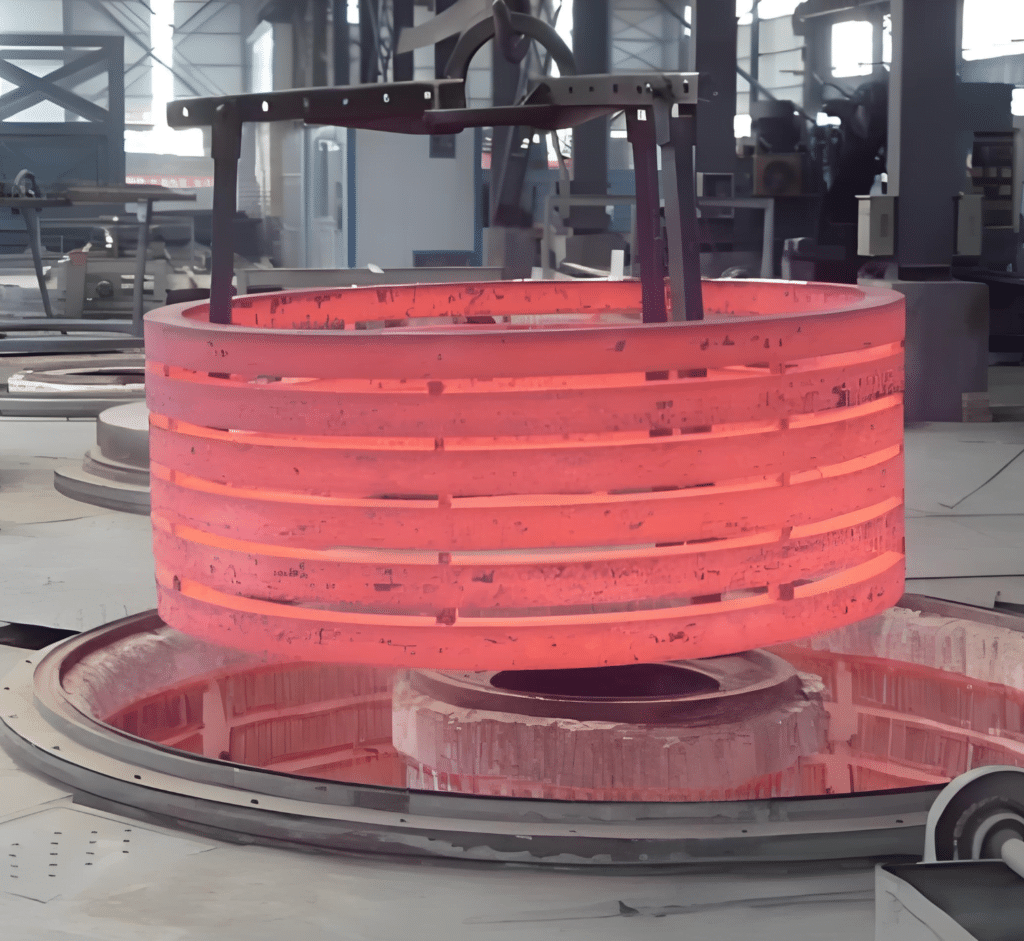
Heat treatment plays a crucial role in enhancing the performance of flanges. This involves various processes like annealing, normalizing, quenching, and tempering, all of which significantly influence the final performance of the flange.
During heat treatment, it is crucial to closely monitor temperature control, holding time, and cooling rate. Each of these factors must be managed with precision for optimal results.
6. Machining
During the machining stage, it is crucial to focus not only on dimensional control but also on ensuring the surface quality of the flange is top-notch.
By utilizing fine machining techniques, we can enhance the surface finish of the flange, which is crucial for its performance and longevity in real-world applications.
7. Non-destructive testing
Nondestructive testing plays a crucial role in guaranteeing the internal quality of flanges.
By utilizing technologies like ultrasonic testing, magnetic particle testing, and radiographic testing, we can uncover internal cracks, pores, and various defects, all to guarantee the reliability of the product.
