How to Properly Install and Maintain Your Pipe Flanges?
When it comes to installing and maintaining pipe flanges, many people may overlook this important step. However, pipe flanges are a critical component of a piping system, ensuring the stability and integrity of the system while also improving its efficiency and reliability. Therefore, it is essential to understand how to properly install and maintain pipe flanges. This blog will provide you with a detailed guide, covering the overview of pipe flanges, installation steps, maintenance and care, application considerations, safety, and future development. We hope this guide will help you better understand pipe flanges and make your piping system more stable and reliable.
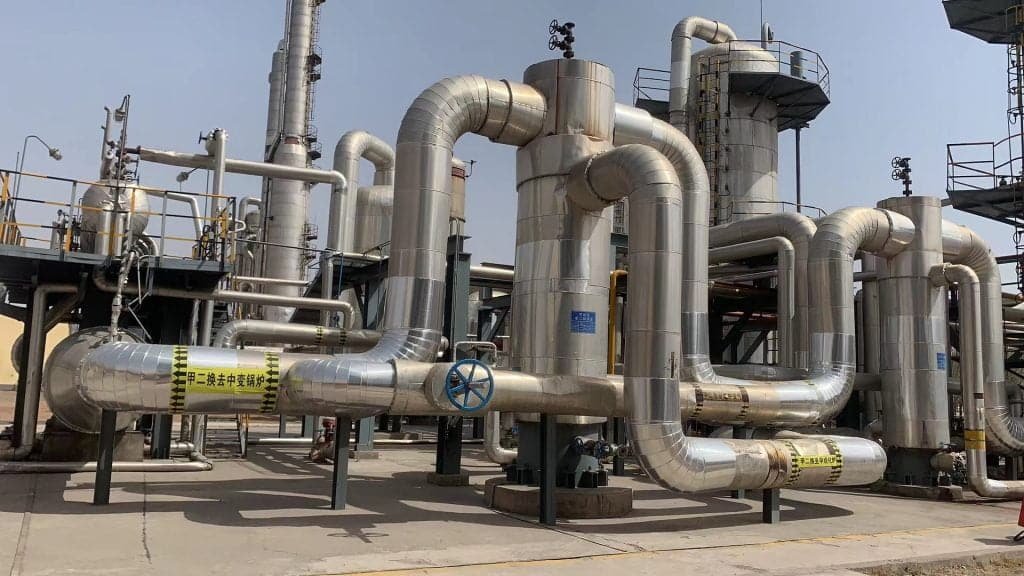

I. Overview of Pipe Flanges
A、What are pipe flanges?
Pipe flanges are mechanical devices that are used to connect two pipes or other components in a piping system. They provide a secure, leak-proof connection between two pipes or other components while allowing for easy disassembly and maintenance. A pipe flange consists of two separate pieces, each with a raised surface that is bolted together, forming a seal between the two pipes or components. They come in a variety of types and sizes, including weld neck, slip-on, threaded, and lap joint, and are typically made from materials such as carbon steel, stainless steel, or plastic. Pipe flanges are an essential part of many industrial and commercial piping systems, and are used in applications ranging from plumbing and heating systems to chemical processing plants and oil refineries.
B、Types and uses of pipe flanges
Pipe flanges come in various types and sizes, each with unique features and applications. Some common types of pipe flanges include weld neck, slip-on, threaded, lap joint, blind, and orifice flanges. Weld neck flanges are often used in high-pressure or high-temperature applications, slip-on flanges are used in low-pressure systems, threaded flanges are used in applications requiring easy disassembly, lap joint flanges are used in low-pressure applications requiring easy disassembly, blind flanges are used to seal off the end of a piping system, and orifice flanges are used to measure fluid flow rate. The type of flange used is determined by the specific requirements of the piping system, such as pressure, temperature, and fluid type.
C、Components of pipe flanges
Pipe flanges consist of several components, including the flange itself, bolts, nuts, and gaskets. The flange is the main component, providing a connection point for the two pipes or other components in the system. Bolts and nuts are used to secure the flange to the pipes, ensuring a tight and secure connection. Gaskets are placed between the flange faces to create a seal and prevent leakage. The type and material of these components are chosen based on the specific application and requirements of the piping system. Proper selection and installation of each component are critical to the overall performance and safety of the piping system.
