What causes a flange to leak?
Flanges are very important to piping systems because it provides for a secure connection between two pipes. Nevertheless, flange leaks do pose a grave threat to safety, hamper operation, and cause financial losses. To maintain integrity of the piping system, the causes of flange leak development must be understood and preventive measures should be implemented.
In this article, we’ll be discussing the causes of flange leaks, such as common installation techniques, defects in materials, gasket failure, and difficult operating conditions. We will also show the possible consequences of flange leaks: safety risks, operation interruption, possible legal penalties.
We will also give you step-by-step guidance on how to avoid flange leakage and, therefore, render the following helpful for you.

Causes of Flange Leaks
Details for each of the common causes of flange leaks are provided below.
Improper installation techniques or insufficient bolt tightening
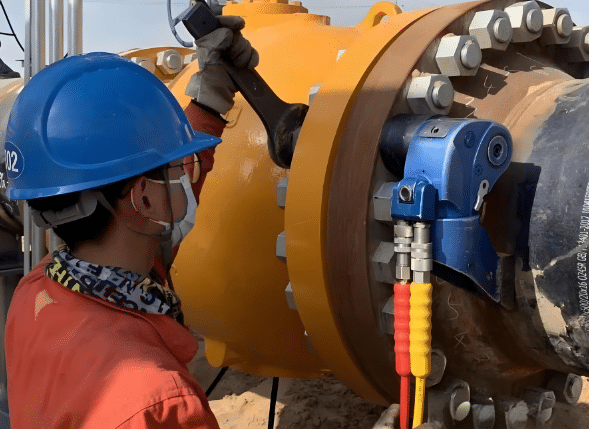
Two major reasons for flange leaks are from improper installation techniques and not tightening the bolts enough. As the gaps and the uneven pressure distribution can lead to leakage over time, flanges are not usually installed correctly or bolts are not tightened adequately. Here are some detailed explanations of these issues and possible solutions:
Improper Installation Techniques:
- Gasket misalignment: Poor alignment of the gasket to the flange faces may cause some leakages. The Center of the gasket needs to be exactly in the middle while installing.
- Uneven surface preparation: Poor cleaning or mechanical damage to flange surfaces can be a reason for nonuniform mating of the parts, leading to leakage. Clean the flanges thoroughly before installation, eliminating from their surfaces all the debris and contaminants.
- Incorrect flange assembly: All flange parts should be properly aligned, and properly assembled according to the specification and standards. Make sure that the bolts, nuts gaskets and flanges are in the right places and the right orientation.
Insufficient Bolt Tightening:
- Under-tightening: Insufficient tightening of the bolts may result in gaps between the flanges; hence, leakage can easily occur. Ensure that during bolting, tensioning of a bolt is at its correct value according to the recommendations of the manufacturer by following the proper tightening sequence.
- Over-tightening: Due to the bolt tightening, and subsequent deformation of the flange, a crack or other damage may occur that can even lead to leaks. Apply a force with the correct torque wrench to not over tighten.
- Uneven bolt tightening sequence: Bolts must be tightened in a specified sequence in a view to distribute the load and pressure across the flange faces. Also, stress the suggested pattern of tightening-star or crisscross-for a good uniform clamping force.
To tackle these problems, it’s imperative to spend some time and effort on how to properly install the deck and on engaging the correct bolt tightening procedures. It is important to ensure their training and education of personnel involved in the flange installation is proper so they do know and do follow the correct procedure. Therefore, it can also offer an early warning if flange connections are subjected to regular inspection and maintenance before the problem becomes a leak. Errors in installation techniques and the wrong way of tightening bolts can be prevented from maximizing the flange leak in order to maintain the system integrity and reliability.
For flange installation, please check: How to install pipe flanges?
