Choosing the Right Flange Type: A Comparison of ANSI B16.5, ANSI B16.47, ASME B16.5, and ASME B16.47
I. Introduction
Flanges are an essential component in piping systems that connect pipes, valves, and other equipment. Choosing the right flange type is crucial for ensuring the integrity, safety, and efficiency of a piping system. In this blog post, we will compare four common types of flanges: ANSI B16.5, ANSI B16.47, ASME B16.5, and ASME B16.47. We will discuss their definitions, features, advantages, and disadvantages, as well as their applications and industries where they are commonly used. By the end of this post, you will have a better understanding of the differences and similarities between these flange types and be able to make informed decisions when selecting the right flange type for your specific piping system. Let’s dive in!
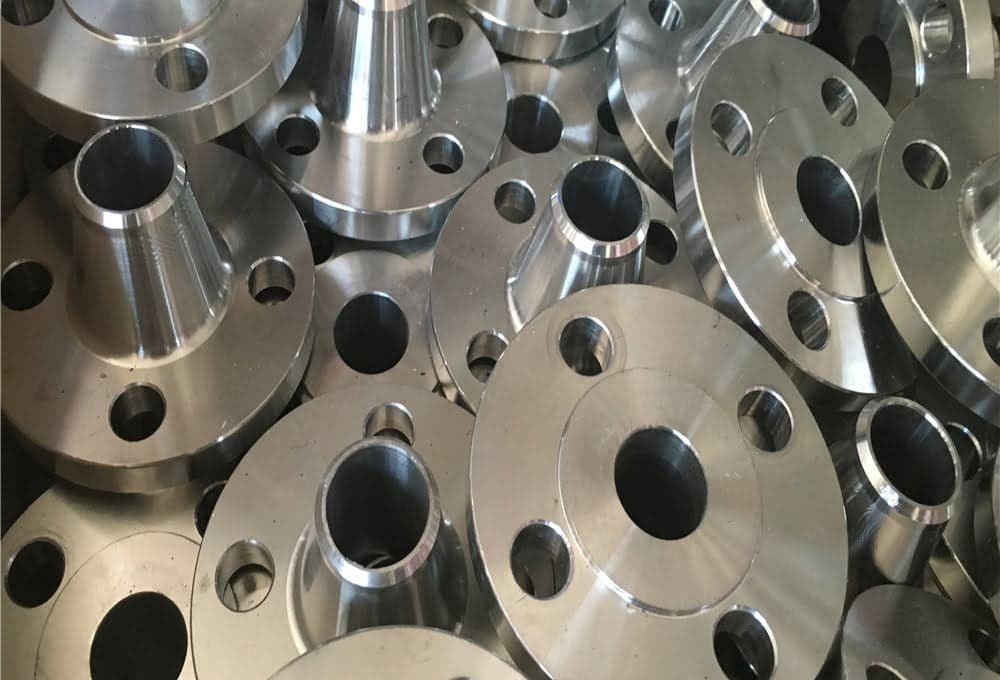
II. ANSI B16.5 Flange Type
A. Definition and features:
ANSI B16.5 flanges are standardized flange types that are designed to connect pipes, valves, and other equipment in a piping system. These flanges have a raised face with bolt holes that allow for easy alignment and connection with the corresponding flange on the adjacent equipment. They come in various sizes and pressure classes and are made of materials such as carbon steel, stainless steel, and alloy steel.
B. Advantages and disadvantages:
One advantage of ANSI B16.5 flanges is their availability and familiarity in the industry. They are widely used and recognized by manufacturers, suppliers, and engineers, which makes them easier to source and install. They also offer good pressure and temperature ratings, making them suitable for a wide range of applications.
One disadvantage of ANSI B16.5 flanges is their limited compatibility with certain materials and operating conditions. They may not be suitable for highly corrosive or abrasive environments or when high levels of vibration or stress are present. Additionally, their flat gasket design may be prone to leaks and require frequent maintenance.
C. Applications and industries where it is commonly used:
ANSI B16.5 flanges are commonly used in industries such as oil and gas, chemical, and petrochemical. They are suitable for connecting pipes and equipment that require high pressure and temperature ratings, such as pipelines, valves, pumps, and heat exchangers. They are also used in applications that require frequent disassembly and maintenance, such as in offshore drilling platforms and refineries.
III. ANSI B16.47 Flange Type
A. Definition and features:
ANSI B16.47 flanges, also known as large-diameter flanges, are designed for larger pipes and higher pressure ratings than ANSI B16.5 flanges. They come in two types: Series A and Series B. Series A flanges have smaller bolt holes and higher pressure ratings than Series B flanges. Both types have a raised face and can accommodate gaskets of various materials.
B. Advantages and disadvantages:
One advantage of ANSI B16.47 flanges is their ability to handle larger pipes and higher pressure ratings, which makes them suitable for demanding applications. They also offer a wider range of sizes and pressure classes than ANSI B16.5 flanges, providing greater flexibility in designing piping systems.
One disadvantage of ANSI B16.47 flanges is their higher cost and greater complexity in installation. They may require specialized tools and equipment to handle the larger size and weight of the flanges, as well as the higher torque required for tightening the bolts. Additionally, the larger size and weight of the flanges may require additional support and reinforcement of the piping system.
C. Applications and industries where it is commonly used:
ANSI B16.47 flanges are commonly used in industries such as power generation, chemical processing, and water treatment. They are suitable for connecting larger pipes and equipment that require high pressure and temperature ratings, such as boilers, turbines, and pumps. They are also used in applications that require frequent disassembly and maintenance, such as in power plants and refineries.