II. Steps for Installing Pipe Flanges
A、Preparing for installation
Before installing pipe flanges, several preparation steps need to be taken:
Check the dimensions and materials of the flange and pipe to ensure they match the specifications and standards.
Clean the connecting surfaces of the flange and pipe to ensure they are free of oil, grease, rust, or any other substances. Steel brushes and solvents can be used to clean surfaces.
Check the connection surfaces of the flange and pipe to ensure they are flat. If the surfaces are uneven, they may need to be machined or ground to ensure a tight seal between the flanges.
Check that the bolts and nuts for the flange and pipe connection match and meet the specified requirements for quality, length, and type.
Choose an appropriate gasket. Select a gasket that meets the requirements of the pipe material, temperature, and pressure to ensure a proper seal.
Check that the pressure of the piping system is within the level and specifications required for the flange. If the pressure is too high or too low, the piping system may need to be replaced or reinforced.
Ensure that the construction site is safe. Before installing the flanges, evaluate the site and take necessary safety measures, such as wearing safety helmets and gloves, ensuring the use of appropriate tools, etc.
B、Installing the flanges
To install pipe flanges, follow these steps:
Align the two pipes to be connected and place the flange over the pipe ends.
Insert bolts through the holes in the flange and align them with the corresponding holes in the pipe.
Tighten the nuts on the bolts by hand until they are snug.
Use a torque wrench to tighten the bolts gradually and evenly in a crisscross pattern to ensure an even distribution of pressure and prevent warping or distortion of the flange.
After tightening the bolts, check the alignment of the flange and pipes to ensure they are properly aligned and straight.
Install the gasket between the flange faces creating a seal.
Tighten the nuts further to achieve the recommended torque value for the flange and gasket combination.
Inspect the flange and piping system for leaks, and adjust the bolts and gasket as needed to ensure a proper seal.
After the installation is complete, test the system for pressure and temperature to ensure it is functioning properly.
Proper installation of pipe flanges is critical to ensure the integrity and safety of the piping system, and it is important to follow the manufacturer’s instructions and industry standards.
C、Testing and verifying the pipeline
After installing pipe flanges, it is important to test and verify the pipeline to ensure that it is functioning properly and meets the necessary safety standards. Here are some steps that can be taken:
Perform a visual inspection of the entire pipeline system to check for any obvious leaks or damages.
Use non-destructive testing methods such as ultrasonic testing, magnetic particle testing, or radiography to detect any hidden defects or cracks in the piping system.
Test the pipeline system for pressure and temperature to ensure it can withstand operating conditions. Pressure testing involves pressurizing the pipeline to a level higher than the maximum operating pressure and checking for any leaks or drops in pressure over time. Temperature testing involves exposing the pipeline to the expected operating temperature and checking for any thermal expansion or contraction.
Verify that the pipeline system meets the required safety standards and regulatory requirements, such as ASME B31.1, ASME B31.3, or other relevant codes.
Record and document the test results and inspections to maintain a record of the pipeline system’s condition and compliance with safety standards.
Regular testing and verification of the pipeline system can help identify potential issues early and prevent costly repairs or accidents in the future. It is important to follow industry standards and manufacturer’s instructions when conducting tests and inspections.