Flange material defects or damage
Flange material defects or damage can also be one of the causes of flange leaks. Here are some of them with detailed explanations of problems and possible solutions respectively:
Material Defects:
- Inclusions or impurities:Poor quality materials may have inclusions or impurities that provide weak structural integrity to the flange, and thus opportunities for leakage. The better the quality of the flange material selected, the better the flange will be, and one should receive those from the best suppliers.
- Porosity or voids: Porosity or voids in the structure of the flange can give way to leakage. Do appropriate material tests and quality control to ensure there is no porosity or void structure.
- Inadequate material strength:If the material used to make the flange does not possess the right strength or resistance to chemical action for a particular application, this inevitably leads to early failures and leakage. Therefore, in selecting flange materials, consideration must be given according to the pressure requirement, temperature, and medium conveyed.
Please refer to the selection of materials: How to choose pipe flanges of different materials?
Flange Damage:
- Corrosion: Loss of strength in flange material and accompanying corrosion may lead to cracks, pits or holes that promote leakage. Flange materials should use good resistance to corrosion materials such as stainless steel or alloy steel.
To know more about corrosion prevention see: How to Prevent Pipe Flange Corrosion?
- Mechanical damage: Flanges may be damaged in handling, shipping or installation, and develop cracks or other deforming which may impair their service performance. Flanges should be handled carefully and visually inspected before installation for any signs of damage. Damaged flanges should be replaced without delay.
- Aging or degradation: Flanges will deteriorate with age due to environmental exposure or operating conditions. A flange has to be checked and monitored for aging over a regular period, and replaced if required.
Defective or damaged flange material should be handled in close cooperation with material suppliers and according to specific standards and specifications of the industries. It is important that quality control, material testing, and inspections are rigorously performed in order to find defects or potential defects in the equipment before installation. Regular maintenance and monitoring of flanges will enable rapid detection and immediate resolution of the first signs of deterioration or damage for a reliable and leak-free flange connection.
Improper size selection

Dimensional problems can also be a cause of flange leakage. Some of the possible dimensional causes include:
Mismatched flange sizes: A bad seal can occur if the flange sizes don’t match or are not meeting required standards. Choose flanges of exactly the size as specified, and use flange connection guidelines as per the appropriate standards during installation.
Uneven flange surfaces: An uneven, dented or rough flange surface may not give an effective seal. Flat flange surfaces can be created by proper surface preparation e.g. grinding, facing or gasketing. Use a proper gasket to compensate for any unevenness on the surface imperfections and seal better.
Specified flanges and gaskets shall be used to avoid flange leakage from dimensional problems. During installation, ensure that the flange surfaces are flat and smooth, appropriate gaskets are used, and bolts are fitted in the correct way and pre-tightened by following specifications in a published guideline. The flange connection shall be checked after the installation whether some adjustment or replacement is needed for tight sealability.
Discuss with experts or engineers for proper dimension and installation guidance or check: How to choose the correct pipe flange size?
Gasket failure due to improper selection or degradation over time
Gasket failure may be caused either by poor selection or by degradation of the gasket over a period of time. The following are a few explanations of such issues and their likely solutions:
- Incompatible material: Incompatibility of the gasket material with the fluid conveyed or operating conditions can also cause failure. It includes temperature, pressure, or chemical compatibility, among other application-specific requirements in choosing the gasketing material.
- Inadequate compression or recovery properties: Gaskets rely on sufficient compression to provide a proper seal. If a gasket material does not have suitable compression characteristics, or recovery after having been compressed, it cannot sustain an effective seal under changing operating conditions. A gasket must be selected which has the requisite degree of compression, as well as recovery, necessary to accommodate joint movement and pressure or temperature fluctuation.
Degradation Over Time:
- Aging: Over time environmental factors including temperature, UV radiation, moisture and even chemical exposure can degrade the gaskets. Such leakage or loss of elasticity is the result of shrinkage, hardening, cracking, which may appear as such. Provide for regular inspection and replacement of gaskets that show signs of aging.
