How to Install Pipe Flanges: a Step-by-step Guide
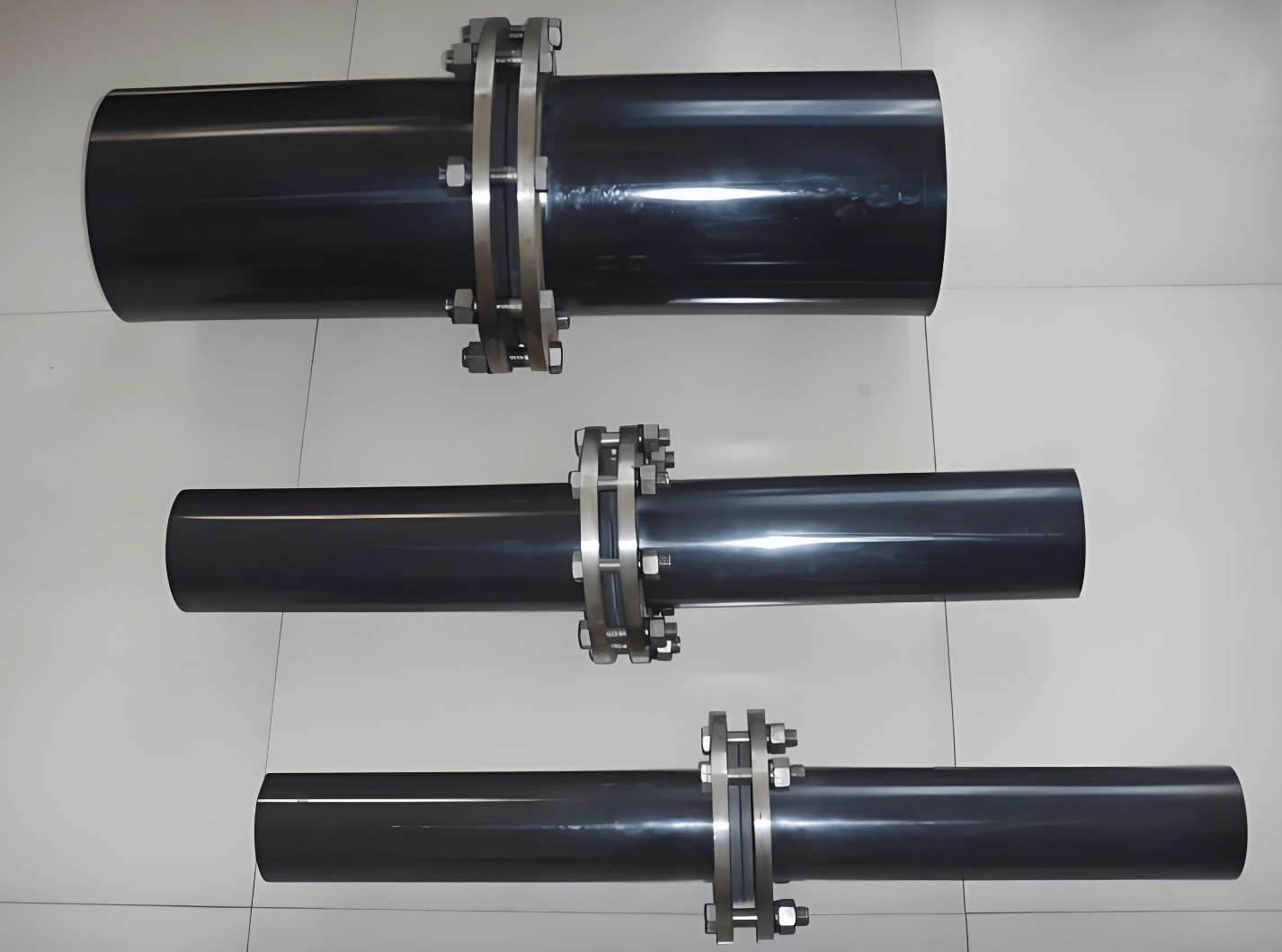
In a piping system, flanges are considered one of the most crucial elements serving as connection points.
By using flanges, the plumbing professionals securely join valves, pipes, regulators, and other components. Chinese flanges not only facilitate safe and secure adjoining but also offer cleaning, inspection, and maintenance of the piping system easily and effectively.
However, all these only become possible when the flanges are installed correctly. Also, appropriate installation is essential as it triggers the required structural integrity preventing leaks. The leak prevention facility also restricts equipment damage, safety-related issues occurrences, and cost repair.
We, Yanhao, intend to elaborate on how to install pipe flanges. This can act as an installation guide for the professionals while highlighting some related and important aspects.
Let’s start.
