Exploring the Distinctions: Flat Welding Flanges vs. Butt Welding Flanges
In the realm of industrial applications, welding flanges play a pivotal role in ensuring the integrity and functionality of various systems. As we delve into the intricate details of these essential components, it becomes apparent that not all flanges are created equal. Welcome to our exploration of the nuanced disparities between flat welding flanges and butt welding flanges – a journey that goes beyond mere surface distinctions.
Understanding these differences is not merely an academic exercise; it is a strategic imperative for professionals and industries worldwide. The choices made in selecting the right type of welding flange can significantly impact performance, durability, and overall project success. In this discourse, we aim to unravel the complexities surrounding flat welding flanges and butt welding flanges, offering a comprehensive guide for informed decision-making.
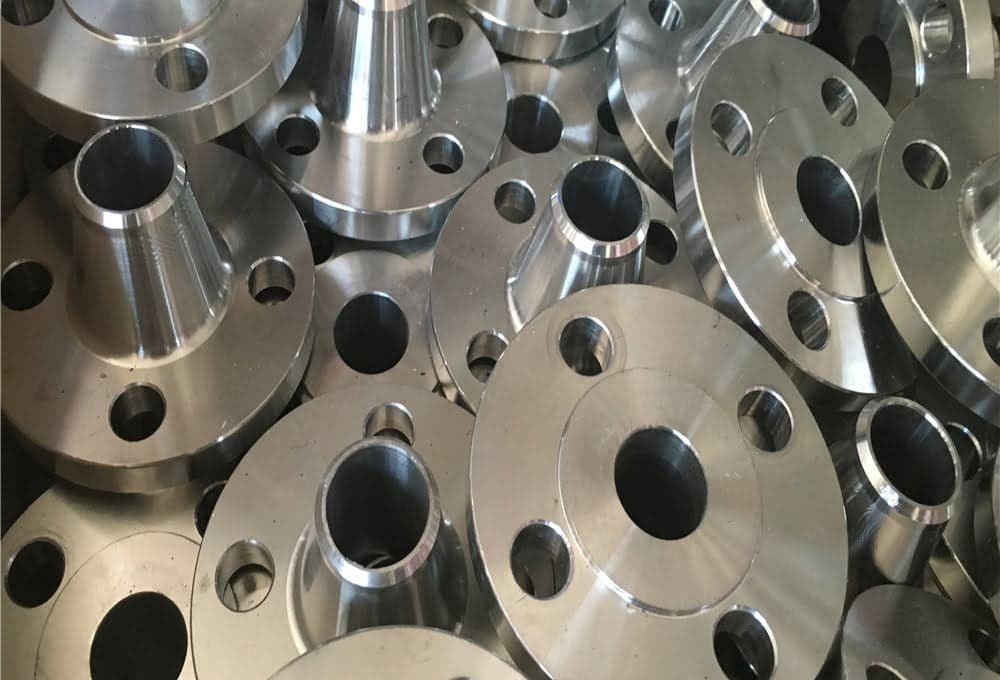
At the heart of this exploration lies YANHAO’s unwavering commitment to quality and expertise. As a company deeply rooted in precision engineering, we understand the critical role that welding flanges play in the seamless operation of industrial systems. Our dedication to delivering high-quality solutions underscores our reputation as a trusted partner in the industry.
Join us on this journey as we navigate through the external appearances, structural designs, connection methods, application scopes, cost considerations, and installation procedures of these two distinct types of welding flanges. Through a lens of professionalism, expertise, and authority, this blog aims to empower our readers with the knowledge necessary to make informed decisions in the complex landscape of welding flanges.
I.External Appearance
A. Flat Welding Flanges
Flat welding flanges, characterized by their sleek and uniform surface, present a distinct appearance in the realm of welding components. These flanges boast a flat face without any protrusions, providing a seamless integration into pipelines or equipment. Their design emphasizes a flush connection, offering a streamlined look and facilitating easy access for maintenance or inspection purposes.
Flat welding flanges typically exhibit a smooth and even surface finish, contributing to their aesthetic appeal. Their clean lines and unobtrusive profile often make them a preferred choice in industries where a neat and visually pleasing finish is desired.
B. Butt Welding Flanges
In contrast, butt welding flanges showcase a different visual profile owing to their raised ring or collar, which surrounds the pipe joint. This raised portion or shoulder serves a critical purpose in providing additional strength to the joint, ensuring a secure and robust connection. The protruding ring distinguishes butt welding flanges from their flat counterparts, adding a distinct feature to their appearance.