- Chemical attack: Exposure to aggressive chemicals or corrosive fluids will lead the gasket materials to become deteriorated. Ideally, ensure gasket materials are resistant to the specific chemicals in the system so they will not degrade and maintain long term sealing effectiveness.
- Thermal cycling: Often gasket materials are subject to expansion and contraction from temperature variations resulting in fatigue and eventual failure. Gasket materials need to be selected for good thermal stability and resistance in order to maintain their sealing properties under thermal cycling conditions.
Proper selection of gaskets will prevent its failure. Consult manufacturers or gasket specialists in the selection of materials most compatible for the given application, considering variables such as chemical compatibility, temperature range, and operating conditions. Gaskets should be inspected on a regular basis for wear, degradation, or leakage, with replacement as required. Monitoring and maintenance of gasket integrity through regular maintenance and replacement will serve to prevent leaks and ensure reliable sealing in flange connections.
Operating conditions such as high pressure, temperature, or corrosive environments
Operating conditions of high pressure, temperature, or corrosive environments have great effects on gasket performance and may lead to failure. How these conditions affect gaskets and some possible solutions:
High Pressure:
- Compression loss: The gaskets applied in high-pressure applications should possess sufficient characteristics of compression and recovery for the establishment and sustenance of tight sealing. Poor or insufficiently compressing seals lead to leakage. Gaskets for high-pressure applications must be selected as such and installed with adequate compression.
- Blowout: Too much pressure will cause gaskets to blow out or extrude from a flange, thus creating leaks. Appropriate pressure rating is one of the consideration in the selection of gaskets and one may look to options of reinforcement such as metal inserts or rings to improve stability at high pressure service.
High Temperature:
- Thermal degradation: Air and thermal aging of high temperature gaskets compromise their elasticity and thus, may lead to reduced sealing performance or total failure. Choose gasket materials which will match high temperature application and ensure that the materials they will be working at will operate at that temperature.
- Differential thermal expansion: Since the different types of materials forming the flange joint expand at different coefficient rates due to such fluctuations in temperature, stress is put on the gasket and the seal is compromised. This can be minimized by selecting gaskets with a good dimensional stability, and having materials with low thermal expansion coefficients into consideration.

Corrosive Environments:
- Chemical attack: Gasket materials will tend to degrade from corrosive fluids or surrounding environments, losing their ability to seal and creating leaks. Gasket materials shall be selected to provide good chemical resistance against the specific fluids; application of corrosion inhibitors and protective coatings may be considered where possible.
- Erosion or wear: Aggressive media can lead to erosion or wear of gaskets over time in certain high-velocity flow applications. In such situations, select gaskets made from erosion/wear-resistant materials or those reinforced with additives that are suitable for their application.
When it comes to pressure, temperature or any harsh environment, the type of gaskets that are needed have to be selected carefully. Consult the gasket makers or gasket experts when choosing the types and materials of gaskets. Examine gaskets for indications of deterioration and leaking, and replace them to improve the seal and lessen flange joint leakage.
Vibrations or thermal cycling environmental factors
Gasket performance is challenged and failure is possible due to environmental factors such as vibrations or thermal cycling. Following are some explanations of these factors, and their possible effects upon gaskets, along with probable solutions:
Vibrations:
- Gasket loosening: Vibration can loosen bolts or fasteners over time, which typically reduces applied compressive force on the gasket, followed by leakage. Installing locking devices, vibration-damping materials, or even the right torque specification are required to prevent this process.
- Surface wear or fretting: Repeated vibration can cause surface wear on gasket materials, or fretting corrosion on the flange surfaces, which compromises the sealing integrity. Gaskets of materials with good wear resistance and/or corrosion protection should be considered. Adequate preparation of surfaces, for example cleaning and applying suitable coatings, may also prevent these wear and corrosion problems.
