5 Tips for Choosing the Right Pipe Flanges for Your Project
Pipe flanges are an integral part of many engineering projects, connecting pipes and components together to create a complete system. Choosing the right pipe flanges for a project is crucial to ensuring proper functionality and avoiding costly mistakes. With so many types and materials of pipe flanges available, it can be overwhelming to determine which ones to use. In this blog post, we’ll provide you with five tips to help you choose the right pipe flanges for your project. We’ll cover everything from project requirements to flange standards, providing you with the knowledge you need to make informed decisions.

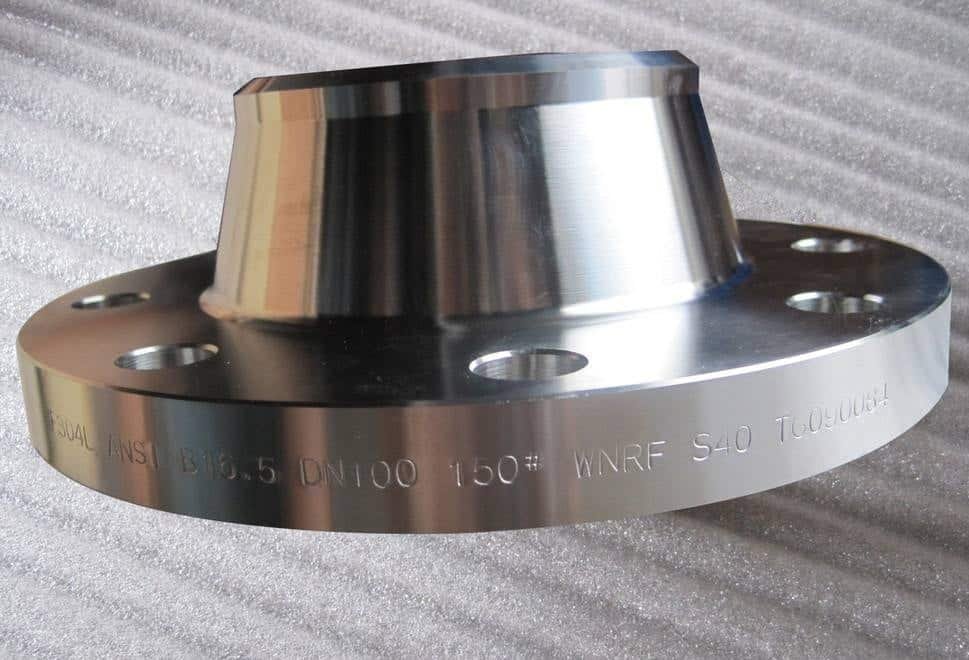

I. Introduction
Pipe flanges are specialized fittings that are used to connect pipes or equipment together. They are designed to join pipes or equipment of different sizes, shapes, or materials in a secure and leak-proof manner. Flanges are used extensively in various industries, including oil and gas, chemical, and power generation.
Choosing the right pipe flanges for a project is crucial to ensure proper functioning and safety. The wrong flange can lead to leaks, system failure, and even accidents. For instance, using a flange that is not designed to handle the pressure, temperature, or medium of the system can result in catastrophic failure. Similarly, using an incompatible material or type of flange can cause corrosion, erosion, or galvanic corrosion, leading to premature failure of the system.
Therefore, selecting the right pipe flanges based on the project’s specific requirements is critical to ensure the safety, reliability, and longevity of the system. By considering the factors such as pressure, temperature, medium, pipe size, material, and flange type, you can choose the appropriate flange that meets the system’s demands and enhances its performance.
This blog post provides five essential tips for choosing the right pipe flanges for your project. The post will cover determining project requirements, selecting the right flange material and type, considering the connection method, and understanding flange standards. By following these tips, readers will be able to make informed decisions when selecting pipe flanges, ensuring safe and reliable system performance.
II. Determine Project Requirements
Identify the required pressure rating, temperature, medium, pipe size, and type for the project.
When selecting pipe flanges, it is important to start by determining the project requirements. This involves considering various factors such as the required pressure rating, temperature, medium, pipe size, and type.
