How to know if you have the right flange size?
I. Introduction
As an engineer or a professional working in the field of piping systems, selecting the right flange size is crucial for ensuring the smooth operation of the system. Flanges serve as critical components that connect pipes, valves, and other equipment, and their size selection directly impacts the performance and functionality of the system. Therefore, accurately determining the flange size is essential during the design, installation, or maintenance of piping systems, as it ensures the integrity, reliability, and efficiency of the system. This article aims to discuss the importance of choosing the correct flange size for piping systems and explore various factors and techniques that influence flange size selection. By understanding the significance of flange size and the methods for proper selection, we can better design, install, and maintain piping systems, avoiding potential issues and losses while improving system performance and reliability. Whether you are new to the field of piping systems or an experienced professional, this article provides comprehensive guidance on flange size selection, helping you successfully tackle the challenges of pipe connections in your work.

II. Understanding Flange Size
A. Definition of flange size:
Flange size refers to the dimensions and specifications of a flange, which is a device used to connect pipes, valves, and other equipment in a piping system. It typically consists of a flat disk or ring with evenly spaced bolt holes for secure attachment to other components. Flanges come in various sizes, ranging from small diameters for residential applications to large diameters for industrial or commercial use. The flange size is determined by factors such as pipe size, material, pressure rating, and application requirements.
B. Importance of matching flange size to pipe size:
Matching the flange size to the pipe size is crucial for achieving a proper fit and ensuring the integrity and functionality of the piping system. A correctly sized flange provides a secure connection that minimizes the risk of leaks, joint failures, and structural issues. It also facilitates efficient flow within the system, reducing pressure drop and maintaining optimal performance. Using a flange size larger or smaller than the pipe size can lead to complications, such as excessive stress concentration, poor sealing, restricted flow, and potential system failures. Therefore, it is essential to select a flange size that matches the pipe size accurately.
C. Factors to consider when determining flange size:
Several factors should be considered when determining the appropriate flange size for a piping system:
- Pipe size: The diameter and wall thickness of the pipe plays a key role in determining the flange size. It is essential to match the flange size with the pipe size to ensure a proper fit and effective sealing.
- Pressure rating: The operating pressure of the system influences the selection of the flange size. Flanges must be able to withstand the pressure and not compromise the integrity of the system.
- Material compatibility: The material of the pipe, valves, and other components should be compatible with the flange material to avoid any chemical or galvanic reactions that could degrade the system. This consideration affects the selection of the appropriate flange material and size.
- Application requirements: The specific application requirements, such as temperature, fluid type, and environmental conditions, should be considered when determining the flange size. These factors can impact the strength, durability, and material choice of the flange.
- Standards and regulations: Compliance with industry standards and regulations is essential for ensuring the reliability and safety of the piping system. Flange size selection should meet the specified standards and criteria set by relevant organizations.
By considering these factors, engineers and professionals can determine the appropriate flange size that matches the pipe size accurately, ensuring a secure and efficient connection in the piping system.

III. Steps to Identify the Right Flange Size
A. Identify the piping system requirements
To identify the piping system requirements, you need to consider the following factors:
- Material: Determine the material of the pipe, valves, and other components in the piping system. Different materials have varying properties such as corrosion resistance, chemical compatibility, and mechanical strength. Selecting the appropriate flange material is important to ensure compatibility with the system’s components.
- Pressure rating: Determine the maximum operating pressure of the piping system. This information is crucial in selecting a flange that can withstand the required pressure without leaking or failing. Consider the pressure rating of the flange and ensure it is suitable for the system’s pressure requirements.
- Temperature range: Identify the temperature range that the piping system will be exposed to during operation. This temperature range affects the selection of flange material, as some materials may deform or lose strength at high temperatures. Consider the thermal expansion and contraction of the piping system when selecting the flange to ensure proper sealing and functionality.
By understanding the material, pressure rating, and temperature range requirements of the piping system, you can make informed decisions when selecting the right flange size and material. This helps ensure the safe and efficient operation of the piping system.
B. Measure the pipe dimensions
To measure the pipe dimensions, follow these steps:
- Outside diameter (OD) measurement: Use a caliper or measuring tape to measure the outside diameter of the pipe. Make sure to measure at the widest point of the pipe. The outside diameter is important for selecting the correct flange size that matches the pipe.