Thermal Cycling:
- Differential expansion and contraction: Frequent temperature changes can cause gaskets, flanges and other materials to expand and contract at different rates and applying more stresses to the gasket that can result in its failure. For resisting thermal cycling without seal compromise, the gasket materials should have good dimensional stability with low thermal expansion coefficient.
- Embrittlement: The gasket will eventually embrittle due to the impact of alternating temperature extremes, which will reduce flexibility and conformance to the flange surface. Choose only those gasketing materials specifically designed for thermal cycling applications or those possessing superior temperature resistance and adequate flexibility to withstand dynamic temperature fluctuations.
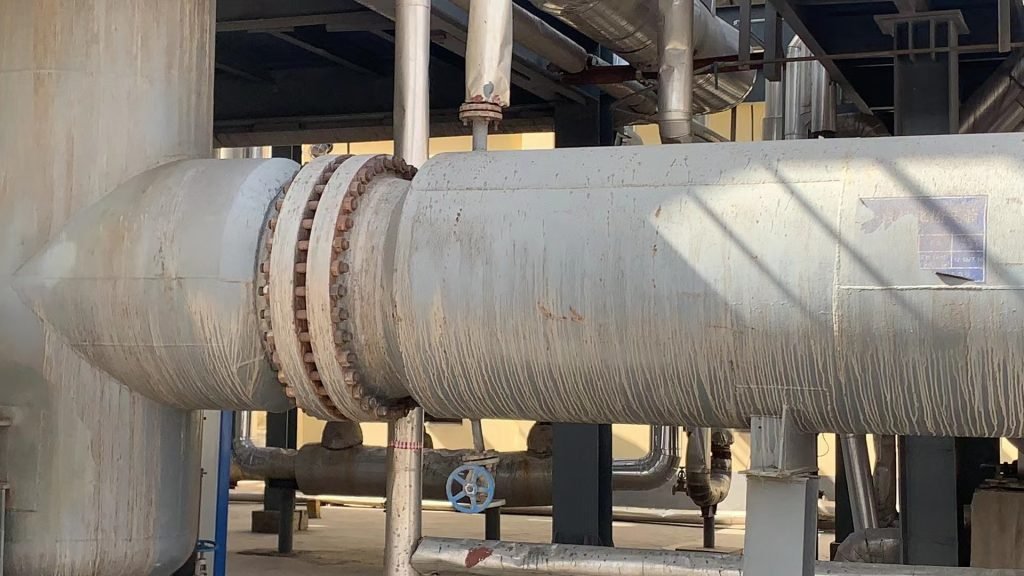
If you plan on using it in some sort of application subject to environmental factors such as vibrations or thermal cycling, you’ll need to think about gasket materials and installation methods which can tolerate those conditions. Speak with gasket manufacturers or industry subjects that can describe suitable materials and designs that are resistant to vibrations, wear, corrosion and thermal cycling. Inspection of gaskets, to identify wear, damage or leakage, should be scheduled regularly, and the gaskets should be maintained or replaced to keep them effective in sealing flange connections which are exposed to these environmental factors.
Correct installation, periodic inspections, and maintenance of flanges are ways to have preventive measures against leakage and quality assurance. Material selection shall be appropriate with respect to operating conditions; vibration isolation; and industrial standards and regulations. Involvement of reputable suppliers and professionals, such as Yanhao Pipeline Equipment Co., Ltd., may further ensure the reliability and integrity of flange systems.
Impact of Flange Leaks
Here are more details on the impact of flange leaks:
- Safety hazards and potential environmental damage: Leaks through the flange may emit toxic chemicals, gasses, or other hazardous, flammable materials. Hence, this can raise chances of a greater danger to personnel safety in the vicinity of the leak. In cases where these leaked materials interact with the environment, soil, water, or air pollution could result, causing serious damage to the environment and even being harmful to ecosystems and human health.