The design of butt welding flanges, although not as sleek as flat welding flanges, offers an advantage in terms of structural reinforcement. This design variation is instrumental in applications that demand enhanced joint integrity and resistance to high-pressure environments.
C. Visual Distinctions and Aesthetic Considerations
The visual disparities between flat welding flanges and butt welding flanges extend beyond their surface textures. While flat welding flanges exude a seamless, modern appearance, butt welding flanges convey a more robust and function-oriented aesthetic due to their raised ring feature.
Aesthetic considerations often play a role in the selection process, with industries balancing functionality and visual appeal. The choice between these two types of flanges not only involves structural and operational factors but also encompasses the desired aesthetic outcome and the overall impression on the system’s appearance.
The decision-making process regarding external appearances of welding flanges involves a careful assessment of the specific requirements of the application, considering both functional and visual aspects to achieve an optimal balance between form and function.
II. Structural Design
A. In-Depth Look at the Structural Features of Flat Welding Flanges
Flat welding flanges are characterized by their simplicity and straightforward structural design. These flanges have a flat face and lack the raised collar found in butt welding flanges. The absence of intricate features contributes to a lighter overall weight, making them a preferred choice in applications where minimizing weight is crucial.
The structural design of flat welding flanges emphasizes ease of installation and accessibility. The absence of a raised portion simplifies alignment during the welding process, promoting a seamless connection. However, it’s essential to note that the flat design may have limitations in high-pressure environments, necessitating careful consideration of application requirements.
B. Comprehensive Examination of the Structural Design of Butt Welding Flanges
Butt welding flanges exhibit a more intricate structural design with a raised ring or collar surrounding the pipe joint. This design imparts additional strength and stability to the joint, making butt welding flanges suitable for applications involving elevated pressures and rigorous operating conditions.
The raised ring in butt welding flanges serves a dual purpose – it reinforces the structural integrity of the joint and provides a stop against which the pipe can be butt-welded, enhancing the overall stability of the connection. This design feature makes butt welding flanges a preferred choice in industries where robustness and reliability are paramount.
C. Impact of Design on Performance and Durability
The structural variances between flat welding flanges and butt welding flanges have a profound impact on their performance and durability in diverse applications. Flat welding flanges, with their straightforward design, excel in scenarios where lightweight construction and ease of installation are priorities. However, their application may be limited in high-pressure or high-temperature environments.
On the other hand, the raised ring in butt welding flanges significantly enhances their performance in demanding conditions. The added structural reinforcement contributes to improved durability and reliability, making them well-suited for applications requiring heightened resistance to pressure, corrosion, or temperature extremes.
Ultimately, the selection between flat welding flanges and butt welding flanges should align with the specific demands of the application. Engineers and industry professionals must carefully evaluate the structural requirements, considering factors such as pressure levels, environmental conditions, and long-term durability to ensure optimal performance and safety.
III.Connection Methods
A. Exploration of Various Connection Methods for Flat Welding Flanges
Flat welding flanges offer versatility in terms of connection methods, providing adaptability to different project requirements. Common connection methods for flat welding flanges include:
- Welding: Flat welding flanges are often welded directly to the pipe or equipment. This welding method ensures a secure and leak-resistant connection. The simplicity of this approach facilitates ease of installation and maintenance.
- Bolting: In some applications, flat welding flanges are connected using bolts. This method allows for quick disassembly and reassembly, making it suitable for systems that require periodic maintenance or modifications.
B. Discussion on Connection Techniques Associated with Butt Welding Flanges
Butt welding flanges, with their raised collar design, employ specific connection techniques tailored to enhance structural integrity. Key connection methods for butt welding flanges include:
- Butt Welding: The primary method involves butt-welding the flange to the pipe. This direct welding creates a robust joint, ensuring a seamless flow of fluids or gases without potential leak points. The raised ring provides additional support during the welding process.
- Socket Welding: Butt welding flanges can also be socket-welded, where the pipe is inserted into the flange’s socket and welded for a secure connection. This method is suitable for smaller pipe sizes and applications with lower pressure requirements.
C. Comparative Analysis of Pros and Cons of Each Connection Method
Flat Welding Flanges:
- Pros:
- Versatile options (welding or bolting) for varied applications.
- Simplicity of installation and maintenance.
- Bolting allows for easy disassembly and reassembly.
