How to Choose the Suitable Flange Type? – Expert Guide for Flange Selection
Before discussing how to choose the right flange type, it is important to understand what a flange is and its significance in a pipeline system. A flange is a critical component used to connect pipes and equipment, providing a secure connection while allowing for disassembly and maintenance of the system. Different application scenarios and working conditions require different types of flanges, making the correct selection crucial for ensuring the safety and performance of the pipeline system.

This article aims to guide you on how to select the appropriate flange type. We will discuss the characteristics and scope of various flange types, as well as key factors to consider when choosing a flange. Additionally, we will explore different materials used for flanges and the importance of adhering to industry standards and regulations. To ensure quality and safety, we will address common flange issues and provide solutions, along with expert advice and tips to help you select the most suitable flange based on specific application requirements.
As a trusted and experienced flange manufacturer, Hebei Yanhao Pipeline Equipment Co., Ltd. is delighted to present this comprehensive guide. Our products are widely used in industries such as oil, chemical, shipbuilding, pharmaceutical, and power generation, earning high praise from our customers. With a commitment to integrity and a focus on quality, we are dedicated to providing our customers with high-quality products and satisfactory services.
Now, let us delve into the process of choosing the right flange type!
1. Understanding Flange Types
There are several types of flanges available in the market, each with its unique features and applications. Let’s explore the most commonly used types:
Weld Neck Flange:

- Features: It has a long tapered neck, which is welded to the pipe, providing high strength and structural integrity.
- Applications: Suitable for high-pressure and high-temperature pipelines, particularly in critical and demanding applications. Commonly used in petrochemical, oil and gas, and power industries.
Slip-On Flange:

- Features: It has a flat face and a bore slightly larger than the outside diameter of the pipe. Easy to align and install.
- Applications: Used in low-pressure, non-critical applications where easy access for cleaning and maintenance is required. Commonly used in water supply systems, fire protection, and general industrial applications.
Socket Weld Flange:

- Features: The pipe is inserted into the socket of the flange, and then fillet-welded for a strong and leak-proof connection.
- Applications: Suitable for small-diameter pipes, high-pressure systems, and systems with heavy vibration or stress. Commonly used in chemical processing, refineries, and power plants.
Blind Flange:
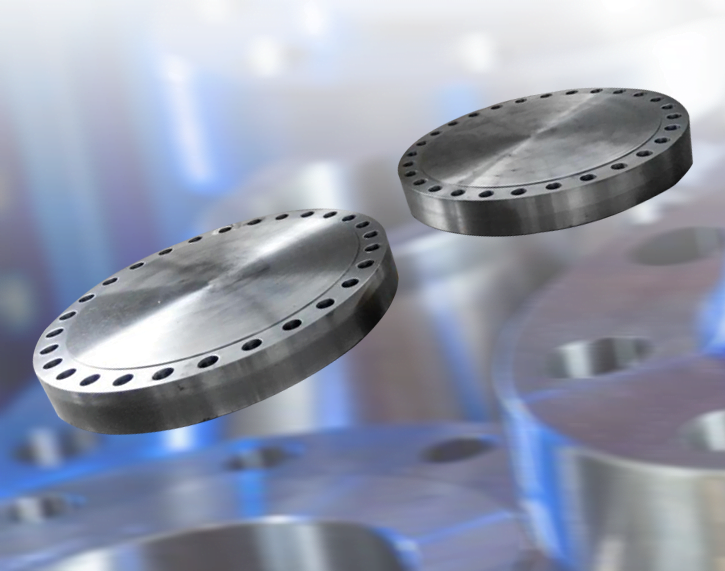
- Features: It is a solid disc with no bore and is used to close the end of a pipe or vessel.
- Applications: Used to terminate pipelines, create access points for inspection or cleaning, and for pressure testing. Commonly used in offshore platforms, petrochemical plants, and water treatment facilities.
Lap Joint Flange:

- Features: It consists of two components – a stub end and a loose backing flange. The stub end is welded to the pipe, and the loose backing flange can rotate freely.
- Applications: Used in systems requiring frequent dismantling and alignment adjustments. Commonly used in piping systems with varying temperatures, expansion, or contraction.
Threaded Flange:

- Features: It has internal threads, allowing it to be screwed onto the pipe, providing a secure connection.
- Applications: Suitable for low-pressure applications, particularly for small-diameter pipes. Commonly used in plumbing systems, gas distribution, and small-scale industries.