- Regulatory compliance risks and legal implications: Flange leakage can lead to failure to comply with regulatory demands in workplace safety, environmental protection, and emissions control. The worst of consequences of non-compliance, aside from litigation tacked with fines and penalties, could be the loss of an organization’s good name. Business enterprises should consider flange systems that are capable of meeting the prevailing standards and regulations to avoid litigation and the interference of regulatory bodies.
- Operational disruptions, downtime, and financial losses: Flange leakage can disrupt regular activities since the involved equipment or piping system may be taken out of service for repair. Thus, it could lead to production downtime, lower productivity, and financial loss. Repairs, replacement of damaged components, and cost of lost production are some of the substantial business expenses that contribute.
By understanding the likely impact brought about by flange leaks, an organization can, therefore, create a plan to avoid and mitigate the incidents. The major safety measures include taking the time to develop good protocols of safety that focus on regular maintenance and inspections, employing quality materials, and continuing to follow regulations and industry standards that minimize risks of flange leaks and their associated consequences. Working with professionals and suppliers, such as Yanhao Pipeline Equipment Co., Ltd., may also be quite resourceful in offering the guide and support necessary in ensuring that flange systems are safe and dependable.
Preventing Flange Leaks
Importance of proper torquing and bolt tightening procedures
The proper torquing and tightening procedures of bolts are critical in minimizing flange leaks. This is due to the following reasons:
- Ensures uniform pressure distribution: The right torque and bolt-tightening methods reduce the occurrence of localized irregularities on the gasket seal by evenly distributing the pressure. Applying the right amount of torque on each bolt will ensure even load distribution to prevent areas of low or high pressure that could lead to leaks.
- Promotes a secure and reliable seal: The reason adequate bolt tightening assists in creating a tight and secure seal between the flange faces and the gasket is very important, since it deters any gap or space that might allow the fluids or gasses to escape. A correctly tightened bolt exerts the needed compressive force on the gasket, thus allowing a very effective seal that withstands leakage.
- Stops over- or under-tightening: In helping prevent over or under tightening of bolts, consistently applying the correct torque is applied. Failure can occur due to over tightening, wherein the gasket is forced to deform, or due to under tightening, where not sufficient compressive force is exerted by the gasket to act as a seal. As per manufacturer’s specifications guidelines they tightly tighten the bolts so that the desired seal is achieved.
- Reduces the risk of loosened bolts: Good practice torquing and tightening reduces the risk that the bolts will loosen up during operation. The bolts are not always going to be tight so they cannot stay tight most of the time, so most of the bolts are loose, because of vibrations, temperature fluctuation or other environmental factors. Moreover, unsecured bolts do pose a danger of leaks. When bolts are torqued correctly, the possibility of the leakage due to loose hardware is much smaller.
- Ensures compliance with industry standards: In flange installations, many industry standards and regulations give guidelines and requirements for torquing and bolt tightening. Following these standards ascertains the regulatory compliance as well as achieves the scope of safety and quality assurance.
Good torquing and bolt tightening procedures are necessary to ensure the seal is secure and reliable in flange connections. Organizations can reduce flange leak risks caused by improper installation techniques and fail to follow manufacturer’s guidelines by investing in proper installation techniques.
Proper gasket material selection and compatibility with the media and flange
Making sure the gasket material is compatible with the flange and media requires careful selection. It is a necessary component because:
- Sealing effectiveness: Gaskets function to provide a physical barrier between the flange faces, preventing fluid or gas leakage. Proper selection of gasket material is necessary to achieve an effective seal. A variety of types of gasket materials are offered in their resistive pressure, temperature, and chemical exposure. The use of a gasket material matched to the operating conditions can provide an optimal seal with less chance of leakage.
- Chemical compatibility: In resistance to chemicals and other media, different gasket materials show different properties. For this reason, it is required to select a material of gasket chemically compatible with the fluid or gas to be transported. Chemical incompatibility can lead to material degradation, swelling, or decomposition of the gasket, resulting in leaks. Knowledge of compatibility among gasket material, flange, and media is very important to ascertain that any chemical exposure that may occur is withstood by the gasket without losing its integrity and sealing capability.