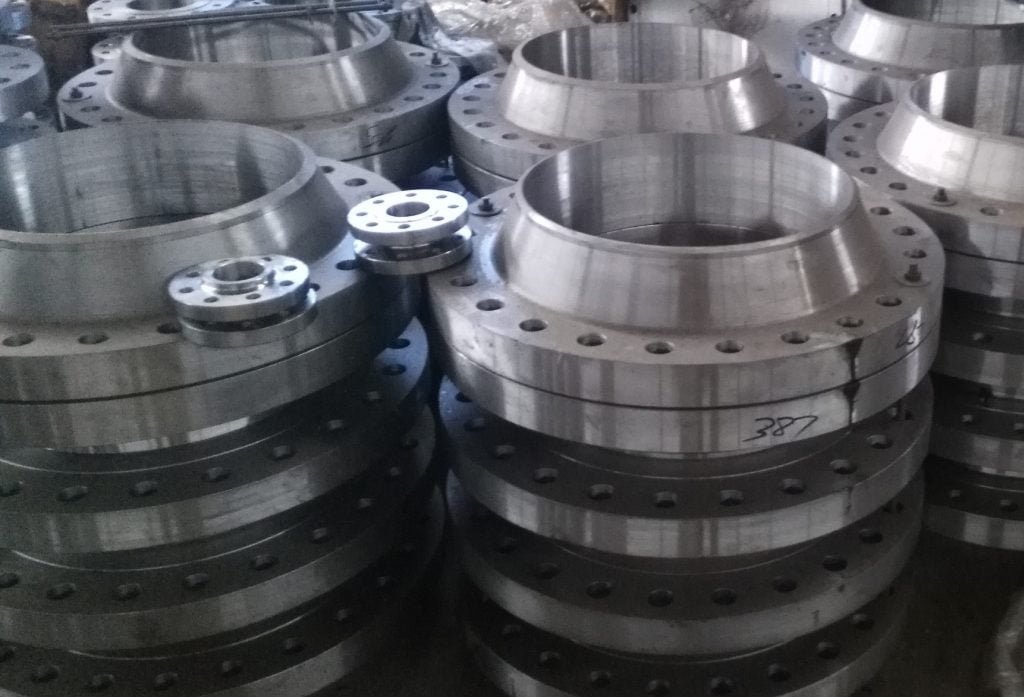


III. Maintenance and Care of Pipe Flanges
A、egularly checking the condition of pipe flanges
Regularly checking the condition of pipe flanges is crucial to ensure the safety and reliability of the piping system. Here are some steps that can be taken to check the condition of pipe flanges:
Inspect the flange surfaces for any signs of damage, such as cracks, erosion, corrosion, or deformations.
Check the bolts and nuts for any signs of wear or corrosion, and ensure they are tightened to the specified torque value.
Inspect the gasket for any signs of damage or wear, and replace it if necessary.
Check the alignment of the flange and piping system to ensure they are properly aligned and straight.
Perform a hydrostatic pressure test on the piping system to check for leaks and ensure the flanges are functioning properly.
Conduct regular maintenance, such as lubricating the bolts and nuts, and replacing any worn or damaged components.
Follow the manufacturer’s instructions and industry standards when conducting inspections and maintenance.
Regularly checking the condition of pipe flanges can help identify potential issues early and prevent costly repairs or accidents in the future. It is important to schedule regular inspections and maintenance to ensure the safe and reliable operation of the piping system.
B、Cleaning methods for pipe flanges
Proper cleaning of pipe flanges is essential for ensuring a secure and leak-free connection. Here are some common methods for cleaning pipe flanges:
Solvent cleaning: This method involves using a solvent, such as acetone or isopropyl alcohol, to clean the flange surface. The solvent dissolves any oil, grease, or other contaminants on the surface of the flange. It is important to use appropriate personal protective equipment (PPE) and follow safety guidelines when using solvents.
Abrasive cleaning: Abrasive cleaning involves using a wire brush or abrasive pad to clean the flange surface. This method is useful for removing rust, scale, and other stubborn contaminants from the surface of the flange.
Steam cleaning: Steam cleaning involves using high-pressure steam to clean the flange surface. This method is effective for removing dirt, grime, and other contaminants from the surface of the flange.
Ultrasonic cleaning: Ultrasonic cleaning involves immersing the flange in a cleaning solution and using ultrasonic waves to remove contaminants from the surface of the flange. This method is useful for cleaning complex geometries and hard-to-reach areas.
Acid cleaning: Acid cleaning involves using an acid, such as hydrochloric acid or sulfuric acid, to clean the flange surface. This method is effective for removing scale and rust from the surface of the flange. It is important to use appropriate PPE and follow safety guidelines when using acids.
It is important to choose the appropriate cleaning method based on the type of contaminants on the flange surface and the material of the flange. It is also important to follow safety guidelines and manufacturer’s instructions when conducting cleaning procedures.
C、Solutions to common problems with pipe flanges
Here are some common problems with pipe flanges and their solutions:
Leaks: Leaks can occur due to a variety of reasons, such as improper installation, insufficient tightening of bolts, or worn or damaged gaskets. To fix leaks, inspect the flange and tighten any loose bolts or replace worn or damaged gaskets.
Corrosion: Corrosion can occur due to exposure to moisture or corrosive chemicals. To prevent corrosion, use flanges made of materials resistant to corrosion, such as stainless steel or plastic. Regular maintenance, such as cleaning and painting, can also help prevent corrosion.