It is essential to consider factors such as pressure, temperature, material compatibility, joint tightness, and installation requirements when selecting the appropriate flange type for a specific application. Consulting with industry experts and adhering to relevant standards and regulations is also crucial for ensuring the right flange choice.
2. Factors to Consider
When selecting the right flange type, several key factors should be considered to ensure optimal performance and safety of the pipeline system:
- Pressure Rating: Consider the maximum working pressure of the system. The flange must have a compatible pressure rating to withstand operating conditions and prevent leaks or failures.
- Temperature Range: Determine the minimum and maximum temperatures the flange will be exposed to. Flanges should be selected with materials capable of withstanding the temperature range without deformation or loss of integrity.
- Pipe Size: Flanges should match the diameter of the pipe to ensure a proper fit and alignment. Different flange types may have limitations in terms of compatible pipe sizes, so careful consideration is required.
- Material Compatibility: Ensure the flange material is compatible with the fluid being transported in the pipeline. The flange material should be corrosion-resistant and able to withstand the chemical composition and properties of the fluid.
- Fluid Characteristics: Understand the nature of the fluid, such as its corrosiveness, acidity, abrasiveness, viscosity, and flow characteristics. This information helps in selecting the appropriate flange material and design to prevent corrosion, erosion, or flow-related issues.
Considering these factors is crucial for the optimal performance and safety of the pipeline system. An incorrect flange selection can lead to leaks, failures, and potential hazards, compromising the integrity of the system. Failure to consider pressure ratings, temperature limits, or material compatibility may result in catastrophic consequences, including accidents, spills, or system shutdowns.
It is advisable to consult with experts or refer to industry standards (e.g., ASTM, ASME, API) and regulations to ensure compliance and make informed decisions. Properly assessing these factors during the flange selection process mitigates risks, extends the lifespan of the pipeline system, reduces downtime, and ensures efficient and safe operations.
3. Material Selection
Commonly used materials for flanges include carbon steel, stainless steel, alloy steel, and non-metallic materials. Here’s a detailed overview of each material type:
Carbon Steel:
- Characteristics: Carbon steel flanges offer good strength and durability at a relatively low cost. They have excellent mechanical properties and are widely available in various grades.
- Advantages: Carbon steel flanges are suitable for a wide range of applications and can handle high-pressure and high-temperature conditions. They are also easy to weld and have good machinability.
- Limitations: Carbon steel is prone to corrosion, especially in the presence of moisture, aggressive chemicals, or acidic environments. Proper surface treatment or protective coatings may be required.
Stainless Steel:
- Characteristics: Stainless steel flanges provide excellent corrosion resistance and stability in various environments. They have high strength, good ductility, and low thermal conductivity.
- Advantages: Stainless steel flanges are highly resistant to corrosion, oxidation, and scaling. They can withstand high temperatures and are suitable for applications involving chemicals, acids, and seawater.
- Limitations: Stainless steel flanges are generally more expensive than carbon steel. They may also have reduced impact strength compared to carbon steel.
Alloy Steel:
- Characteristics: Alloy steel flanges are made from various alloying elements, such as chromium, molybdenum, and nickel. They offer enhanced mechanical properties, including higher strength, toughness, and wear resistance.
- Advantages: Alloy steel flanges have superior strength and excellent resistance to corrosion, heat, and wear. They are commonly used in high-pressure and high-temperature applications, such as oil and gas pipelines and power plants.
- Limitations: Alloy steel flanges tend to be more expensive than carbon steel. Welding may require specialized techniques due to the different alloying elements present.
Non-Metallic Materials:
- Characteristics: Non-metallic flange materials include materials like PVC (Polyvinyl Chloride), PTFE (Polytetrafluoroethylene), and rubber.
- Advantages: Non-metallic flanges offer exceptional resistance to corrosion, chemicals, and temperature variations. They are lightweight, cost-effective, and suitable for non-metallic pipe systems or applications that demand electrical insulation.
- Limitations: Non-metallic flanges have lower strength compared to metallic flanges, making them unsuitable for high-pressure or high-temperature applications. They may also have limitations in terms of size and compatibility with certain chemicals or fluids.
The selection of flange material depends on factors such as the specific application, operating conditions, fluid characteristics, and budget. It is crucial to consider the compatibility of the chosen material with the fluid being transported, ensuring it can withstand the temperature, pressure, and chemical exposure of the system. Consulting with materials specialists or referring to industry standards and guidelines is recommended for the appropriate material selection.
