What are the types of stainless steel carbon steel flanges?
Stainless steel flanges, with their diverse types and applications, form the backbone of critical infrastructure worldwide. From the towering structures of urban landscapes to the intricate pipelines beneath our feet, these unassuming components play a crucial role in ensuring the integrity and efficiency of fluid systems.
In this comprehensive guide, we aim to shed light on the various types of stainless steel flanges, dissecting their designs, applications, and advantages. Through this exploration, we invite you to witness the marriage of innovation and tradition in the production of these essential components.
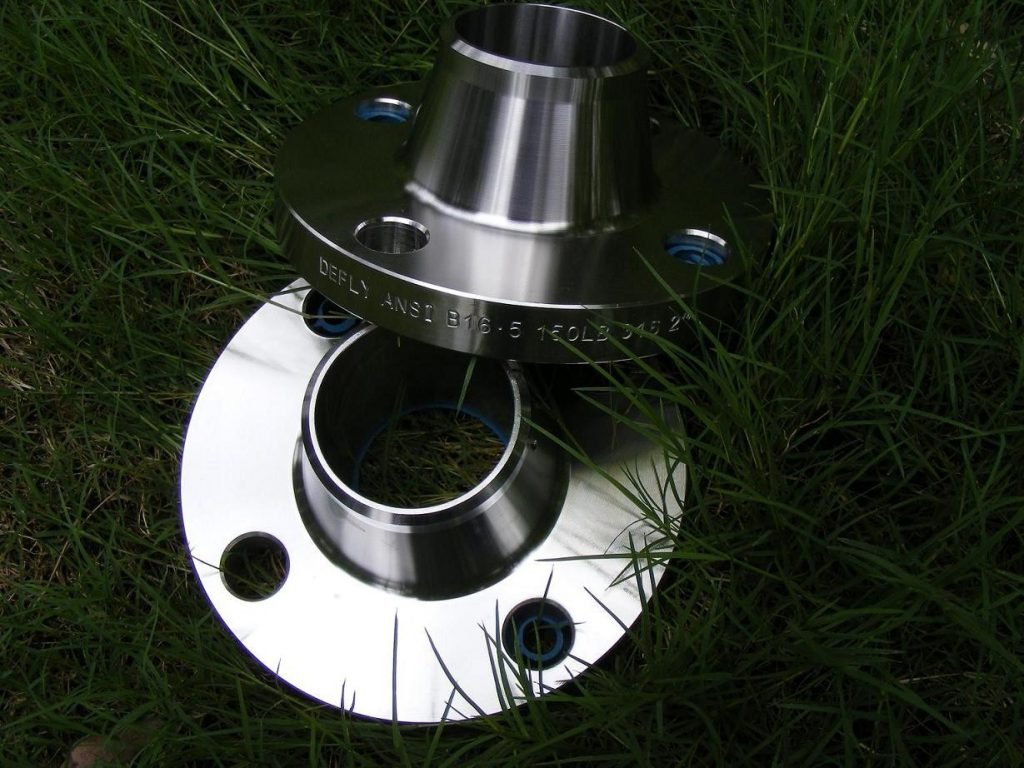
1. Weld Neck Flanges:
Design:
Weld neck flanges, distinguished by their extended neck or hub, feature a smooth, gradual transition from the flange to the pipe. This design incorporates a tapered hub that facilitates the welding process and enhances the overall strength and integrity of the joint.
The key elements of the design include:
- Neck Length: The length of the neck is a critical design feature, providing space for a smooth weld connection and ensuring efficient stress distribution. Longer necks are often preferred for applications demanding higher pressure and temperature tolerances.
- Tapered Hub: The tapered hub not only aids in welding but also contributes to the overall stability of the joint. This design minimizes stress concentrations, making weld neck flanges suitable for demanding industrial environments.