- Consider wall thickness and pipe schedule: Take note of the wall thickness of the pipe. You can usually find this information printed on the pipe itself or refer to pipe specifications. Pipe schedules, such as Schedule 40 or Schedule 80, indicate the wall thickness and are used to standardize pipe sizes.
Consider the combination of the outside diameter and wall thickness to determine the correct pipe size. For example, a pipe with an outside diameter of 2 inches and a wall thickness of 0.25 inches would be referred to as a 2-inch Schedule 40 pipe.
By accurately measuring the pipe dimensions and considering the wall thickness and pipe schedule, you can select the appropriate flange size that matches the pipe and ensures a proper fit for the piping system.
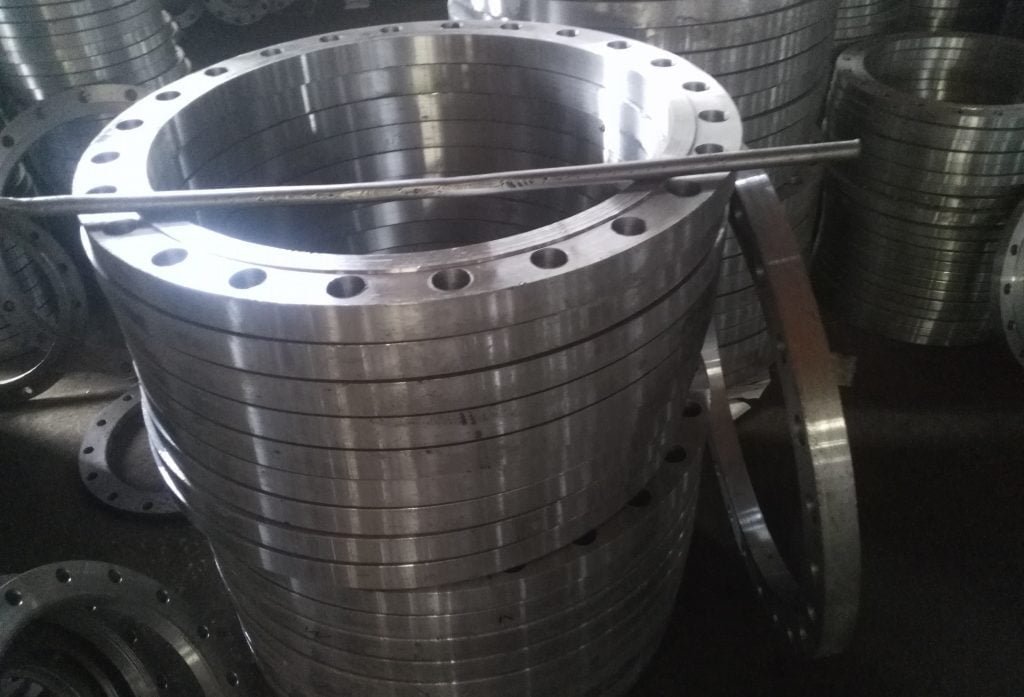
C. Determine the flange type and connection method
To determine the flange type and connection method for your piping system, consider the following:
- Overview of common flange types:
- Weld Neck Flange: This flange type has a long tapered neck and is designed to be butt-welded to the pipe. It provides high strength and is suitable for high-pressure and high-temperature applications.
- Slip-On Flange: This flange type slides over the pipe and is then welded in place. It is easy to install and suitable for low-pressure applications.
- Socket Weld Flange: This flange type has a socket or recess that fits over the pipe end. It is then welded on the outer side of the flange and pipe. It is commonly used in smaller pipe sizes and high-pressure applications.
- Threaded Flange: This flange type has internal threads that allow it to be screwed onto the pipe. It is suitable for low-pressure applications and is commonly used for small pipe sizes or in plumbing systems.
Consider the specific requirements of your piping system, such as pressure, temperature, and installation convenience, when selecting the appropriate flange type.
- Consideration of connection method:
- Butt-weld: In this method, the flange is welded directly to the pipe end, providing a strong and leak-resistant connection. It is commonly used for high-pressure and high-temperature applications.