Flange deformation: Flange deformation can occur due to the over-tightening of bolts or thermal expansion and contraction. To prevent deformation, use the specified torque value for tightening bolts and use flanges made of materials that can withstand thermal expansion and contraction.
Improper alignment: Improper alignment can cause leaks and damage to the flange and piping system. To ensure proper alignment, use alignment tools and check the alignment periodically.
Flange damage: Flange damage can occur due to impact or other physical damage. To fix the flange damage, replace the damaged flange with a new one.
Bolt failure: Bolt failure can occur due to overtightening or under-tightening of bolts or the use of worn or damaged bolts. To prevent bolt failure, use the specified torque value for tightening bolts and replace worn or damaged bolts.
It is important to conduct regular inspections and maintenance of pipe flanges to identify and address any problems early on. Following industry standards and manufacturer’s instructions can also help prevent common problems with pipe flanges.



IV. Application Considerations for Pipe Flanges
A、Pressure and temperature limits
Proper use of pipe flanges requires consideration of pressure and temperature limits. Here are some important considerations related to pressure and temperature limits:
Pressure limits: Pipe flanges are rated for specific pressure limits. Exceeding the rated pressure limit can cause flange failure and result in leaks or other safety hazards. It is important to select flanges rated for the maximum pressure expected in the piping system and to follow the manufacturer’s instructions for installation and use.
Temperature limits: Pipe flanges are also rated for specific temperature limits. Exceeding the rated temperature limit can cause flange failure and result in leaks or other safety hazards. It is important to select flanges rated for the maximum temperature expected in the piping system and to follow the manufacturer’s instructions for installation and use.
Corrosion: High-pressure and high-temperature applications can increase the risk of corrosion in pipe flanges. It is important to select materials resistant to corrosion and to follow appropriate maintenance procedures to prevent corrosion.
Thermal expansion and contraction: Temperature changes can cause thermal expansion and contraction of the piping system, which can affect the performance of the flange. It is important to select flanges made of materials that can withstand thermal expansion and contraction and to use appropriate gaskets to accommodate thermal changes.
Pressure testing: Pressure testing is an important step in the installation and maintenance of pipe flanges. It is important to follow industry standards and manufacturer’s instructions for pressure testing and to conduct regular pressure testing to identify any potential issues.
Overall, proper selection, installation, and use of pipe flanges based on pressure and temperature limits are essential for ensuring a safe and efficient piping system.
B、How to use gaskets with flanges
When using pipe flanges, gaskets are an important component that can help ensure a leak-free seal. Here are some considerations when using gaskets with flanges:
Gasket material: Gaskets are available in a variety of materials, such as rubber, graphite, and PTFE. The gasket material should be selected based on the operating conditions of the piping system, such as temperature, pressure, and the type of fluid being transported. It is important to select a gasket material that is compatible with the flange material and the fluid being transported.
Gasket thickness: The thickness of the gasket can affect the performance of the flange. A gasket that is too thin may not provide sufficient sealing, while a gasket that is too thick may not allow for proper compression of the flange. It is important to follow the manufacturer’s instructions for selecting the appropriate gasket thickness.
Compression: The gasket should be compressed evenly and to the specified compression level to ensure a leak-free seal. Overcompression of the gasket can cause it to fail, while decompression can result in leaks. It is important to follow the manufacturer’s instructions for tightening the bolts to achieve the proper compression of the gasket.
Reuse: Gaskets should not be reused, as they can become damaged or compressed and may not provide a reliable seal. It is important to use a new gasket each time the flange is opened.
Maintenance: Regular maintenance of the gaskets and flanges can help ensure their optimal performance. Inspect the gaskets for signs of wear or damage, such as cracks or tears, and replace as needed. Clean the flange and gasket surfaces before reinstallation to remove any debris or residue that could affect the seal.
Overall, proper selection and use of gaskets with pipe flanges can help ensure a leak-free and efficient piping system. It is important to follow the manufacturer’s instructions and industry standards to ensure proper gasket selection, compression, and maintenance.
C、Precautions and preventative measures
When using pipe flanges, there are several precautions and preventative measures that can help ensure their safe and reliable operation. Here are some key considerations:
Proper installation: Proper installation of the flanges is essential for ensuring their safe and reliable operation. It is important to follow the manufacturer’s instructions for installation, use appropriate gaskets, and ensure that the bolts are tightened to the appropriate torque specifications.