Features:
Weld neck flanges are characterized by several features that make them suitable for specific applications:
- High Pressure and Temperature Resistance: The extended neck and tapered hub design make weld neck flanges robust and capable of withstanding high-pressure and high-temperature conditions. They are commonly employed in critical applications where structural integrity is paramount.
- Smooth Flow Transition: The smooth transition from the flange to the pipe minimizes turbulence and pressure drop, ensuring an efficient and uninterrupted flow of fluids. This is particularly advantageous in industries such as oil and gas.
- Prevents Leakage: The welding neck flange design, when properly welded, creates a strong and leak-resistant joint. This is essential in applications where any form of leakage could have severe consequences, such as in chemical processing plants.
- Weldability: Weld neck flanges are specifically designed to facilitate welding, providing a secure and durable connection between the flange and the pipe. The welding process creates a permanent bond, enhancing the reliability of the entire system.
Applications:
Critical in industries like oil and gas, chemical processing, and power generation where robustness and reliability are paramount.
In conclusion, weld neck flanges are a testament to precision engineering, offering a design that prioritizes strength, reliability, and fluid dynamics. Yanhao’s commitment to excellence ensures that weld neck flanges produced by our company adhere to the highest industry standards, making them a trusted choice for critical applications across various industries.
2. Slip-On Flanges:
Design:
Slip-on flanges are characterized by their simple yet effective design, making them versatile components in various piping systems. The key design elements of slip-on flanges contribute to their ease of installation and suitability for specific applications.
- Bore Diameter:
- Slip-on flanges have a bore diameter slightly larger than the outer diameter of the pipe they connect to. This allows the flange to slip over the pipe, providing a straightforward and quick installation process.
- Raised Face:
- The flange face is typically raised, offering a flat sealing surface. This design simplifies the alignment of the flange during installation and contributes to the ease of sealing.
- Welding Hub:
- Slip-on flanges have a welding hub on the inner side, allowing for secure welding of the flange to the pipe. The welding process creates a strong and durable connection.
Features:
The design features of slip-on flanges make them well-suited for specific applications where ease of assembly and disassembly is crucial. Here are the key features:
- Ease of Installation:
- Slip-on flanges are known for their simplicity and ease of installation. The slip-over design eliminates the need for precise alignment during setup, making them a preferred choice in situations where quick assembly is essential.
- Cost-Effective:
- The simplicity of the slip-on flange design translates to cost-effectiveness in terms of both manufacturing and installation. The reduced complexity makes them an economical choice for low-pressure applications.
- Ideal for Low-Pressure Systems:
- Due to their design, slip-on flanges are best suited for low-pressure applications. Their simple structure may not be suitable for handling the high pressures that other flange types, such as weld neck flanges, are designed for.
- Facilitates Easy Inspection:
- The slip-on design allows for easy inspection of the joint between the flange and the pipe. This is advantageous in applications where periodic inspection or maintenance is required.
- Versatility in Materials:
- Slip-on flanges can be manufactured from a variety of materials, offering versatility in their applications. Common materials include carbon steel, stainless steel, and alloy steel, allowing for customization based on the specific requirements of the system.
Applications:
Preferred in industries such as water treatment, food processing, and HVAC systems where ease of assembly and disassembly is crucial.
In conclusion, slip-on flanges are valued for their simplicity, ease of installation, and cost-effectiveness. Yanhao ensures that slip-on flanges produced adhere to the highest standards, providing reliable and efficient solutions for a range of low-pressure applications across different industries.
3. Socket Weld Flanges:
Design:
Socket weld flanges are recognized for their unique design, characterized by a recessed area or socket into which the end of the pipe is inserted and welded. This design enhances the strength and structural integrity of the joint, making socket weld flanges suitable for high-pressure applications. Key design elements include:
- Socket (Recessed Area):
- The socket is a key feature of socket weld flanges. It provides a recessed area into which the end of the pipe is inserted, creating a smooth and continuous bore.