Introduction to Pipe Flange
In this section, we elaborate on the pipe flange’s definition, purposes, types, and construction materials in a detailed manner.
Definition

As per the basics, a pipe flange is a disk-shaped metal component that accommodates a raised rim, an opening for the pipe, and a multiple number of bolt holes.
With all these structural components, piping flanges offer a reliable and flexible method for joining the piping components.
Structural Components of Pipe Flanges

The following are the structural components of a piping system.
Purposes of Pipe Flange
The core purposes of a pipe flange are listed below.
- First, a pipe flange offers to establish connections like pipe-pipe, pipe-valve, pipe-regulator, and so on.
- Second, pipe flanges offer effortless assembly and disassembly of the piping sections.
- Third, using a flange to develop a piping connection ensures that there is no leaking.
- Furthermore, pipe flanges ensure that the connections do not host any leak offering a greater level of safety for the plumbing workers, other nearby piping equipment, etc. Most essentially, the leak proof connection eliminates the chance of water, air, and soil pollution due to leakages.
- Also, the flanges are designed to withstand high temperature and pressure which makes the flange an essential piping element in various industrial applications.
- By installing pipe flanges, the designers become able to trigger the expansion and shortening of a piping system.
- Due to the associated ease of disassembly, the pipe flanges allow the professionals to perform repair and maintenance jobs more quickly and efficiently.
Types of Pipe Flanges
The following are the most popular types of pipe flanges.
Weld Neck Flange
Weld neck flanges host cast-in neck which is long enough to trigger smooth transition from flange to pipe. Here, the pipes are directly welded to the flange.
Socket Weld Flange
This flange type is small in diameter and used in high-pressure piping applications. In the socket weld flanges, pipes are installed and welded perfectly throughout the outer section.
Blind Flange
The blind flange falls into a specialized category. A blind flange does not consist of any bore for the pipe and is installed at the end of the piping system.
Threaded Flange
This flange criterion also falls into the specialized category. The threaded flanges do not consist of any bolt holes. In this case, screws are used to connect the pipes with the flanges.
Lap Joint Flange
Lap joint flanges are a perfect example of precision engineering developing pipe-flange without any welding or screwing. The lap joint flanges can rotate easily without hampering the structural integrity of the whole piping system. It is usually used if there is a frequent requirement for maintenance and repair works of the piping system.
Orifice Flange
As per the core, an orifice in a piping system is the hole created to insert a pressure gauge or temperature-measuring equipment. The orifice flange is installed at the orifice to ensure there is no leak orientation.
Ring-type Joint Flange
RTJ pipe flanges are used in oil, gas, and chemical industries. This pipe flange type hosts a groove to accommodate a metal gasket.
Slip-on Flange
Slip-on pipe flanges are used in low-pressure applications. This flange type is easy to install and offers greater structural integrity as the flange is welded on the inner sides and outer sides.
Standards Used in Pipe Flanges
Almost every Chinese flange manufacturer in Hebei, China produces flanges that incorporate international standards like ASME/ANSI, DIN, JIS, and customized flanges. Yanhao also does the same and offers flanges with the following standards.
ASME Flanges
ASME/ANSI flanges are designed and produced following ASME/ANSI Section VIII Division 1, ASME/ANSI B16.5, ASME/ANSI B16.47, and so on.
ANSI Flanges
In this case, the flanges are designed and produced following the dimensions of 150, 300, 400, 600, 900, 1500, and 2500. Here, the ANSI flanges NPS ½ to NPS 24.
Din Flanges
The pipe flanges are designed by incorporating the engineering standards of Germany are termed Din flanges.
JIS Flanges
As per the basics, JIS flanges incorporate the engineering standards of Japan. Some examples of JIS standard flanges are JIS 10K for JIS B 2220/2239-2006, JIS 20K for JIS B 2220/2239-2006, etc.
Non-standard Flanges
This flange type is also termed a customized flange type. If a piping system is unique and does not follow any of the standards mentioned earlier, professionals use non-standard flanges. Yanhao is an expert in producing any form of customized flanges.
Pipe Flange Construction Materials
Well, the mentioned standards in the above section are designated to incorporate the dimension, stress tolerance, etc. On the other hand, the pipe flange’s construction material selection follows the standard of ASTM. Designers and professionals at Yanhao can effectively incorporate the ASTM standards while proposing other suitable and compatible materials for flange construction.
Stainless Steel Flanges
For industrial applications, stainless steel pipe flanges are the most essential ones. This flange type is highly resistant to corrosion and stains. SS flange production process follows the ASTM A182 F304 and F316 guidelines.