The pressure rating refers to the maximum pressure that the system will operate at, and the flanges must be rated to handle this pressure. Similarly, the temperature rating refers to the maximum temperature that the system will operate at, and the flanges must be able to handle the temperature without failing.
The medium refers to the substance that will be transported through the system, such as gas, oil, water, or chemicals. The chemical composition and properties of the medium can impact the corrosion resistance and material compatibility of the flanges.
The pipe size and type refer to the diameter and shape of the pipes that the flanges will connect. The flanges must be compatible with the pipe size and type to ensure a proper fit and secure connection.
By considering these project requirements, you can select the appropriate pipe flanges that meet the demands of the system, ensuring safe and efficient operation.
why these factors are important
Pressure rating and temperature: Choosing the wrong flange with a lower pressure rating or temperature rating than required can result in system failure, leaks, and accidents. It is essential to select flanges that can handle the maximum pressure and temperature that the system will operate.
Medium: Different substances have different chemical compositions and properties that can impact the material compatibility and corrosion resistance of the flanges. Choosing a flange material that is not compatible with the medium can cause premature failure of the system.
Pipe size and type: Flanges must fit properly and securely connect the pipes of the system. Choosing the wrong size or type of flange can result in an improper fit, leaks, and reduced efficiency.
III. Determine Flange Material
common flange materials
Carbon steel: This is the most common material for pipe flanges and is suitable for low to medium-pressure and temperature applications. It is also cost-effective and widely available.
Stainless steel: This material is ideal for corrosive or high-temperature applications, as it provides excellent corrosion resistance and durability.
Alloy steel: This material has higher strength and temperature resistance than carbon steel and is suitable for high-pressure and high-temperature applications.
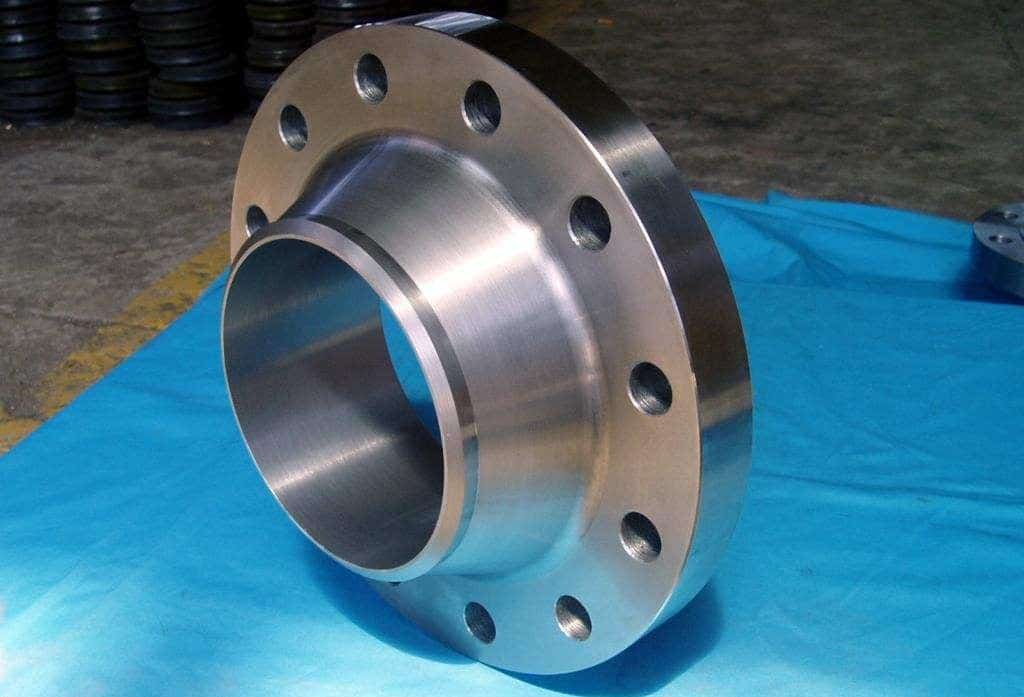

Application places of different pipe flange materials
Carbon steel flange: This material is widely used for low to medium-pressure and temperature applications. It is cost-effective and has good strength and durability. However, it may not be suitable for highly corrosive environments.