IV. ASME B16.5 Flange Type
A. Definition and features:
ASME B16.5 flanges, also known as ANSI/ASME B16.5 flanges, are a standard flange type developed by the American Society of Mechanical Engineers (ASME). They are similar to ANSI B16.5 flanges in terms of design and features, with a raised face and bolt holes for connection with adjacent equipment. They are available in various sizes and pressure classes and are made of materials such as carbon steel, stainless steel, and alloy steel.
B. Advantages and disadvantages:
One advantage of ASME B16.5 flanges is their compatibility with a wide range of materials and operating conditions. They are suitable for use in corrosive and abrasive environments and can handle high levels of stress and vibration. They also offer good pressure and temperature ratings, making them suitable for a wide range of applications.
One disadvantage of ASME B16.5 flanges is their limited availability and higher cost compared to ANSI B16.5 flanges. They may also require additional machining or surface finishing to ensure proper fit and alignment with adjacent equipment.
C. Applications and industries where it is commonly used:
ASME B16.5 flanges are commonly used in industries such as oil and gas, chemical, and petrochemical. They are suitable for connecting pipes and equipment that require high pressure and temperature ratings, such as pipelines, valves, pumps, and heat exchangers. They are also used in applications that require frequent disassembly and maintenance, such as in offshore drilling platforms and refineries.
V. ASME B16.47 Flange Type
A. Definition and features: ASME B16.47 flanges, also known as large-diameter steel flanges, are designed for use in high-pressure and high-temperature applications. They are available in two types: Series A and Series B and are similar to ANSI B16.47 flanges in terms of design and features. They have a raised face and bolt holes for connection with adjacent equipment and are available in various sizes and pressure classes. They are commonly made of materials such as carbon steel, stainless steel, and alloy steel.
B. Advantages and disadvantages: One advantage of ASME B16.47 flanges is their high pressure and temperature ratings, which make them suitable for use in demanding applications. They also offer a wide range of sizes and pressure classes, providing flexibility in designing piping systems.
One disadvantage of ASME B16.47 flanges is their higher cost and complexity in installation. They require specialized tools and equipment to handle the larger size and weight of the flanges, as well as the higher torque required for tightening the bolts. Additionally, the larger size and weight of the flanges may require additional support and reinforcement of the piping system.
C. Applications and industries where it is commonly used: ASME B16.47 flanges are commonly used in industries such as oil and gas, chemical, and petrochemical. They are suitable for connecting large-diameter pipes and equipment that require high pressure and temperature ratings, such as pipelines, valves, pumps, and heat exchangers. They are also used in applications that require frequent disassembly and maintenance, such as in offshore drilling platforms and refineries.
VI. Comparison of ANSI B16.5, ANSI B16.47, ASME B16.5, and ASME B16.47 Flange Types
A. Key differences and similarities:
- ANSI B16.5 and ASME B16.5 flanges have similar designs and features, with raised faces and bolt holes for connection with adjacent equipment. They are suitable for a wide range of materials and operating conditions and offer good pressure and temperature ratings.
- ANSI B16.47 and ASME B16.47 flanges are large-diameter steel flanges designed for high-pressure and high-temperature applications. They are available in two types: Series A and Series B and offer high pressure and temperature ratings.
- ANSI B16.5 and ASME B16.5 flanges have a smaller size range compared to ANSI B16.47 and ASME B16.47 flanges.
- ASME B16.47 flanges are more complex and expensive to install due to their larger size and weight, requiring specialized tools and equipment for handling and tightening.
B. Factors to consider when choosing a flange type:
- Operating conditions such as pressure, temperature, and media compatibility.
- Material selection for the flange and adjacent equipment.
- Piping systems design requirements, such as size, weight, and pressure class.
- Installation and maintenance considerations, such as ease of assembly and disassembly, accessibility, and cost.
C. Recommendations for different applications and industries:
- ANSI B16.5 and ASME B16.5 flanges are suitable for a wide range of applications and industries, including chemical, petrochemical, and oil and gas industries, as well as water and wastewater treatment facilities.
- ANSI B16.47 and ASME B16.47 flanges are commonly used in large-diameter piping systems, such as those found in power generation, offshore drilling, and petrochemical facilities.
- When choosing a flange type, it is important to consider the specific requirements of the application and industry, as well as the available resources for installation and maintenance. Consulting with a flange supplier or engineer may also be helpful in selecting the appropriate flange type.
VII. Conclusion
In this blog post, we have compared and contrasted four types of flanges: ANSI B16.5, ANSI B16.47, ASME B16.5, and ASME B16.47. We have discussed the definition, features, advantages, and disadvantages of each flange type, as well as their common applications and industries. We have also identified key factors to consider when choosing a flange type, such as operating conditions, material selection, piping system design, installation, and maintenance.
When choosing a flange type, it is important to consider the specific requirements of the application and industry, as well as the available resources for installation and maintenance. Consulting with a flange supplier or engineer may also be helpful in selecting the appropriate flange type.
The demand for high-performance flanges that can withstand extreme operating conditions and reduce emissions is driving innovation in flange technology. Future developments may include the use of new materials, such as composites and alloys, and the integration of smart technologies, such as sensors and monitoring systems. There may also be a trend towards modular and customizable flange designs that can be adapted to different applications and industries.
Author: Lewis Liu
Hello, my name is Lewis Liu, and I’m a professional sales engineer with over a decade of expertise in the flange fittings sector.
I am quite informed about flange selection, installation, and maintenance. I am passionate about providing customers with the greatest solutions for keeping their pipeline systems running smoothly, safely, and dependably.
If you have any queries or concerns concerning flange fittings for your pipelines, whether they are about selection, material choice, specification requirements, or anything else, please contact me at any time. I am dedicated to providing expert advice and assistance to help you make educated decisions and reach your objectives.