4. Flange Standards and Codes
Adhering to industry standards and codes is essential when selecting flanges to ensure the proper functioning, safety, and reliability of the pipeline system. Here’s why it’s important and an overview of some relevant standards:
- Safety and Reliability: Following industry standards and codes helps ensure that flanges meet specific requirements for pressure, temperature, material compatibility, and performance. These standards are developed based on extensive research, testing, and consensus among industry professionals, ensuring the highest level of safety and reliability.
- Compliance and Legal Requirements: Many industries, such as oil and gas, power generation, and chemical processing, have regulatory bodies or government agencies that enforce specific codes and standards for pipeline systems. Compliance with these regulations is necessary to avoid penalties, legal consequences, or loss of certification.
- Interchangeability and Compatibility: Standards such as ASME B16.5 (Pipe Flanges and Flanged Fittings) and ASME B16.47 (Large Diameter Steel Flanges) define the dimensions, tolerances, and ratings for flanges, ensuring that flanges from different manufacturers are interchangeable and compatible. This allows for easy maintenance, repairs, and replacements of flanges without requiring extensive system modifications.
- Performance and Quality Assurance: Industry standards provide guidelines for material selection, manufacturing processes, and testing procedures. Standards like API 6A (Specification for Wellhead and Christmas Tree Equipment) are specifically designed for use in the oil and gas industry and provide requirements for critical flanges used in wellhead and pressure control systems. Adhering to these standards ensures consistent performance, quality assurance, and the ability to meet operational demands and specifications.
- Documentation and Traceability: Industry standards often require documentation and traceability throughout the manufacturing, testing, and installation processes. This includes material certifications, test reports, dimension verification, and traceability to ensure the quality and reliability of the flanges.
- International Consistency: Industry standards also play a crucial role in facilitating international trade and communication. Standards adopted by multiple countries or regions ensure consistency in design, manufacturing, and testing practices, enabling interoperability and seamless integration across different locations or projects.
It is essential to consider and comply with relevant standards when selecting flanges. Some commonly referenced standards include ASME B16.5, which covers flange dimensions, ratings, and materials for pipe flanges and flanged fittings. ASME B16.47 focuses on large-diameter steel flanges, including dimensions, ratings, and testing requirements. API 6A is specific to the oil and gas industry and provides specifications for wellhead and pressure control equipment, including flanges.
Consulting the appropriate standards and codes, and working with knowledgeable professionals or engineers, ensures that flanges are selected and installed correctly, conforming to industry best practices, and meeting regulatory requirements.
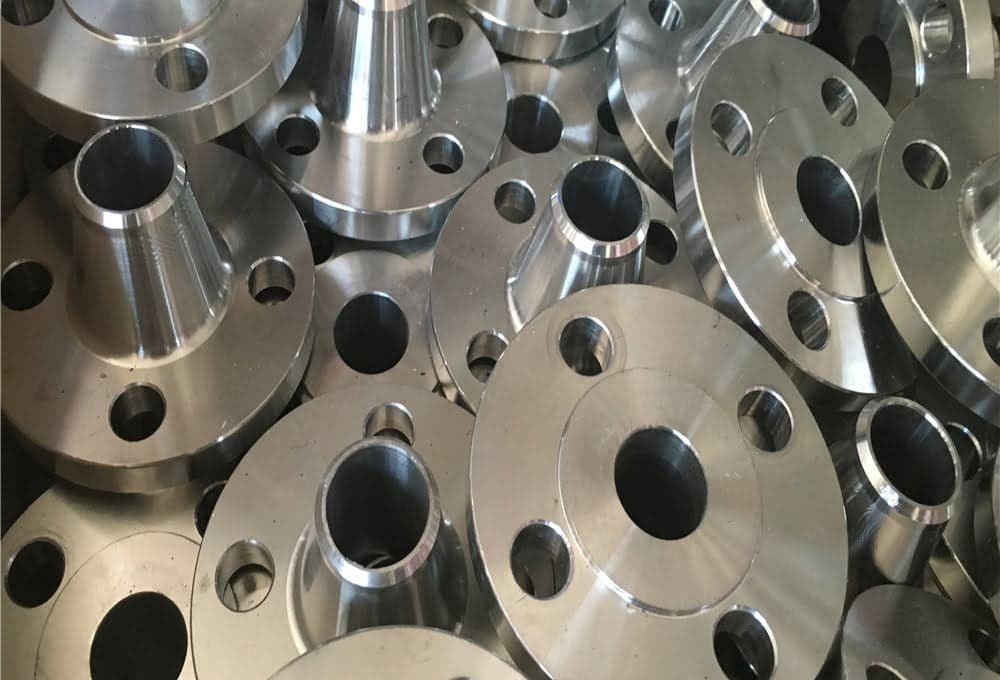
5. Common Flange Issues and Solutions
Leakage:
- Issue: Flange leakage is a common problem caused by improper installation, insufficient bolt tightening, gasket failure, or damage to the flange surface.