Stainless steel flange: Stainless steel provides excellent corrosion resistance and durability, making it ideal for corrosive or high-temperature applications. It is also easy to clean and maintain. However, it is more expensive than carbon steel.
Alloy steel flange: This material has higher strength and temperature resistance than carbon steel, making it suitable for high-pressure and high-temperature applications. However, it is more expensive than carbon steel.
IV.Determine Flange Type

Weld Neck Flange: This type of flange is suitable for high-pressure and high-temperature applications, especially those involving cyclic loading and thermal stresses. It is commonly used in the petrochemical, oil, gas, and power generation industries.
Slip-On Flange: This type of flange is suitable for low-pressure and low-temperature applications, where quick installation and removal are required. It is commonly used in water supply, plumbing, and HVAC systems.
Socket Weld Flange: This type of flange is similar to a slip-on flange, but is more suitable for high-pressure and high-temperature applications. It provides a strong and reliable connection that resists deformation and leakage. It is commonly used in chemical processing, power generation, and oil and gas industries.
Blind Flange: This type of flange is suitable for applications where the end of a pipe or valve needs to be sealed. It is commonly used in pipelines and pressure vessels, as well as in hydraulic and pneumatic systems.
Threaded Flange: This type of flange is suitable for low-pressure and low-temperature applications, where easy installation and removal are required. It is commonly used in plumbing, water supply, and air conditioning systems.
Lap Joint Flange: This type of flange is suitable for applications where frequent disassembly and reassembly are required. It is commonly used in piping systems that require periodic inspection or maintenance.
V.Common flange connection methods and selection skills
Flanges can be connected to pipes using several methods, including:
Welding: Flanges can be welded directly to the pipe, providing a strong and permanent connection. Welding is commonly used for high-pressure and high-temperature applications, where a secure and reliable connection is required.
Bolting: Flanges can be bolted to the pipe using nuts and bolts, providing a strong and flexible connection. Bolting is commonly used for low to medium-pressure applications, where some flexibility in the connection is desirable.
Clamping: Flanges can be clamped to the pipe using special clamps or couplings, providing a quick and easy connection. Clamping is commonly used for emergency repairs or temporary connections.
Adhesive bonding: Flanges can be bonded to the pipe using adhesive bonding agents, providing a strong and flexible connection. Adhesive bonding is commonly used for low-pressure applications, where some flexibility in the connection is desirable.
The choice of flange connection method depends on the specific project requirements and application. Welding is suitable for high-pressure and high-temperature applications, while bolting is suitable for low to medium-pressure applications. Clamping is ideal for emergency repairs or temporary connections, while adhesive bonding is suitable for low-pressure applications where flexibility in the connection is desirable.
VI. Understand Flange Standards
Here’s a brief introduction to some common flange standards:
ANSI/ASME: This is a widely used flange standard in the United States. It includes a range of flange types, such as weld neck, slip-on, threaded, and blind flanges. ANSI/ASME flanges are typically made from carbon or stainless steel and are rated for a range of pressure classes.
API: This standard is used in the oil and gas industry and includes a range of flange types that are suitable for high-pressure applications. API flanges are typically made from carbon or alloy steel and are rated for a range of pressure classes.
DIN: This is a German standard for flanges that is widely used in Europe. It includes a range of flange types, such as weld neck, slip-on, threaded, and blind flanges. DIN flanges are typically made from carbon or stainless steel and are rated for a range of pressure classes.
JIS: This is a Japanese standard for flanges that is commonly used in Asia. It includes a range of flange types, such as weld neck, slip-on, threaded, and blind flanges. JIS flanges are typically made from carbon or stainless steel and are rated for a range of pressure classes.
BS: This is a British standard for flanges that are widely used in the UK and other parts of the world. It includes a range of flange types, such as weld neck, slip-on, threaded, and blind flanges. BS flanges are typically made from carbon or stainless steel and are rated for a range of pressure classes.
