Maximizing Performance and Cost Savings with ANSI Flanges: A Guide for Engineers
I. Introduction
Welcome to our guide on Maximizing Performance and Cost Savings with ANSI Flanges. As a leading flange manufacturer based in Cangzhou, Hebei, China, we understand the importance of selecting the right flanges for engineering projects. In this guide, we’ll provide insights and tips on how to select the right flanges for your specific project needs, along with proper installation and maintenance procedures, quality assurance, and certification. Our goal is to help engineers and anyone involved in the selection and installation of ANSI flanges to maximize performance and cost savings.
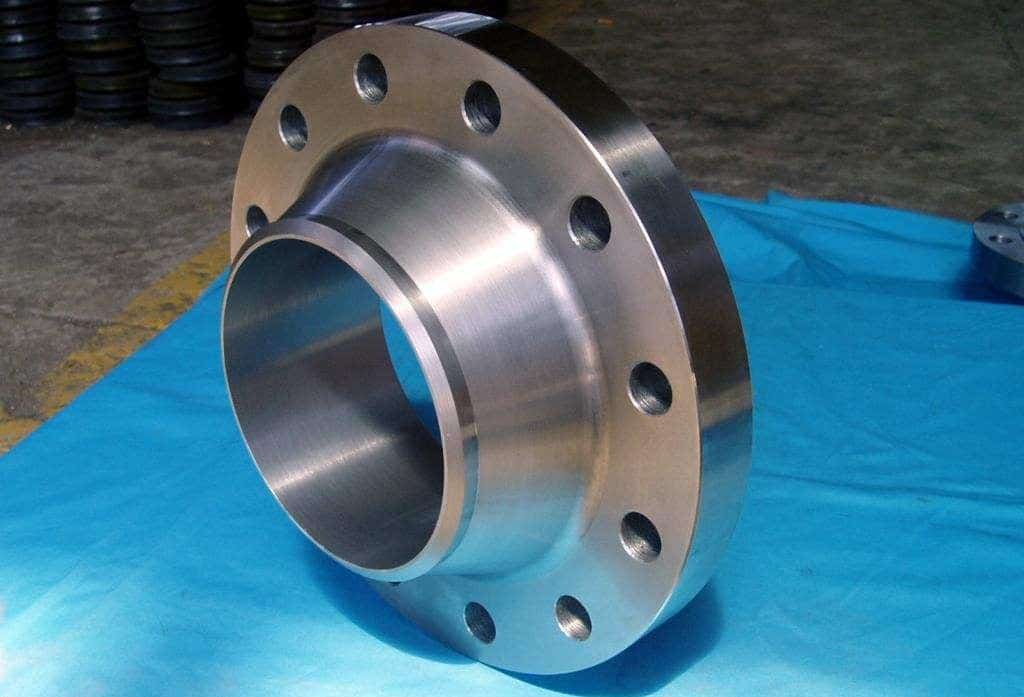
II. Understanding ANSI Flanges
A. ANSI flanges and their purpose
ANSI flanges are a type of flange that conforms to the standards established by the American National Standards Institute (ANSI). These flanges are designed to provide a secure and leak-proof connection between pipes, valves, or other equipment in various industrial applications.
The purpose of ANSI flanges is to allow for easy and efficient connection and disconnection of pipes and equipment while ensuring a safe and reliable seal that prevents leaks and the release of hazardous materials. They are typically used in applications that require high-pressure or high-temperature conditions, such as in the oil and gas industry, chemical processing, power generation, and more.
ANSI flanges come in various sizes, shapes, and materials, allowing for flexibility in design and application. Their standardized design ensures that they are interchangeable between manufacturers and suppliers, making them a widely used and trusted solution in industrial piping systems.
B. The various types of ANSI flanges and their applications
There are several types of ANSI flanges, each with unique designs and applications. Here are some of the most common types of ANSI flanges:
- Weld Neck Flanges: These flanges are designed with a tapered neck that is welded to the pipe, providing a strong and reliable connection. They are often used in high-pressure and high-temperature applications, such as in the petrochemical industry.
- Slip-On Flanges: These flanges slide onto the pipe and are then welded in place. They are easier to install than weld neck flanges but are not as strong and are typically used in lower-pressure and temperature applications.
- Blind Flanges: These flanges are used to seal off the end of a pipe, valve, or equipment. They are typically used in applications where future access to the pipe is not required.
- Threaded Flanges: These flanges have internal threads that allow them to be screwed onto the pipe. They are often used in low-pressure and low-temperature applications.
- Socket Weld Flanges: These flanges are designed to fit over the pipe and then be welded in place. They are typically used in high-pressure and high-temperature applications.
- Lap Joint Flanges: These flanges are designed to slide over the end of the pipe and are then held in place with a stub end. They are typically used in applications that require frequent dismantling and assembly.
The choice of flange type depends on the specific requirements of the application, such as pressure, temperature, pipe size, and materials. It is essential to consult with a qualified engineer to determine the appropriate type of flange for a given application.
C.Benefits of using ANSI flanges
There are several benefits of using ANSI flanges in industrial piping systems, including performance improvements and cost savings.
Firstly, ANSI flanges provide a secure and reliable connection between two pipes or components, ensuring a leak-free operation. This reduces the risk of accidents, enhances safety, and minimizes downtime for maintenance and repairs.
Secondly, ANSI flanges are highly customizable and can be designed to fit a wide range of pipe sizes and configurations. This allows for greater flexibility in piping system design and installation, which can improve overall system performance and efficiency.