- Socket Weld: This method involves inserting the pipe into the socket of the flange and then welding on the outer side. It provides good structural integrity and is commonly used for small pipe sizes and high-pressure applications.
- Threaded: This method involves screwing the flange onto a threaded pipe end. It is suitable for low-pressure applications and allows for easier disassembly and reassembly.
Consider the compatibility of the connection method with your piping system and the requirements for disassembly and maintenance when selecting the appropriate flange connection method.
By considering the specific requirements of your piping system and the available flange types and connection methods, you can choose the most suitable flange type and connection method for your application.
D. Consult industry standards and specifications
When determining flange dimensions and specifications, it is important to consult and adhere to industry standards and specifications. Some of the commonly referenced standards for flanges include:
- ASME B16.5: The American Society of Mechanical Engineers (ASME) standard provides dimensions, pressure ratings, and materials for pipe flanges and flanged fittings. It covers flanges from 1/2″ to 24″ in size and includes various types of flanges such as weld neck, slip-on, socket weld, and blind flanges.
- EN 1092-1: The European standard for flanges, gaskets, and bolting is specified for use in pressure vessel and piping applications. It provides dimensions, pressure ratings, and material specifications for a range of flange types.
Other relevant standards to consider include ANSI/ASME B16.47, API 605, and DIN standards for flange dimensions and specifications.
These standards outline important details such as flange dimensions, flange face types (e.g., raised face, flat face), bolting requirements, pressure ratings, and applicable materials. They provide guidelines for flange design, manufacturing, and installation to ensure compatibility and functionality within the piping system.
By consulting and adhering to industry standards and specifications, you can ensure that the flanges used in your piping system meet recognized criteria, promoting safety, reliability, and compliance with regulations.
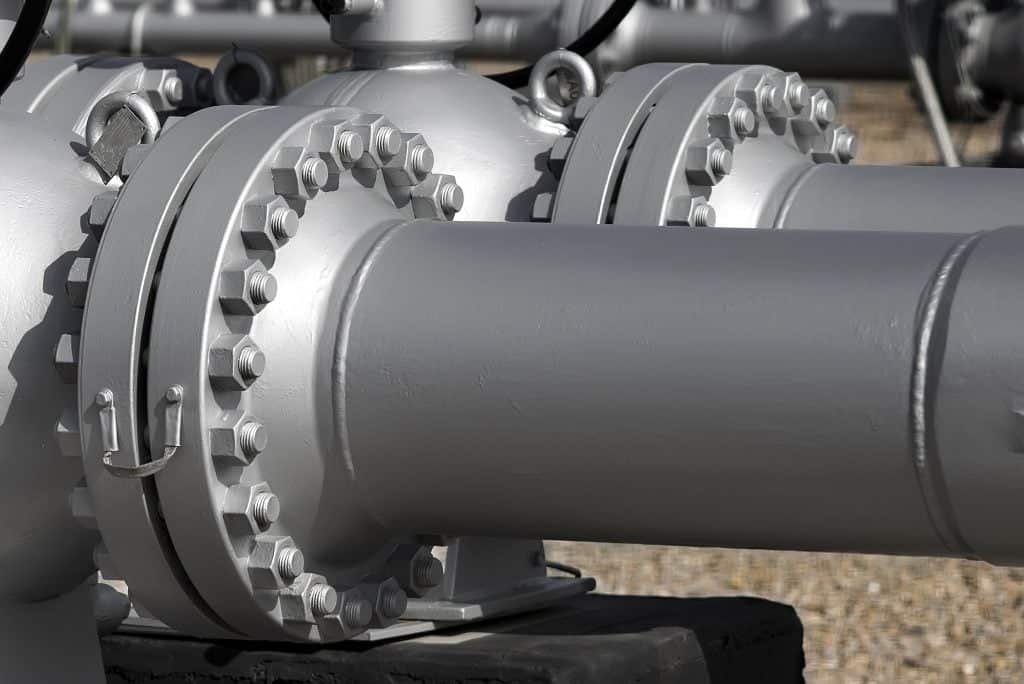
E. Matching flange dimensions with pipe size
To match flange dimensions with the pipe size, follow these steps:
- Comparing pipe OD measurement with standard flange dimensions: Compare the outside diameter (OD) measurement of the pipe with the standard flange dimensions specified in industry standards such as ASME B16.5 or EN 1092-1. These standards provide comprehensive information on flange dimensions for different pipe sizes.