- Solution: Ensure proper gasket selection for the specific application, considering factors like temperature, pressure, and chemical compatibility. The flange faces should be clean, flat, and aligned before installation. Use appropriate bolt-tightening procedures, such as torque or tensioning, to achieve the required preload. Regularly inspect flanges for signs of leakage and address any issues promptly.
Corrosion:
- Issue: Corrosion occurs when the flange materials come in contact with corrosive substances or environments, leading to degradation and potential failure.
- Solution: Choose flange materials that are resistant to the specific corrosive conditions present in the system. Consider factors like temperature, pressure, and the chemical composition of the fluid being transported. Apply protective coatings, such as anti-corrosion paints or linings, to the flange surfaces. Implement a regular maintenance program to inspect and mitigate any signs of corrosion, including cleaning, repair, or replacement.
Gasket Failure:
- Issue: Gasket failure can occur due to improper gasket selection, inadequate compression, temperature variations, or chemical attack.
- Solution: Select gaskets that are compatible with the operating conditions, considering factors like temperature, pressure, and fluid type. Use the correct gasket size and shape for the flange. Ensure proper compression of gaskets during installation by following recommended torque or tensioning procedures. Perform regular inspections to identify signs of gasket failure, such as leaks or compression loss, and replace gaskets as needed.
Flange Misalignment:
- Issue: Flange misalignment occurs when mating flanges are not properly aligned, leading to stress concentration, leakage, and potential gasket failure.
- Solution: Ensure proper alignment between flanges during installation by using alignment tools or techniques. Check flange alignment visually or by using a straight edge or feeler gauge. Make necessary adjustments to align the flanges before final tightening. Avoid excessive force or bending of flanges during installation or maintenance.
Bolt Failure:
- Issue: Bolt failure can occur due to inadequate tightening, fatigue, or improper bolt material selection.
- Solution: Follow recommended bolt tightening procedures to achieve the required preload, using torque or tensioning methods. Use high-quality bolts made from materials suitable for the intended application, considering factors like temperature, pressure, and vibration. Regularly inspect bolts for signs of damage or fatigue, and replace any worn or damaged bolts promptly.
Thermal Expansion and Contraction:
- Issue: Thermal expansion and contraction of flanges can lead to stress concentration, bolt loosening, and potential leakage.
- Solution: Consider the thermal expansion properties of the flange materials when designing or selecting the flanges. Allow for proper bolt elongation and provide sufficient flexibility in the piping system to accommodate thermal movements. Use expansion joints or flexible connectors where necessary. Employ proper insulation practices to minimize temperature variations and reduce the impact of thermal cycling.
Regular inspection, maintenance, and adherence to proper installation procedures are vital practices for addressing common flange-related issues. Collaborating with knowledgeable professionals or engineers can provide valuable guidance in selecting the appropriate materials, gaskets, and tightening methods to mitigate potential problems effectively.
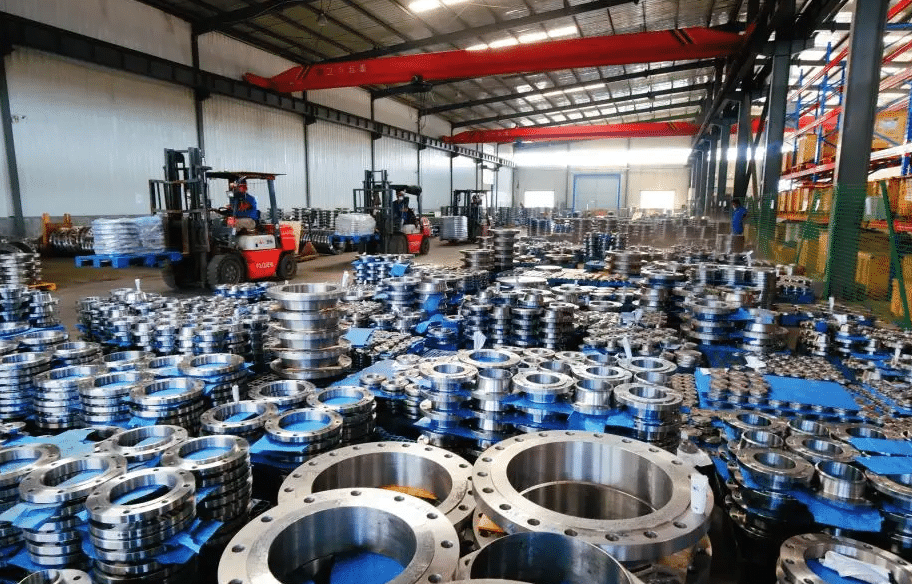
6. Yanhao’s professional tips for flange selection
As a flange manufacturing company, I am honored to offer professional tips and recommendations to help you choose the most suitable type of flange based on specific application requirements. Here are some key factors and advancements that can influence your flange selection decision:
Material Selection:
- Choosing the appropriate material is crucial, considering the specific application environment. Common flange materials include carbon steel, stainless steel, alloy steel, cast iron, etc.