Thirdly, ANSI flanges are made from high-quality materials such as stainless steel, carbon steel, and alloy steel, which offer excellent corrosion resistance and durability. This ensures a longer service life for the flanges and reduces the need for frequent replacements or repairs, resulting in significant cost savings over time.
Lastly, ANSI flanges can be easily installed and removed, which simplifies maintenance and repair operations, reducing labor costs and downtime. Overall, the use of ANSI flanges in industrial piping systems can provide significant benefits in terms of performance improvements and cost savings.
III. Factors to Consider When Selecting ANSI Flanges
A. When selecting ANSI flanges for a specific project, it is important to consider several factors, including material, pressure rating, and size. The material of the flange should be chosen based on compatibility with the fluid being transported and the operating conditions of the system. The pressure rating of the flange must also be considered to ensure that it can withstand the maximum pressure of the system without failure. Additionally, the size of the flange must match the size of the pipes or components being connected to ensure proper alignment and a secure connection.
B. Different factors can affect the performance and cost of a project. For example, selecting the wrong material for the flanges can lead to corrosion, leaks, and failures, resulting in increased maintenance and repair costs. Choosing a flange with a lower pressure rating than required can lead to system failure and downtime, which can also increase costs. Similarly, selecting the wrong side of the flange can cause alignment issues, leading to leaks and the need for expensive repairs.
C. To select the right ANSI flanges for a specific project, it is important to consider the specific requirements of the system, such as the fluid being transported, the operating conditions, and the maximum pressure and temperature. Consulting with a knowledgeable supplier or engineer can also help ensure that the right flanges are selected for the project. It is also important to choose flanges from reputable manufacturers that meet industry standards and have a proven track record of performance and reliability. Regular maintenance and inspection of the flanges can also help prevent issues and extend their service life.
IV. Installation and Maintenance of ANSI Flanges
A. Proper installation and maintenance of ANSI flanges are crucial to ensure optimal performance and safety. During installation, it is important to follow the manufacturer’s guidelines and use the correct tools and techniques. The flange faces must be clean and free of debris, and the bolts should be tightened to the recommended torque values in a criss-cross pattern. After installation, regular maintenance is necessary to prevent leaks and failures. This includes checking for signs of corrosion or wear, replacing damaged gaskets or bolts, and tightening loose bolts.
B. Manufacturers provide specific recommendations for the maintenance and inspection of their ANSI flanges. It is important to follow these guidelines to ensure that the flanges perform as intended and to prevent safety hazards. Failure to follow the recommended maintenance procedures can lead to premature wear, leaks, or even catastrophic failure.
C. Common installation and maintenance issues include improper torque values, misaligned flanges, damaged gaskets, and corrosion. To address these issues, it is important to carefully follow the manufacturer’s guidelines for installation and maintenance. For example, if bolts are not tightened to the recommended torque values, the flanges may leak or fail. If flanges are misaligned, it may be necessary to reposition them or use shims to ensure proper alignment. Damaged gaskets should be replaced promptly to prevent leaks, and regular inspections for corrosion can help identify potential issues before they become major problems.
V. Quality Assurance and Certification for ANSI Flanges
A. Quality assurance is critical for ANSI flanges to ensure they meet the required standards and are safe to use in various applications. Poor quality or substandard flanges can lead to costly and dangerous consequences, such as leaks, bursts, and other accidents.
B. There are various certifications and standards that are available for ANSI flanges. For instance, ANSI B16.5 is the standard specification for pipe flanges and flanged fittings in sizes from 1/2″ to 24″. It provides dimensions, tolerances, materials, and other technical requirements for ANSI flanges. Other common standards include ASTM, ASME, API, and ISO.
C. Working with a certified and reputable manufacturer is crucial to ensuring the quality of ANSI flanges. A certified manufacturer will follow the required standards and regulations to produce high-quality flanges that meet the specified requirements. They will also perform testing and inspection to ensure the flanges meet the required quality and safety standards, reducing the risk of failure or accidents. Additionally, a reputable manufacturer will provide excellent customer support and after-sales services, helping customers with installation, maintenance, and other issues that may arise during the project.
VI. Conclusion
As the author of this blog, I hope that the information provided has been helpful in understanding the importance of selecting the right ANSI flanges for engineering projects. Material, pressure rating, size, installation, maintenance, and certification are all critical factors to consider when choosing the appropriate flange for your project.
It is important to remember that selecting the right ANSI flange can have a significant impact on the performance, reliability, and cost-effectiveness of your project. By working with a certified and reputable manufacturer, you can ensure that the flanges you use meet the necessary quality standards and have been tested to perform in a range of applications.
I encourage readers to reach out to our company for further assistance and information on selecting the appropriate ANSI flanges for their specific projects. Our team of experts is always available to provide guidance and support to ensure the success of your engineering projects.
Author: Lewis Liu
Hello, my name is Lewis Liu, and I’m a professional sales engineer with over a decade of expertise in the flange fittings sector.
I am quite informed about flange selection, installation, and maintenance. I am passionate about providing customers with the greatest solutions for keeping their pipeline systems running smoothly, safely, and dependably.
If you have any queries or concerns concerning flange fittings for your pipelines, whether they are about selection, material choice, specification requirements, or anything else, please contact me at any time. I am dedicated to providing expert advice and assistance to help you make educated decisions and reach your objectives.