Regular maintenance: Regular maintenance of the flanges and gaskets can help ensure their optimal performance. Inspect the flanges and gaskets regularly for signs of wear or damage, and replace them as needed. Clean the flange and gasket surfaces before reinstallation to remove any debris or residue that could affect the seal.
Corrosion prevention: Corrosion can weaken the flanges and cause leaks or other safety hazards. It is important to select materials resistant to corrosion and to follow appropriate maintenance procedures to prevent corrosion.
Temperature and pressure limits: Pipe flanges are rated for specific temperature and pressure limits. Exceeding these limits can cause flange failure and result in leaks or other safety hazards. It is important to select flanges rated for the maximum temperature and pressure expected in the piping system and to follow the manufacturer’s instructions for installation and use.
Pressure testing: Regular pressure testing is important for identifying any potential issues with the flanges and gaskets. It is important to follow industry standards and manufacturer’s instructions for pressure testing and to conduct regular pressure testing to identify any potential issues.
Overall, proper installation, regular maintenance, corrosion prevention, adherence to temperature and pressure limits, and regular pressure testing are all important precautions and preventative measures that can help ensure the safe and reliable operation of pipe flanges.
V. Safety of Pipe Flanges
A、Safety measures and standards
Safety measures and standards are critical when it comes to the use of pipe flanges. There are several industry standards and regulations that govern the design, installation, and use of flanges, such as ASME B16.5 and API 6A. These standards provide guidelines for material selection, design, and testing, and help ensure that flanges are installed and used safely and reliably.
In addition to following these industry standards, it is important to take additional safety measures when working with pipe flanges. For example, wearing appropriate personal protective equipment (PPE) can help prevent injuries from flying debris or other hazards during installation or maintenance. It is also important to use proper lifting equipment when handling heavy flanges to prevent injuries from lifting or dropping.
Finally, proper training is essential for anyone working with pipe flanges. Training should cover topics such as proper installation techniques, the importance of regular maintenance, and how to identify potential safety hazards. By following industry standards, taking appropriate safety measures, and providing proper training, it is possible to use pipe flanges safely and reliably.
B、How to prevent pipe flange accidents
Preventing pipe flange accidents is critical to ensuring the safety of workers and the integrity of the piping system. Here are some key steps that can help prevent accidents:
Proper installation: Proper installation of pipe flanges is essential for their safe and reliable operation. Follow the manufacturer’s instructions for installation, use appropriate gaskets, and ensure that the bolts are tightened to the appropriate torque specifications.
Regular maintenance: Regular maintenance of the flanges and gaskets can help identify potential issues before they become safety hazards. Inspect the flanges and gaskets regularly for signs of wear or damage, and replace them as needed.
Pressure testing: Regular pressure testing can help identify potential issues with the flanges and gaskets. Follow industry standards and manufacturer’s instructions for pressure testing and conduct regular pressure testing to identify any potential issues.
Corrosion prevention: Corrosion can weaken the flanges and cause leaks or other safety hazards. Select materials resistant to corrosion and follow appropriate maintenance procedures to prevent corrosion.
Training: Proper training is essential for anyone working with pipe flanges. Training should cover topics such as proper installation techniques, the importance of regular maintenance, and how to identify potential safety hazards.
Safety equipment: Wearing appropriate personal protective equipment (PPE) can help prevent injuries from flying debris or other hazards during installation or maintenance. Use proper lifting equipment when handling heavy flanges to prevent injuries from lifting or dropping.
By following these steps and implementing appropriate safety measures, it is possible to prevent pipe flange accidents and ensure the safety of workers and the integrity of the piping system.
C、Accident response and prevention
Accident response and prevention are critical when it comes to the use of pipe flanges. In the event of an accident or leak, it is important to have a plan in place for responding quickly and effectively to prevent further damage and ensure the safety of workers.
Here are some key steps that can help prevent accidents and respond effectively in the event of an incident:
Emergency response plan: Develop an emergency response plan that outlines the steps to be taken in the event of a leak or other incident. Ensure that all workers are trained on the plan and know their roles and responsibilities in the event of an emergency.
Shutdown procedures: Develop shutdown procedures that can be implemented quickly in the event of a leak or other incident. Ensure that workers are trained on the procedures and know how to quickly and safely shut down the piping system.
Containment and cleanup procedures: Have procedures in place for containing and cleaning up any spills or leaks. Ensure that workers are trained on the procedures and have access to the appropriate equipment and materials for containing and cleaning up spills.