- Cons:
- May have limitations in high-pressure applications.
- Welding might require skilled labor for precision.
Butt Welding Flanges:
- Pros:
- Robust and secure joints, suitable for high-pressure environments.
- Enhanced structural integrity due to the raised ring design.
- Butt welding provides a leak-resistant connection.
- Cons:
- Butt welding may be more time-consuming than bolting.
- Socket welding may have limitations for larger pipe sizes.
In selecting the appropriate connection method, the specific needs of the project, including pressure requirements, maintenance considerations, and installation constraints, should guide the decision-making process. Both flat welding flanges and butt welding flanges offer unique advantages, and the choice depends on the application’s demands and operational conditions.
IV.Application Scope
A. Overview of the Industries Where Flat Welding Flanges Excel
Flat welding flanges find their niche in various industries, showcasing versatility and adaptability. Key industries where flat welding flanges excel include:
Petrochemical Industry:
- Commonly used in pipelines for the transport of fluids and gases.
- Versatile connection methods facilitate easy integration into complex systems.
Water Treatment Facilities:
- Suitable for applications involving water distribution and treatment.
- Bolting options allow for straightforward maintenance and system modifications.
HVAC Systems:
- Often utilized in heating, ventilation, and air conditioning systems.
- Simple installation makes flat welding flanges suitable for a range of HVAC applications.
B. Insight into the Specific Applications of Butt Welding Flanges
Butt welding flanges, with their robust design, find specific applications where structural integrity is paramount. These applications include:
Oil and Gas Exploration:
- Butt welding flanges are favored in oil and gas pipelines due to their ability to withstand high pressures.
- Butt welding ensures a secure connection in critical points of the pipeline.
Chemical Processing Plants:
- Chemical industries benefit from the leak-resistant joints provided by butt welding flanges.
- Butt welding ensures the reliability of connections in corrosive environments.
Power Generation Facilities:
- Used in power plants for connecting pipes carrying steam or high-pressure fluids.
- Butt welding flanges contribute to the overall reliability of power generation systems.
C. Consideration of Factors Influencing the Choice of Flange Type for Different Scenarios
The choice between flat welding flanges and butt welding flanges hinges on several critical factors, each influencing the selection for specific scenarios:
Pressure Requirements:
- Flat Welding Flanges: Suitable for moderate pressure applications.
- Butt Welding Flanges: Ideal for high-pressure environments, offering enhanced structural support.
Material Compatibility:
- Consideration of the type of material being transported and its compatibility with the flange material.
Installation Constraints:
- Flat Welding Flanges: Preferred for applications with ease of installation as a priority.
- Butt Welding Flanges: Chosen for applications where the additional time spent on welding is justified by the need for a robust joint.
Maintenance Considerations:
- Flat Welding Flanges: Bolting options facilitate quick and easy maintenance.
- Butt Welding Flanges: Reliable joints may reduce the frequency of maintenance requirements.
Cost Considerations:
- Flat Welding Flanges: Often cost-effective and suitable for applications with budget constraints.
- Butt Welding Flanges: May involve higher upfront costs but offer long-term reliability.
In conclusion, the choice between flat welding flanges and butt welding flanges depends on a careful evaluation of these factors, ensuring that the selected flange type aligns with the specific requirements and operational conditions of the intended application.
V.Cost Analysis
A. Evaluation of the Economic Aspects Related to Flat Welding Flanges
Flat Welding Flanges:
- Material Costs: Flat welding flanges, with their simpler design, often involve lower material costs.
- Installation Costs: The straightforward installation process of flat welding flanges can reduce labor expenses.
- Maintenance Costs: Bolting options facilitate easy maintenance, potentially lowering long-term costs.
- Versatility: The adaptability of flat welding flanges can lead to cost savings in various applications.
B. Cost Considerations Associated with Butt Welding Flanges
Butt Welding Flanges:
- Material Costs: The additional material required for the raised ring design may result in higher material costs.
- Installation Costs: Butt welding may involve more labor-intensive installation, potentially increasing upfront costs.
- Maintenance Costs: The robust design of butt welding flanges may contribute to reduced maintenance requirements, offsetting initial costs.
- Specialized Applications: In industries with stringent requirements, the durability of butt welding flanges can justify higher initial costs.