- For example, if the measured OD of the pipe is 4 inches, consult the appropriate standard to determine the corresponding flange dimensions for a 4-inch pipe.
Consider the specific flange type (e.g., weld neck, slip-on) and flange rating (e.g., Class 150, PN16) to ensure compatibility with the pipe and the intended application.
- Ensuring accurate alignment of flange size with pipe size: Ensure that the flange size you choose matches the designated pipe size accurately. This requires careful attention to the dimensions and specifications outlined in the industry standards.
Consider factors such as flange face type (raised face, flat face), bolting requirements, and pressure ratings to ensure proper alignment between the flange size and the pipe size. Improper alignment can result in leaks, structural integrity issues, and potential safety hazards.
Also, ensure that the flange dimensions and type are appropriate for the specific requirements of your piping system, considering factors such as pressure, temperature, and fluid compatibility.
By comparing the pipe OD measurement with standard flange dimensions and ensuring accurate alignment of flange size with pipe size, you can select the appropriate flange that matches your piping system, ensuring a proper connection and maintaining system integrity.

F. Seek professional assistance when unsure
When unsure about matching flange dimensions with pipe size or any other aspect of flange selection, it is advisable to seek professional assistance. Here are two ways to obtain expert guidance:
- Consulting with professionals or experienced flange suppliers: Reach out to professionals in the industry, such as piping engineers or experienced flange suppliers, who have knowledge and expertise in flange selection. They can provide valuable insights, recommendations, and guidance based on their experience working with flanges in various applications.
These professionals can help in accurately determining the appropriate flange size based on the specific pipe size, pressure ratings, temperature requirements, and other factors relevant to your piping system. They can also guide you through the selection process, considering industry standards, specifications, and material compatibility.
- Getting expert guidance to determine the correct flange size: Some situations may require specialized knowledge or expertise to determine the correct flange size accurately. In such cases, consider seeking technical assistance from consultants, engineers, or flange manufacturers.
These experts can assess your specific requirements, review technical data, and perform calculations or analysis to ensure the correct flange size selection. They may utilize software tools and simulations to validate flange sizing, considering factors such as stress analysis, gasket compatibility, and alignment with the pipe size.
Seeking professional assistance reduces the risk of errors in flange selection and ensures that you have access to expert knowledge to make informed decisions. Their expertise can help avoid issues such as leaks, flange failures, or compatibility problems within your piping system.
Remember that accurate flange sizing is essential for the integrity and functionality of your piping system, so it is advisable to consult professionals when there is uncertainty.

IV. Conclusion
Choosing the correct flange size is crucial for the optimal performance and safety of a piping system. Following the proper steps to determine the correct flange size is important. This includes comparing pipe OD measurements with standard flange dimensions and ensuring accurate alignment of flange size with pipe size.
However, when faced with uncertainty, seeking professional assistance is a wise choice. Professionals such as sales engineers or experienced flange suppliers can provide valuable guidance and recommendations based on their expertise. They can help in selecting the correct flange size based on your specific requirements.
At Yanhao Company, we are more than willing to provide professional assistance, and we have experienced sales engineers who can offer you free guidance. By seeking their expertise and experience, you can ensure the accurate selection of flange size, minimizing the risks of leaks, flange failures, or compatibility issues.
Please do not hesitate to reach out to our sales engineers for assistance whenever needed. We will strive to provide you with the best support and guidance.
Author: Lewis Liu
Hello, my name is Lewis Liu, and I’m a professional sales engineer with over a decade of expertise in the flange fittings sector.
I am quite informed about flange selection, installation, and maintenance. I am passionate about providing customers with the greatest solutions for keeping their pipeline systems running smoothly, safely, and dependably.
If you have any queries or concerns concerning flange fittings for your pipelines, whether they are about selection, material choice, specification requirements, or anything else, please contact me at any time. I am dedicated to providing expert advice and assistance to help you make educated decisions and reach your objectives.