Regular inspections: Regular inspections can help identify potential safety hazards before they become accidents. Inspect the flanges and gaskets regularly for signs of wear or damage, and replace them as needed.
Reporting: Ensure that workers are trained on the importance of reporting any incidents or near misses. Encourage workers to report any potential safety hazards, and investigate any incidents or near misses to identify potential improvements to safety procedures.
By following these steps and implementing appropriate safety measures, it is possible to prevent accidents and respond effectively in the event of an incident. This can help ensure the safety of workers and the integrity of the piping system.

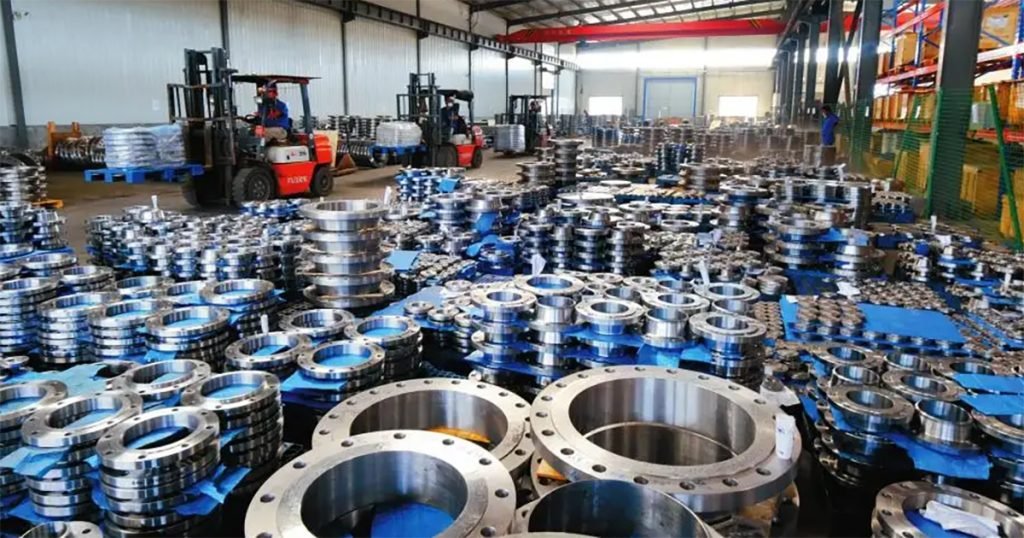
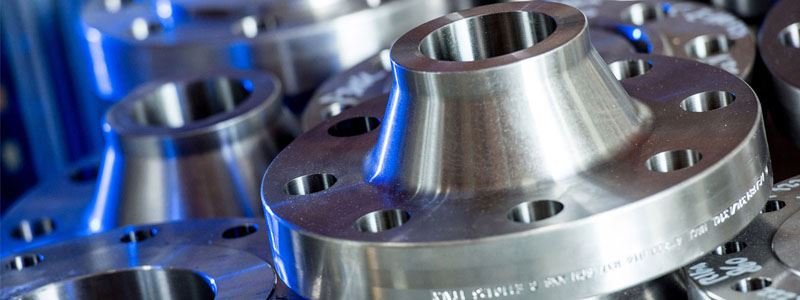
VI. Technological Developments in Pipe Flanges
A、New materials and technologies
Advancements in technology and materials have led to the development of new types of pipe flanges that offer improved performance and durability. Here are some of the new materials and technologies used in pipe flanges:
Composite materials: Composite materials, such as fiberglass-reinforced plastic (FRP), are increasingly being used in pipe flanges. They offer excellent corrosion resistance, lightweight, and high strength.
3D printing: 3D printing technology is being used to create customized pipe flanges with complex shapes and geometries. This technology allows for faster prototyping and customization, which can reduce costs and lead times.
Advanced coatings: Advanced coatings, such as ceramic coatings, are being used to improve the corrosion resistance and durability of pipe flanges. These coatings can protect against harsh environments and extend the life of the flanges.
Smart flanges: Smart flanges, equipped with sensors and communication technologies, can provide real-time data on the condition and performance of the flanges. This can help with maintenance and troubleshooting, and prevent accidents and downtime.
High-performance alloys: High-performance alloys, such as super duplex stainless steel, are being used in pipe flanges for applications that require high strength and corrosion resistance. These alloys can withstand harsh environments and offer improved performance compared to traditional materials.