Carbon Steel Flanges
Carbon steel flanges are popular due to their associated strength and affordability. In this case, Yanhao uses ASTM grade A105N for forged carbon steel flanges and ASTM grade A350 LF2 for low-temperature carbon steel. Yanhao is also an expert in incorporating other ASTM flange grades like ASTM A182, ASTM A694, etc.
Alloy Steel Flanges
Alloy steel flanges are used in high-pressure and high-temperature applications. Due to the presence of chromium, molybdenum, and nickel in alloy steel, the respective flanges offer greater mechanical properties and corrosion resistance. Alloy steel pipe flanges incorporate ASTM grade A182 F5, F9, F11, etc.
Nickel Alloy Flanges
Nickel alloy pipe flanges are used in sophisticated mechanical and electrical engineering applications. This pipe flange type incorporates ASTM grade B564, SB564, UNS N02200, and so on.
Copper Alloy Pipe Flanges
Copper alloy pipe flanges also serve similar purposes to Nickel alloy pipe flanges. In this case, the most used ASTM codes are ASTM B61 and ASTM B62.
Iron-made Pipe Flanges
In most cases, cast and ductile irons are used to manufacture iron-made pipe flanges. Yanhao incorporates ASTM A126 and A536 from cast and ductile iron, respectively.
A Comprehensive Guide on How to Install Pipe Flanges
This section is designated to detail the pipe flange installation process. Here, experts at Yanhao elaborate on the various segments of the pipe flange installation process including the pre-installation process to the installation completion process.
Pre-installation Processes
Plumbing professionals must embrace the following stepwise guide before initiating the installation process.
Meeting PPE Requirements
The pipe flange installation process requires various tools and materials. Here, pipe flange installation professionals must incorporate the standard PPE requirements. Adhering to the PPE standards ensures that the workers can effectively and safely handle potential hazards like harsh chemical exposure, sharp-edged materials, heavy-weight mechanical components, electric cables, etc. In this case, the general PPE requirement is to wear the below-listed safety measures:
Inspecting Flanges and Materials
As part of the pre-installation process of the pipe flanges, the professionals must inspect flanges and other to-be-installed materials to ensure the flange’s high performance and structural integrity of the whole piping system. The flange and associated material inspection process includes the below-listed components.
- Professionals need to do a close examination of the flanges to find cracks, warps, damage, and any corroded spots. It is also essential to do a physical check of the dimension-related specifications of the flanges by incorporating the design sheets.
- Other flange installation components like washers, nuts, and bolts are required to be checked. It triggers the exclusion of any degraded-quality component.
- Most importantly, the plumbing professionals must do a quality check of the supplied gaskets. If there is any sign of crack, wear, tear, corrosion, etc., the respective gasket must be replaced. It is more than essential as the gaskets ensure tight sealing at the connection points which facilitates zero-leaking.
- Along with the above mentions, the plumbing professionals must check the welding rods’ quality and the welding machine’s performance. If any welding joint is proposed, this task is more than essential considering the weld-based joint’s crucial role in the whole piping structure’s integrity. However, if screw joint flanges or lap joint flanges are going to be used, inspection of the screws for the screw joint and precision of the lap joint flange dimensions is essential.
Cleaning of the Flanges and Other Installation Materials
Before starting the main installation process, it is required that the professionals incorporate the following pre-installation measures.
- By using a wired brush, the flanges, and other materials need to be cleaned to remove dust and debris. If the to-be-installed components carry a considerable number of debris, the professionals must use compatible solvents to ensure perfect cleaning.
- Cleaning both faces of a flange is essential along with the end portion of the pipe. For a perfect job, professionals must bevel the welding points on the pipe end and the flange bore’s surface. After beveling with a grinder machine, the mentioned portions need to be cleaned with sandpaper.
- In all two cleaning cases, it is required that the professionals use compatible flange materials to avoid any dust or debris present on the surfaces. Also, the compatibility checkup ensures that the flange and other respective installation materials do not face any damaging context.
Completing Pre-installation Process
To get a high-quality output, professionals must use working tables equipped with clamps, welding rod holders, 180-degree plain top surface, and so on. Here, using a metalworking table properly fixed with the floor surface is the standard.
Positioning and Aligning
To ensure effective joints between flanges and pipes, at first, the pipes need to be placed appropriately. In this case, the professionals must place the respective pipe on the working table or platform (for larger flange works) with perfect alignment. If the flanges are going to be used as part of the piping system’s expansion, plumbing professionals are required to use heavy-duty sprit levels to ensure the required alignment’s orientation. Here, the professionals must place stone chips or flexible metal stands below the piping to hit the alignment target.
Installation of the Pipe Flanges
The following is the step-by-step guide to doing the pipe flange installation. Here, we elaborate on how to form flange-flange and flange-pipe joints.