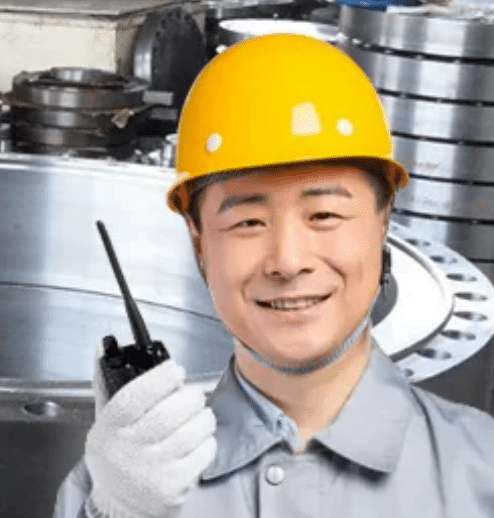
In order to ensure that there are no defects, such as cracks and pores inside the flange, our customers will pay attention to whether we have carried out strict non-destructive testing, such as ultrasonic testing, X-ray testing, etc. We provide detailed test reports (MTR) for each batch of flanges to ensure transparency and traceability.
8. Pickling and anti-corrosion
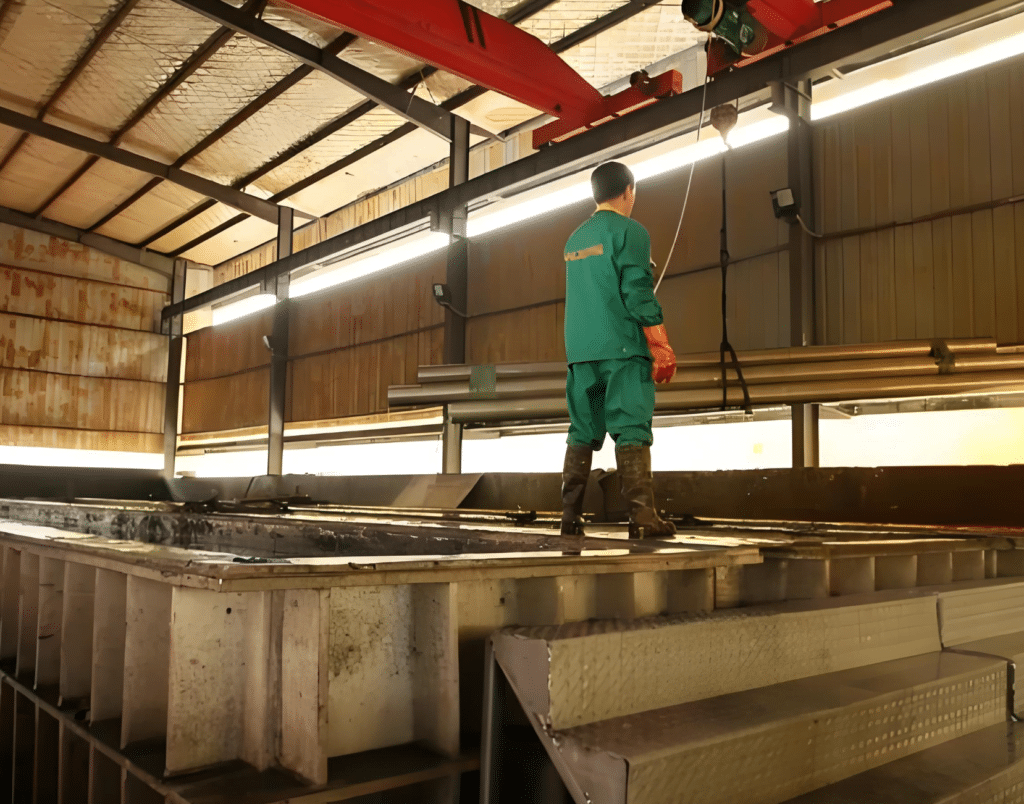
The final stages of flange manufacturing involve the crucial processes of pickling and anti-corrosion treatment.
To enhance the durability of the flange, a chemical treatment is employed to eliminate impurities. Following this, an anti-corrosion coating or electroplating is applied to boost its resistance to corrosion.
9. Quality evaluation
The acceptance of the finished product marks the ultimate quality assessment of the flange. This involves a thorough inspection that covers mechanical properties, dimensional accuracy, and surface quality. Getting this step right is crucial for making sure the flange aligns with both international and domestic standards.