As technology continues to advance, we can expect to see even more innovative materials and technologies being used in pipe flanges. These advancements will help improve the performance, durability, and safety of pipe flanges in a wide range of applications.
B、Predictions for the future of pipe flanges
The future of pipe flanges is likely to be shaped by advancements in technology and changes in the global market. Here are some predictions for the future of pipe flanges:
Increased use of composite materials: Composite materials, such as FRP, are likely to become even more popular due to their excellent corrosion resistance, lightweight, and high strength. As environmental regulations become more stringent, composite materials will offer a more sustainable and cost-effective alternative to traditional materials.
Adoption of smart technologies: Smart flanges, equipped with sensors and communication technologies, will become more common. These flanges will provide real-time data on the condition and performance of the flanges, enabling predictive maintenance and reducing downtime.
Expansion into new markets: Pipe flanges will continue to expand into new markets, such as the renewable energy sector. Flanges will be needed to connect pipelines in wind farms, solar power plants, and other renewable energy facilities.
Emphasis on safety and reliability: As safety regulations become more stringent, there will be a greater emphasis on the safety and reliability of pipe flanges. New materials and technologies will be developed to meet these requirements.
Integration with automation systems: Pipe flanges will become more integrated with automation systems, enabling remote monitoring and control. This will improve efficiency and reduce the risk of accidents.
Overall, the future of pipe flanges looks promising, with new materials, technologies, and market opportunities driving innovation and growth. As the industry continues to evolve, we can expect to see even more advancements in the design, manufacturing, and application of pipe flanges.
VII. Conclusion
A、Importance and significance of pipe flanges
Pipe flanges play a critical role in the safe and efficient transport of fluids and gases through pipelines. Here are some of the key reasons why pipe flanges are so important:
Connect pipes: Flanges are used to connect pipes together, allowing for the creation of complex piping networks. Flanges can be easily assembled and disassembled, making it easier to maintain and repair pipelines.
Provide a secure seal: Flanges provide a secure seal between two pipes, preventing leaks and ensuring the safe transport of fluids and gases. Properly installed flanges can withstand high pressures and temperatures without breaking or leaking.
Allow for flexibility: Flanges can be used to create flexible piping systems that can handle movement and vibration. This is especially important in industrial applications where pipelines are subject to a lot of stress.
Accommodate different pipe sizes: Flanges can be manufactured in different sizes to accommodate different pipe sizes. This allows for the creation of complex piping networks that can transport fluids and gases of varying volumes and pressures.
Meet industry standards: Flanges are designed to meet industry standards and regulations, ensuring the safe and efficient transport of fluids and gases. This helps to reduce the risk of accidents and ensures compliance with local and international regulations.
Overall, pipe flanges are essential components in the construction and maintenance of pipelines. Without flanges, it would be difficult to create secure and reliable piping systems that can handle the demands of modern industry.
B、Summary and recommendations
To summarize, installing and maintaining pipe flanges is crucial for the safe and efficient transport of fluids and gases through pipelines. Proper installation includes preparing the pipes, flanges, and gaskets, aligning the flanges, tightening the bolts, and testing and verifying the pipeline. Regular maintenance includes checking the condition of the flanges, cleaning them, and addressing any issues promptly to prevent accidents.
Some precautions and preventative measures that should be taken when using pipe flanges include observing pressure and temperature limits, using gaskets correctly, and following safety standards and regulations. It is also important to use high-quality materials and technologies to improve the safety and reliability of the flanges.
In the future, advancements in materials and technologies are expected to improve the performance and durability of pipe flanges. However, it is important to continue following safety standards and best practices to prevent accidents and ensure the safe transport of fluids and gases.
Overall, it is important to prioritize proper installation and maintenance of pipe flanges to ensure their safe and effective operation.
Author: Lewis Liu
Hello, my name is Lewis Liu, and I’m a professional sales engineer with over a decade of expertise in the flange fittings sector.
I am quite informed about flange selection, installation, and maintenance. I am passionate about providing customers with the greatest solutions for keeping their pipeline systems running smoothly, safely, and dependably.
If you have any queries or concerns concerning flange fittings for your pipelines, whether they are about selection, material choice, specification requirements, or anything else, please contact me at any time. I am dedicated to providing expert advice and assistance to help you make educated decisions and reach your objectives.