- Counterbore:
- Socket weld flanges often have a counterbore at the base of the socket. This counterbore accommodates the pipe and allows for proper welding, ensuring a secure and leak-free connection.
- Welding Fillet:
- The welding fillet is formed as the pipe is welded to the socket. This fillet enhances the strength of the joint and contributes to the overall stability of the connection.
Features:
The design features of socket weld flanges make them well-suited for applications where a robust, leak-resistant, and high-pressure connection is essential. Here are the key features:
- High Pressure and Temperature Resistance:
- Socket weld flanges are designed to handle high-pressure and high-temperature conditions. The welded connection provides strength, and the smooth bore reduces turbulence, making them suitable for critical applications in industries such as chemical processing and petrochemical.
- Strong and Reliable Connection:
- The socket weld design creates a strong and reliable connection between the pipe and the flange. This is particularly crucial in applications where the integrity of the system is paramount.
- Smooth Flow Transition:
- The smooth transition from the pipe to the flange minimizes turbulence and pressure drop, ensuring an efficient and uninterrupted flow of fluids. This feature is advantageous in applications where a smooth flow is essential.
- Precision Welding:
- Socket weld flanges require precision welding, and the welding process results in a fillet that adds to the overall strength of the joint. The precision welding ensures a secure and durable connection.
- Suitable for Critical Environments:
- Socket weld flanges are commonly used in critical environments such as chemical processing and oil and gas, where leak resistance and structural integrity are paramount.
- Reduced External Loads:
- The design of socket weld flanges reduces the external loads on the pipe compared to some other flange types. This can be advantageous in applications where minimizing stress on the piping system is a consideration.
Applications:
Frequently used in chemical processing, petrochemical, and pharmaceutical industries where high-pressure conditions are prevalent.
In conclusion, socket weld flanges are engineered for applications demanding a combination of strength, reliability, and resistance to high-pressure and high-temperature conditions. Yanhao’s commitment to precision and quality ensures that socket weld flanges produced by our company meet the stringent requirements of diverse industrial applications.
4. Threaded Flanges:
Threaded Flanges: Design and Features
Design:
Threaded flanges are distinctive in their design, featuring internal threads that facilitate a secure connection with external threads on the pipe. This threaded connection eliminates the need for welding and provides ease of assembly and disassembly. Key design elements include:
- Internal Threads:
- Threaded flanges have internal threads machined into their bore, allowing them to be screwed onto the external threads of the pipe. This threading provides a secure and leak-resistant connection.
- Raised Face or Flat Face:
- Threaded flanges may have a raised face or flat face, depending on the application. The raised face provides additional support and ensures proper alignment during assembly.
- Bore Diameter:
- The bore diameter of threaded flanges is designed to match the outer diameter of the pipe, allowing for a seamless connection.
- Counterbore:
- Some threaded flanges feature a counterbore, providing space for the pipe end and contributing to the overall strength of the connection.
Features:
Threaded flanges are chosen for their simplicity, ease of installation, and suitability for specific applications. Here are the key features:
- Ease of Assembly and Disassembly:
- The threaded connection eliminates the need for welding, making threaded flanges easy to assemble and disassemble. This feature is advantageous in applications requiring frequent maintenance or alterations.
- Versatility in Materials:
- Threaded flanges can be manufactured from various materials, including carbon steel, stainless steel, and alloy steel. This versatility allows them to cater to a wide range of applications in different industries.
- Suitable for Low-Pressure Systems:
- Threaded flanges are well-suited for low-pressure systems. While they may not be suitable for applications with extremely high pressures, they provide a reliable solution for systems operating under moderate pressure conditions.
- Convenient for Temporary Connections:
- Threaded flanges are convenient for temporary connections or situations where the flange needs to be easily removed. This feature is particularly useful in industries such as plumbing.
- No Welding Required:
- The absence of welding simplifies the installation process and eliminates the need for skilled welders. This can be advantageous in scenarios where welding is not practical or cost-effective.