Step 1: Positioning the Flanges
Upon completion of the pre-installation process, the plumbing workers are required to position the respective flange on the working table or platform. Here, the standard is using two spirit levels ensuring that the flange is positioned accurately: one level on top of the flange and the second level on top of the pipe surface. The flange positioning process completion requires hitting the 0 scale by both levels.
If the connection process requires joining two flanges or one flange with other components like a valve, regulator, etc., both of the items are required to hit the 0 scale on the levels. Also, the following tasks are included in joining two flanges.
- Placing the gasket appropriately so that the gasket matches the exact dimension of the flange’s face at the joining position. This requires aligning the flange’s center with the gasket’s center to ensure the covering of the flange surface by the gasket surface.
- The perfect alignment of the gasket and both of the flanges is a crucial requirement. This ensures tight sealing which restricts any sort of leaking.
- Then, bolts are required to be installed to form a perfect joint. In this case, hand tightening of the bolts is needed. After ensuring the alignments are perfect, the bolts should be fixed using a torque range. The workers must not insert torques more than the design allows. Over-tightening of the bolts can damage the flange and gasket.
Step 2: Joining Flanges with Pipes
To form welding joints between the flanges and pipes, the following tasks’ completion is required.
- Make sure that the welding machine is supplying the required level of voltages to melt the weld rods perfectly. The pass-through of the voltage in the welding machine must be consistent.
- Upon the readiness of the welding machine, the already checked weld rods need to be installed on the weld rod holder of the welding machine.
- Now, it is time to start the joining of the flange and pipe. A highly skilled and experienced workforce is required to develop perfect and fine-finish welding joints. In the welding process, easy joints are needed to be formed at a single shot; it is the standard requirement. However, sometimes on-shot welding joint formation is tough which demands close inspection of the joints and fill the welding gaps as required.
- A metal chipper is required to chip off the weld joint’s on-top surface. Upon chipping the burned components of the weld joints will be removed.
- Finally, by using sandpaper, the joints need to be cleaned from the dust and debris. Then, cross-examination of the weld joint quality takes place ensuring the respective flange and pipe are joined appropriately. Also, a final alignment check is needed.
Flange Installation Completion
To finish the flange installation in terms of flange-flange or flange-pipe joints, the implementation of a standard testing method is required. In general, depending on the application type, professionals are used to implementing hydrostatic tests, air pressure tests, and helium leak tests. Performance of these tests or a single test based on the application’s criterion ensures that the joints are high-performing and 100 percent leak-proof. The final step of the flange installation process also includes visual inspection for the gaps and final alignment testing. Upon any dissatisfactory outcome’s observance, the whole assembly is needed to extract and perform the reassemble task following the steps as the first joint formation’s time.
Tips to Increase the Flange Joint’s Performance and Durability
The following are the maintenance and repair-related tips to ensure enhanced performance and durability of the installed flange and the joints.
- For flange-flange joints, professionals must check the bolts’ tightening condition after 8-12 months of use of the whole system.
- Gasket inspection should take place at least once a year.
- Welded joint condition inspection should be performed once a year.
If any of the below-listed happening is observed, the professionals must go for repair or replacement work.
- Rust, discoloration, and pitting on the flange and bolt surface.
- If the flowing substance is leaking, the bolts are required to tighten again. Also, it is better to replace the old gasket with a new one.
- If there is any rattling sound at the joints or any visual movement, prompt repair or replacement work is essential.
- Gasket deformation, cracks, etc. must be addressed by replacing the damaged gasket.
- Any sort of visible crack, warp, or bending demands prompt replacement of the respective flange.
Final Words
We expect that our elaboration on how to install the flange will help the professionals enormously. By using the stepwise guides, professionals will be able to form highly functional flange-flange, flange-valve, flange-regulator, flange-pipe, etc. joints effectively. We highly recommend using quality welding rods, sandpapers, welding machines, etc. to ensure the whole system’s durability and functionality.
However, Yanhao produces high-quality pipe flanges that offer greater durability and superb functionality. Also, the top-notch flange quality provided by Yanhao eliminates the reworking tasks in the connection development process.
Author: Lewis Liu
Hello, my name is Lewis Liu, and I’m a professional sales engineer with over a decade of expertise in the flange fittings sector.
I am quite informed about flange selection, installation, and maintenance. I am passionate about providing customers with the greatest solutions for keeping their pipeline systems running smoothly, safely, and dependably.
If you have any queries or concerns concerning flange fittings for your pipelines, whether they are about selection, material choice, specification requirements, or anything else, please contact me at any time. I am dedicated to providing expert advice and assistance to help you make educated decisions and reach your objectives.