Each of these standards specifies different dimensions, materials, and pressure ratings for flanges. When selecting a flange, it is important to choose one that meets the relevant standard for your application.
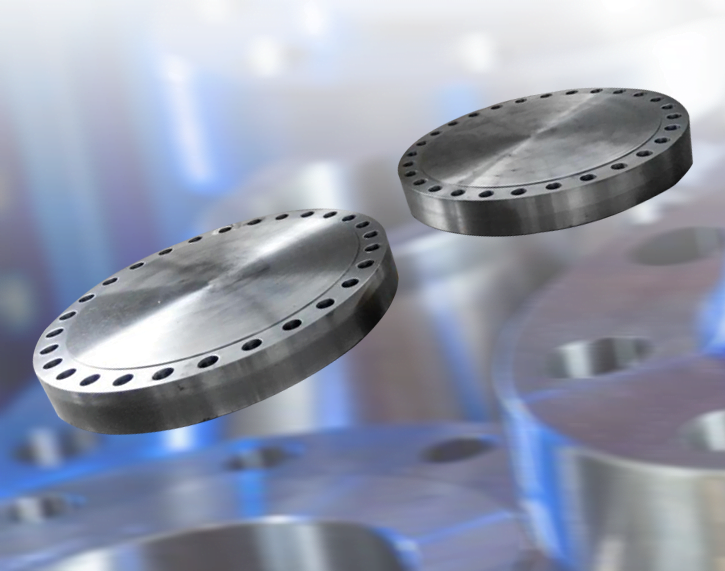


Adhering to applicable flange standards is important
Safety: Flanges are used to connect pipes that carry fluids or gases under high pressure. Using the wrong type of flange or one that does not meet the necessary safety standards can result in leaks, failures, or other hazards that can cause injuries or property damage.
Compatibility: Flange standards specify dimensions and materials for each type of flange, ensuring that they are compatible with other components in the system. Using non-standard or incompatible flanges can result in leaks, corrosion, or other problems that can compromise the system’s efficiency and longevity.
Compliance: Many industries have regulations and standards that govern the use of flanges and other components in piping systems. Adhering to these standards can help ensure compliance with legal requirements, avoid fines or penalties, and promote ethical and responsible business practices.
Reliability: Flanges are critical components in piping systems that must withstand high pressures, temperatures, and other stressors. Using flanges that meet or exceed industry standards can help ensure that they perform reliably and consistently over time, reducing the risk of downtime, maintenance, or other disruptions that can affect productivity and profitability.
Overall, adhering to applicable flange standards is important for ensuring safety, compatibility, compliance, and reliability in piping systems.
VII. Conclusion
we provide guidance for selecting the appropriate flanges for piping systems. This blog emphasizes the importance of understanding project requirements, selecting the right material, choosing the appropriate flange type, following flange standards, and consulting with experts when needed. By following these tips, project managers and engineers can choose the right flanges for their piping systems, ensuring safety, reliability, and efficiency.
Choosing the right pipe flanges is crucial for the success of any piping project. The wrong flange can lead to leaks, structural failures, and safety hazards. Selecting the right flanges based on project requirements, material compatibility, and applicable standards can ensure the safe and reliable operation of the piping system. It can also prevent costly repairs and downtime caused by unexpected failures. Therefore, it is essential to prioritize the selection of the appropriate flanges and to consult with experts when necessary to ensure the success of the project.
Author: Lewis Liu
Hello, my name is Lewis Liu, and I’m a professional sales engineer with over a decade of expertise in the flange fittings sector.
I am quite informed about flange selection, installation, and maintenance. I am passionate about providing customers with the greatest solutions for keeping their pipeline systems running smoothly, safely, and dependably.
If you have any queries or concerns concerning flange fittings for your pipelines, whether they are about selection, material choice, specification requirements, or anything else, please contact me at any time. I am dedicated to providing expert advice and assistance to help you make educated decisions and reach your objectives.