- Resistance to Vibration:
- The threaded connection provides resistance to vibration and mechanical shocks, making threaded flanges suitable for applications where the system may experience movement or stress.
Applications:
Commonly found in plumbing systems, low-pressure pipelines, and applications requiring regular maintenance.
In summary, threaded flanges offer a practical and efficient solution for specific applications, particularly in low-pressure systems or situations where ease of assembly and disassembly is crucial. Yanhao ensures that threaded flanges produced meet industry standards, providing reliable solutions for various piping requirements.
5. Blind Flanges:
Blind Flanges: Design and Features
Design:
Blind flanges are designed to close the end of a pipe, vessel, or valve. They are solid plates without a bore, making them distinct from other types of flanges. The design is tailored to effectively seal the termination point of a piping system. Key design elements include:
- Solid Plate Construction:
- Blind flanges are solid and lack a bore, serving the primary purpose of sealing the end of a pipe. This design ensures a complete closure of the system.
- Raised Face or Flat Face:
- Blind flanges may have a raised face or flat face, depending on the specific application requirements. A raised face enhances stability and provides a surface for better alignment during installation.
- Bolt Holes:
- Blind flanges typically have bolt holes around the periphery, allowing them to be securely fastened to the mating flange or equipment.
Features:
Blind flanges offer distinctive features that make them essential in various industrial applications where closing the end of a pipe or vessel is necessary. Here are the key features:
- Closure of Open Ends:
- The primary function of blind flanges is to close open ends of pipes, valves, or vessels. This is crucial in situations where certain sections of a piping system need to be sealed off temporarily or permanently.
- Isolation and Inspection:
- Blind flanges are utilized for isolating sections of a piping system for maintenance, inspection, or repair. They provide a secure closure, allowing workers to perform tasks without interference from the flowing fluids.
- Pressure Testing:
- Blind flanges are often used in pressure testing procedures. By closing off one end of a system, pressure tests can be conducted to ensure the integrity of the entire piping network.
- Preventing Contamination:
- In applications where the end of a pipe needs to be sealed to prevent contamination or environmental exposure, blind flanges are the preferred choice.
- Easy Installation and Removal:
- Blind flanges are easy to install and remove, making them practical for temporary closures or situations where frequent access to the interior of the system is necessary.
- Versatility in Materials:
- Blind flanges can be manufactured from a variety of materials, offering versatility to meet the specific requirements of different industries. Common materials include carbon steel, stainless steel, and alloy steel.
- Bolted Connection:
- The bolted connection of blind flanges ensures a secure and leak-resistant closure. The number and size of bolts depend on the flange size and the pressure rating of the system
Applications:
Crucial in scenarios where the termination of a pipe needs to be securely sealed, such as in water treatment plants and chemical processing facilities.
Blind flanges play a crucial role in maintaining the integrity and safety of piping systems by providing a reliable and leak-proof closure. Yanhao’s commitment to quality ensures that blind flanges produced meet the highest industry standards, offering dependable solutions for a wide range of applications.The diversity in stainless steel flange types caters to the intricate needs of various industries. Yanhao, as a stalwart in stainless steel manufacturing, ensures that each flange, be it weld neck, slip-on, socket weld, threaded, or blind, meets and exceeds stringent industry standards. Explore our range to discover the epitome of precision and reliability in stainless steel flanges for your specific applications.
Author: Lewis Liu
Hello, my name is Lewis Liu, and I’m a professional sales engineer with over a decade of expertise in the flange fittings sector.
I am quite informed about flange selection, installation, and maintenance. I am passionate about providing customers with the greatest solutions for keeping their pipeline systems running smoothly, safely, and dependably.
If you have any queries or concerns concerning flange fittings for your pipelines, whether they are about selection, material choice, specification requirements, or anything else, please contact me at any time. I am dedicated to providing expert advice and assistance to help you make educated decisions and reach your objectives.