- Temperature and pressure resistance: The properties of gasket materials enable them to withstand a range of different temperatures and pressures. Material failure from operating conditions outside the parameters of the gasket material often results in premature deterioration, which in many cases means leakage. Selection of a material suitable for withstanding the expected temperature and pressure fluctuations that may occur within the system is very important. It ensures that the gasket will be resilient over time and its sealing properties will not lose efficacy.
- Flange compatibility: Gasket materials should be compatible with the flange materials so that galvanic corrosion or even chemical reaction can be avoided. Because of this consideration, the gasket material shall be chosen with regard to the flange material so that negative reactions that may degrade the flange and affect the seal will not take place.
- Longevity and reliability: Selection of gasket material is normally made compatible with the flange and media for the system to live long and be reliable. Appropriately selected gasket material stands a better chance of having a longer service life with minimal changes or repairs that may be required. This reduces the likelihood of any leaks through the flanges and saves some essential hours, reducing maintenance costs.
Material selection must be done with reputed suppliers or manufacturers who can propose the proper material operating under conditions and requirements. A careful decision about the compatibility of gasket materials will definitely ensure a reliable and leak-free flange connection.
Surface preparation
Good surface preparation is a prerequisite for a successful seal. In case of a flange connection, good preparation of the surfaces has the following reasons:
- Elimination of contaminants: The goal of surface preparation is to eliminate impurities such as dirt, oil, grease, corrosion, and old gasket material on the faces of the flanges.The existence of such contamination defeats the effectiveness of a gasket and leads to leaks. Removing them cleans the surface for the gasket to make direct contact with the flange faces and helps provide a safe and reliable seal.
- Enhances adhesion: The process of surface preparation may involve roughening or micro-roughening of the flange face, particularly by grinding or abrasive blasting. This roughening increases the area of contact between the gasket and the flange faces thus enhancing bonding and the ability of the gasket to penetrate within and seal any imperfections on the finish. This increase in adhesion characteristically decreases the risk of leakage of any fluids or gasses through the seal.
- Smoothing high spots and ensuring flatness: Surface preparation might include high spots or imperfections to be removed from the flange faces. High spots could interfere with the gasket’s proper contact with the flange, causing local areas of uneven compression that might be promoting leakage. Smoothing out high spots tends to promote uniformity in compressive force across the gasket for an effective seal. Besides, confirmation of the flatness of the flanges is very much essential to avoid any possible shortcomings in seal capacity. Lapping or machining operation on the surface of flanges might be required in order to get the desired flatness.
- Avoids damage to the gasket: Proper surface preparation will prevent any damage to the gasket at the time of installation. For instance, a gasket material may be torn or cut by roughness and jagged edges on flange faces, breaching its integrity. In preparing flange surfaces, one can reduce gasket damage to ensure a longer service life.
- Complies with industry standards: Specifications and standards often require or recommend that industry standards and specifications are followed in preparing the surface. Indeed, compliance and proper installation practices, safety, and environmental stewardship are ensured if such guidelines are met.
Methods of surface preparation by blast cleaning, pickling, wire brushing, or other methods shall be performed in accordance with the recommendations of the manufacturer, industry standards, or project-specific requirements. Tools, materials and techniques used shall be appropriate for the desired surface cleanliness, roughness, and flatness. The quality of the surface preparation, combined with proper gasket material and bolt tightening procedures, is critical to tightness and reliability for a seal in flange connections that minimize leaks, ensuring the safety and efficiency of the operation.