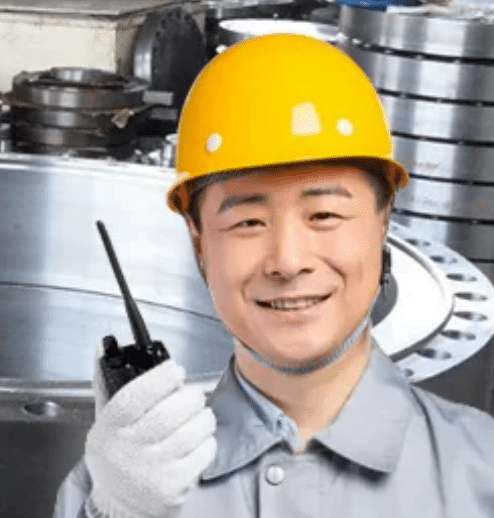
Customers want detailed production records, including raw material sources, production batches, heat treatment records, etc., to ensure product traceability. At YANHAO, we provide detailed product traceability records.
10. Steel stamping and storage
Steel stamping and warehousing management play a crucial role in documenting flange information and maintaining traceability.
By implementing a robust inventory management system, you can effortlessly monitor the production history and quality records of each flange, guaranteeing optimal quality control for the product.
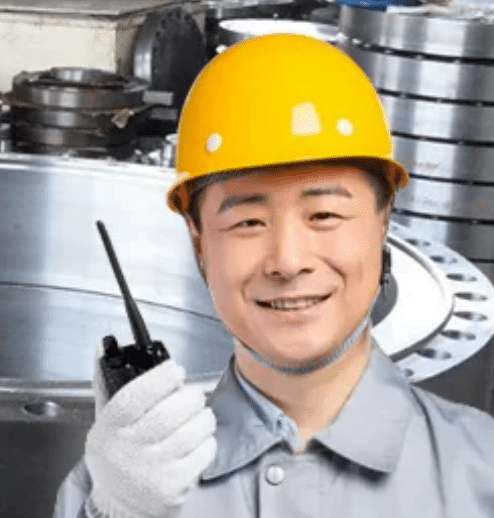
Print or mark the die serial number, material furnace number, and other information on the forgings, and these marks will accompany the products until they are finally delivered. In this way, even if there are problems during the use of the product, the original production information can be traced back.
Additional Information
Bolt Holes and Manufacturing Methods
The number and size of bolt holes in flanges can vary based on the specific application and industry standards. YANHAO offers a wide range of flange types, including weld neck flanges, slip-on flanges, blind flanges, lap joint flanges, socket weld flanges, and threaded flanges. Each type is manufactured using the most suitable manufacturing methods, whether it is forging or casting, to ensure optimal performance and reliability.
Flange Standards and Materials
At YANHAO, we adhere to various international and domestic standards, including ANSI, ASME, EN, and custom types. Our flanges are available in a variety of materials, such as stainless steel, carbon steel, and alloy steel, to meet the diverse needs of our customers.
Final Words
The above is the specific process of our flange production, YANHAO. We will adjust the details of the production process according to the needs of users. Below are some common flange products produced by YANHAO. You can click on the links to view the detailed information.
Category | Options |
---|---|
Flange Standards | ANSI flange | ASME flange | EN Standard Flange | Custom Type |
Flange Types | Weld Neck Flanges | Slip-On Flanges | Blind Flanges | Lap Joint Flanges | Socket Weld Flanges | Threaded Flanges |
Flange Materials | Stainless Steel Flanges | Carbon Steel Flanges | Alloy Steel Flanges |
Our customers are very satisfied with the quality of our products. Also, customers love YANHAO for our competitive prices and prompt delivery, ensuring their satisfaction every time.
Author: Lewis Liu
Hello, my name is Lewis Liu, and I’m a professional sales engineer with over a decade of expertise in the flange fittings sector.
I am quite informed about flange selection, installation, and maintenance. I am passionate about providing customers with the greatest solutions for keeping their pipeline systems running smoothly, safely, and dependably.
If you have any queries or concerns concerning flange fittings for your pipelines, whether they are about selection, material choice, specification requirements, or anything else, please contact me at any time. I am dedicated to providing expert advice and assistance to help you make educated decisions and reach your objectives.