- Determine the temperature, pressure, and chemical properties of the medium involved and select a material with the corresponding corrosion resistance and high-temperature capabilities.
- For special applications like high temperature, low temperature, high pressure, etc., there are constantly evolving new materials and coatings that can offer better performance and durability.
Flange Types:
- Select the most suitable flange type based on application requirements, such as welding neck flange, blind flange, socket weld flange, bolted flange, etc.
- Consider factors such as piping system design, installation, and maintenance requirements, as well as the desired level of connection strength and sealing capability.
Advancements in Sealing Technology:
- Sealing technology plays a vital role in flange performance. Staying updated on the latest advancements in sealing technology can help you make more informed decisions.
- New sealing materials like PTFE, PEEK, leak control technologies certified with API 622 and API 624, etc., can provide better sealing and reliability.
Standards and Certifications:
- Familiarize yourself with relevant standards and certifications like ASME, ISO, API, etc., to ensure that the chosen flanges comply with specifications and requirements.
- Depending on the specific application and regional requirements, be aware of certifications such as the Pressure Equipment Directive (PED) in the EU or the ATEX (Explosive Atmospheres) Directive.
Partner Selection:
- Look for reputable and reliable flange manufacturers or suppliers to collaborate with. They can provide professional advice, customized solutions, and ongoing technical support.
- Maintain regular communication with partners to stay informed about the latest technological advancements and innovations in flange products.
In conclusion, staying updated on the latest advancements in flange technology is essential for making the right flange selection. If you need more professional advice and customized solutions, collaborate closely with your partners or professional engineers.
7. Conclusion
When it comes to choosing the right type of flange, expert guidance is crucial. In this article, we have discussed key factors and the latest advancements in flange technology that can influence your selection.
Firstly, the choice of flange material is paramount as different application environments require specific corrosion resistance and high-temperature capabilities. Factors such as temperature, pressure, and the chemical properties of the medium need to be considered to select the appropriate material.
Secondly, different types of flanges have distinct characteristics and applications. Welding neck flanges are suitable for high-temperature and high-pressure environments, while blind flanges are used to close off pipelines. Understanding the various types of flanges and selecting them based on your specific application requirements is important.
Sealing technology is also a critical factor. Ongoing developments in sealing materials and leak control techniques offer better sealing performance, ensuring the stability and safety of the piping system.
Additionally, familiarity with relevant standards and certifications is crucial. Different countries or regions may have specific requirements, and it is essential to ensure that the chosen flange complies with the appropriate standards and certifications.
Lastly, selecting a reliable partner or supplier is paramount. YANHAO Company, as a professional flange manufacturer, can provide expert guidance and customized solutions to help you make the right choice.
We encourage readers to carefully consider the aforementioned factors and seek assistance from the YANHAO Company when selecting a flange. We will provide professional advice and support to ensure you choose high-quality flanges that meet your specific application needs.
Author: Lewis Liu
Hello, my name is Lewis Liu, and I’m a professional sales engineer with over a decade of expertise in the flange fittings sector.
I am quite informed about flange selection, installation, and maintenance. I am passionate about providing customers with the greatest solutions for keeping their pipeline systems running smoothly, safely, and dependably.
If you have any queries or concerns concerning flange fittings for your pipelines, whether they are about selection, material choice, specification requirements, or anything else, please contact me at any time. I am dedicated to providing expert advice and assistance to help you make educated decisions and reach your objectives.