Proper alignment
Proper alignment ensures that the connection of the flanges will be leak-free and reliable. The reason proper alignment is important includes the following:

- Even distribution of load: Proper alignment promotes even distribution of the load from the bolts across the flange faces and the gasket. Poorly aligned flanges create an imbalance in the load and may cause stress concentration points that can result in leaks. Proper alignment makes sure that the load is uniformly distributed around the flange, promoting a secure and even sealing pressure across the gasket.
- Prevents gasket deformation: Improper alignment can result in distortion of gaskets either at the time of installation or during operation. Gaskets are designed for operating compressive stresses within their elastic limit to produce an effective seal. Misaligning the flanges causes excessive stress or deformation which may crush, extrude, or displace the gasket, creating possible leakage paths and loss of seal integrity. Good alignment reduces the possibility of gasket distortion and damage.
- Sealing surface contact: Good seals are achieved by having the flanges’ sides fully and evenly in contact with the gasket when these are in position. The probable causes of leak sites may be due to the facial gaps and misalignments between the flanges and the gasket. A proper alignment of the flanges increases the contact area between the gasket and the flange surfaces, improving sealing and lowering the possibility of leaks.
- Bolt alignment: Proper alignment allows for proper bolting system alignment. Poor alignment results in improper bolt engagement of the bolts when they cannot share the load correctly or lock the flange in position properly. Such uneven tightening creates areas of increased stress concentration that may result in leaks or flange failure. Proper alignment ensures proper functioning of the bolting system: a securely and consistently loaded bolt.
- System integrity: Proper flange alignment is critical to ensure the integrity of the general system. Misalignments may give rise to excessive stress or distortion on the connected equipment, pipelines, and other components. This may further cause mechanical stress, fatigue, or system failure. Proper alignment shall help the system to last long, be reliable, as excessive loads and stresses are minimized on the components.
The installation or maintenance should carefully position and align the flanges for proper alignment. The use of various alignment tools, such as jacks, dial indicators, or laser alignment systems, facilitates precise alignment. Manufacturer guidelines related to the standards of the industry and best practices about flange alignment will make sure that the connection is not only effective but also leak-free.
Inspections and maintenance
Inspections and maintenance are important, which ensures continuous performance, reliability, and safety of the flange connections. Here’s why inspections and maintenance are important:
- Early detection of issues: Regular inspections can easily enable the identification of any of the probable problems of the flange connections. These include wear, corrosion, leakage, misalignment, and other types of damages that could be compromising the integrity of the connection. Precognition of such issues means early and effective corrective measures that could reduce the possibility of costly repairs, downtimes, or safety risks.
- Preventive maintenance: Regular maintenance will prevent sudden failures and breakdowns. Activities in this regard include lubrication of bolts and nuts, gasket inspection and replacement, checking of bolt tightness, flange alignment checks, and cleaning of flange surfaces. Carrying out preventive maintenance affords you the chance to find those little problems that are brewing, which allows you to avoid their growth into major ones and ensure continued performance and reliability of the flange connection.
- Ensure compliance with standards: Inspections and maintenance ensure that industry standards, regulations, and best practices are adhered to. Application guidelines can be helpful in maintaining a safe and reliable operation. Any verification on whether the flange connections have met requirements is done through inspection, and deviation or non-compliance can be taken care of through maintenance activity.
- Extend service life: Regular inspection and maintenance have been put in place to help extend the service life of a flange connection. You identify problems early enough to prevent premature failure, reduce leakage, and costly repairs or replacement. Well-maintained flange connections stand a better chance of performing effectively for their estimated lifespan.
- Safety and environmental protection: The contribution of inspections and maintenance to general system safety and environmental protection is crucial. Leaks in flange connections may create dangerous situations that could lead to accidents, injuries, or property damage. Periodic inspections and other maintenance activities enable one to find the presence of leaks and repair them in order to keep the environment safe for operation. In addition, taking action early reduces the risk of environmental contamination that may occur due to leaks.