C. YANHAO’s Commitment to Cost-Effective Solutions Without Compromising Quality
At YANHAO, our commitment to delivering cost-effective solutions is unwavering, underpinned by a dedication to quality and innovation. We prioritize:
- Efficiency in Design: Our engineering expertise focuses on designing welding flanges that optimize material usage without compromising performance, ensuring cost-effectiveness.
- Streamlined Manufacturing: YANHAO employs efficient manufacturing processes, leveraging cutting-edge technologies to enhance productivity and reduce production costs.
- Quality Assurance: While maintaining cost-effectiveness, YANHAO upholds stringent quality control measures. Our products undergo thorough testing to guarantee reliability and longevity, minimizing the total cost of ownership.
- Tailored Solutions: YANHAO collaborates closely with clients to understand their specific needs, offering tailored solutions that strike a balance between cost considerations and performance requirements.
- Long-Term Value: YANHAO’s products are designed for durability, providing long-term value that extends beyond initial costs. Our commitment to quality ensures that our solutions withstand the test of time, contributing to overall cost savings.
In choosing YANHAO as your partner, you can trust in our ability to provide cost-effective welding flange solutions without compromising the high standards of quality and reliability that define our brand.
VI. Installation Procedures
A. Step-by-Step Guide to Installing Flat Welding Flanges
Installation of Flat Welding Flanges:
Preparation:
- Ensure all components are clean and free from contaminants.
- Verify that the flat face of the flange aligns correctly with the mating surface of the pipe.
Alignment:
- Align the bolt holes on the flange with those on the mating flange or equipment.
- Secure the flange in place using temporary fasteners, ensuring proper alignment.
Welding:
- Weld the flat welding flange to the pipe using appropriate welding techniques.
- Follow welding procedures to achieve a strong and leak-resistant joint.
Bolting:
- If bolting is the chosen connection method, insert bolts through the flange holes.
- Tighten bolts evenly in a crisscross pattern to ensure uniform pressure distribution.
Inspection:
- Inspect the completed installation for weld quality and overall integrity.
- Conduct visual checks and, if necessary, non-destructive testing to verify the reliability of the joint.
B. Detailed Installation Procedures for Butt Welding Flanges
Installation of Butt Welding Flanges:
Preparation:
- Cleanse all components thoroughly to eliminate any impurities.
- Confirm the proper alignment of the raised ring with the pipe’s end for butt welding.
Butt Welding:
- Perform butt welding by joining the flange to the pipe, ensuring a secure fit.
- Employ welding techniques suitable for the specific materials involved.
Inspection of Welding:
- Inspect the weld for quality, paying particular attention to the joint’s robustness.
- Conduct necessary testing, such as radiographic examinations, to ensure weld integrity.
Securing Bolts:
- If applicable, secure bolts through the flange holes for additional reinforcement.
- Follow proper bolting procedures, evenly tightening bolts to the specified torque.
Final Inspection:
- Conduct a final inspection of the entire installation to verify the completeness and integrity of the joint.
- Ensure that all safety standards and regulations are adhered to throughout the installation process.
C. Emphasis on Safety Measures and Best Practices
Personal Protective Equipment (PPE):
- Prioritize the use of appropriate PPE, including gloves, safety glasses, and welding helmets, to protect workers during installation.
Ventilation:
- Ensure adequate ventilation in welding areas to disperse fumes and gases, promoting a safe working environment.
Fire Prevention:
- Implement fire prevention measures, such as having fire extinguishers nearby, especially during welding activities.
Training:
- Provide comprehensive training to personnel involved in the installation process, emphasizing proper welding techniques and safety protocols.
Quality Control:
- Incorporate rigorous quality control measures to identify and rectify potential issues during the installation process.
Regulatory Compliance:
- Adhere to local and international safety regulations and standards throughout the installation, promoting a culture of safety and compliance.
By following these step-by-step installation guides and prioritizing safety measures, both flat welding flanges and butt welding flanges can be installed efficiently and securely, ensuring the longevity and reliability of the overall system.
Author: Lewis Liu
Hello, my name is Lewis Liu, and I’m a professional sales engineer with over a decade of expertise in the flange fittings sector.
I am quite informed about flange selection, installation, and maintenance. I am passionate about providing customers with the greatest solutions for keeping their pipeline systems running smoothly, safely, and dependably.
If you have any queries or concerns concerning flange fittings for your pipelines, whether they are about selection, material choice, specification requirements, or anything else, please contact me at any time. I am dedicated to providing expert advice and assistance to help you make educated decisions and reach your objectives.