To perform inspections, competent personnel shall have experience in flange connection standards, inspection techniques, and wear criteria. Inspection shall be performed by appropriate tools and techniques, such as by visual, by nondestructive test methods (liquid penetrant or magnetic particle testing), or by ultrasonic inspection.
With the institution of these preventive measures and partnering with companies like Yanhao Pipeline Equipment Co., Ltd., a company will be able to reduce the chances of flange leakages, hence making the piping system much safer and reliable.
Choose a flange with quality assurance
When it comes to selecting a flange based on quality assurance, the following are some of the key factors that must be put into consideration:
- Certification and compliance: The incoming flanges shall be manufactured to meet internationally accepted standards for quality such as, but not limited to B16.5 or B16.47 of ASME, ISO 9001 certification stating that the manufacturer follows a quality management system.
- Material quality: Choose the flanges fabricated from premium materials such as carbon steel, stainless steel, and other alloys according to the demand for the specific application. All the materials must be per the demand of corrosion resistance and strength, with sufficient mechanical properties.
- Manufacturing processes: Follow the manufacturing process, including quality control by the manufacturer. Ensure that raw materials are sourced, processes are controlled, inspection, and testing is done. The manufacturer shall have appropriate process flows in place to ensure the consistency of the products for the quality stability of said products.
- Testing and inspection: Learn about investment by the manufacturer in testing the quality of the products and inspection. Generally, high-quality flange manufacturers always carry out serious tests and inspections, including but not limited to the following: dimensional measurement, material analysis, pressure test, eddy current or ultrasonic test. Such inspections help to ensure that the flanges meet the requirements of specifications and have good performance.
- References and reputation: Customer reviews and the manufacturer’s reputation go a long way. This helps in reading the experience and opinions of previous users, which help in understanding the quality of the flanges better.
It is necessary to conduct comprehensive research, make some price comparisons among different suppliers and their products, and consider your specific needs and expectations for what you want to purchase.
YANHAO at your Service
As a leading provider in flange solutions, YANHAO provides rich experience and capability in this field. Specialized in making flanges to the client’s demand and requirement, it is able to provide unusual design or non-standard sizes. This feature, combined with the ability of YANHAO’s staff to apply special materials, promotes the provision of customized flanges that perfectly match the needs of the client.
Among the main strengths of Yanhao lie the many varieties of material available for flange production. We could supply different kinds of material, such as stainless steel, alloy steel, and carbon steel for flanges. Having a great variety of materials supplies assures that customers can be provided with the most suitable application based on various options, such as corrosion resistance, strength, and compatibility with the environment in which they work.
Yanhao was dedicated to the quality of every product manufactured. It had invested in state-of-the-art production and testing equipment to ensure reliability and performance of the flanges. This entailed employing the latest machining tools, inspection devices, and test instruments. By using these technologies, Yanhao will adopt precise manufacture and thorough quality control processes so that all its flanges are assured of meeting the highest quality standards.
- Hardness testing
- Magnetic particle inspection
- Thickness measurement
- Direct-Reading Spectrometer
- Hardness testing
- Metallographic Analyzer
- Physical and chemical testing
- Tensile Testing Machine
- Ultrasonic testing
- Engineers are performing non-destructive testing on flanges
In a nutshell, Yanhao has earned a good reputation in the market for professional customization of flanges, varieties of materials such as stainless steel, alloy steel, and carbon steel, and assurance in product quality due to advanced production and testing equipment.
Author: Lewis Liu
Hello, my name is Lewis Liu, and I’m a professional sales engineer with over a decade of expertise in the flange fittings sector.
I am quite informed about flange selection, installation, and maintenance. I am passionate about providing customers with the greatest solutions for keeping their pipeline systems running smoothly, safely, and dependably.
If you have any queries or concerns concerning flange fittings for your pipelines, whether they are about selection, material choice, specification requirements, or anything else, please contact me at any time. I am dedicated to providing expert advice and assistance to help you make educated decisions and reach your objectives.
