What are the applications of carbon steel flanges?
Flanges play a critical role in connecting pipelines and ensuring the safe and leak-free flow of fluids in various industries. Among the different types of flanges available, carbon steel flanges are widely preferred due to their durability, strength, and high-temperature resistance. Hebei Yanhao Pipeline Equipment Co., Ltd. (YANHAO) is a renowned company specializing in the production and supply of high-quality carbon steel flanges. In this blog post, we will delve into the applications of carbon steel flanges, highlighting their advantages and installation maintenance considerations. So, let’s get started and explore the extensive uses of carbon steel flanges and the expertise that YANHAO brings to the table!
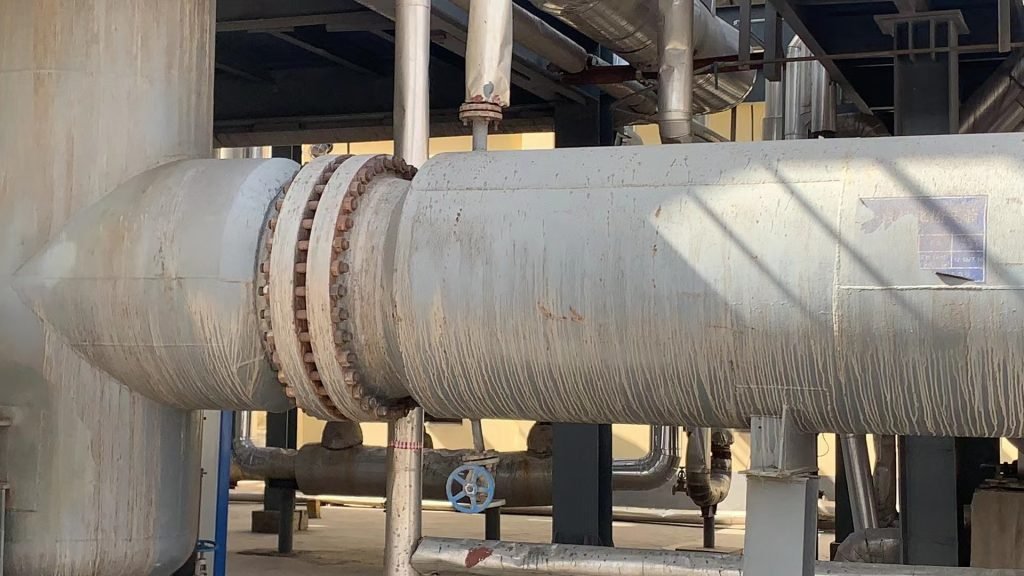
1. Introduction to carbon steel flanges
Carbon steel flanges are essential components used in piping systems to connect pipes, valves, and other equipment. They are typically made from carbon steel, which is an alloy of iron and carbon. Carbon steel is known for its strength, durability, and excellent heat resistance, making it an ideal material for flange manufacturing.
The typical composition of carbon steel flanges includes different grades of steel with varying carbon content. Lower carbon content allows for higher ductility and ease of welding, while higher carbon content provides increased strength and hardness. The carbon content can range from 0.05% to 2.1%, depending on the specific grade and application requirements.
One of the key properties of carbon steel flanges is their robustness and resistance to deformation and corrosion, especially when exposed to high pressures and temperatures. Carbon steel flanges can withstand extreme conditions, making them suitable for a wide range of applications in industries such as oil and gas, petrochemicals, power generation, water treatment, and more.
Furthermore, carbon steel flanges offer excellent compatibility with different types of pipes, fittings, and sealing materials. They can be easily welded, allowing for secure and leak-free connections. Carbon steel flanges also provide flexibility in terms of size, pressure ratings, and configurations, making them highly versatile and adaptable to various piping systems.
In conclusion, carbon steel flanges are crucial components in piping systems, offering strength, durability, and resistance to high temperatures. Their compatibility, weldability, and broad range of applications make them an essential choice for industries requiring reliable and long-lasting pipeline connections.
2. Industrial applications
Carbon steel flanges find extensive use in a wide range of industries due to their durability, strength, and high-temperature resistance. Let’s explore some of the key industries where carbon steel flanges play a crucial role:
- Oil and Gas Industry: In the oil and gas industry, carbon steel flanges are essential components for connecting pipelines, valves, and equipment. They ensure the safe and efficient transportation of crude oil, natural gas, and refined products. Carbon steel flanges are used in offshore platforms, refineries, pipelines, and storage facilities, where they handle high pressures and temperatures while resisting corrosion from aggressive fluids.
- Petrochemical Industry: The petrochemical industry relies on carbon steel flanges to connect various processing units, such as distillation columns, heat exchangers, and reactors. Carbon steel flanges are vital in maintaining the integrity and reliability of the intricate and high-pressure piping systems used in petrochemical plants.
- Chemical Industry: Carbon steel flanges are extensively used in chemical plants where they facilitate the safe transport of various chemicals. They withstand corrosive environments, ensuring leak-free connections and preventing accidents. Carbon steel flanges are commonly found in chemical reactors, storage tanks, and other equipment used in the production of chemicals.
- Power Generation: Carbon steel flanges play a critical role in power generation facilities, including thermal power plants, nuclear power plants, and renewable energy installations. They connect pipes, valves, turbines, and other equipment, ensuring the efficient flow of steam, water, and other fluids. Carbon steel flanges are specifically designed to handle high-pressure steam and withstand extreme temperatures.
- Water Treatment: In water treatment plants, carbon steel flanges are used for the transportation of water, chemicals, and wastewater. They are crucial components in pumps, valves, and filtration systems, contributing to the overall reliability and efficiency of water treatment processes.
Apart from these industries, carbon steel flanges are also utilized in sectors like construction, shipbuilding, mining, and HVAC (Heating, Ventilation, and Air Conditioning). Their versatile nature and compatibility with various materials and systems make them indispensable in ensuring safe and efficient operations across different industrial sectors.

3. Types of carbon steel flanges
There are various types of carbon steel flanges available in the market, each designed for specific applications and installation requirements. Let’s explore some of the most common types:
- Slip-on Flanges: Slip-on flanges are the most popular and widely used type of carbon steel flanges. They have a bore slightly larger than the outer diameter of the pipe, allowing the pipe to slip into the flange. Slip-on flanges are easy to align, providing a low-cost and secure connection. They are commonly used in low-pressure and non-critical applications in industries such as water treatment, HVAC, and general plumbing.
- Weld Neck Flanges: Weld neck flanges are ideal for high-pressure and high-temperature applications. They have a long tapered neck, which is welded to the pipe, providing excellent structural strength and integrity. Weld neck flanges offer better flow characteristics and reduce turbulence in pipelines. They are commonly used in industries such as oil and gas, petrochemical, and power generation.
- Blind Flanges: Blind flanges are solid discs with no center bore, used to seal the end of a piping system. They are typically used in applications where the pipeline needs to be closed off or temporarily blocked. Blind flanges are commonly used in industries such as oil and gas, chemical processing, and water treatment.
- Socket Weld Flanges: Socket weld flanges are designed with a socket-like end that fits over the pipe, allowing for easy alignment and welding. They provide a reliable and leak-free connection and are suitable for small-diameter, high-pressure piping systems. Socket weld flanges are commonly used in industries such as oil and gas, petrochemical, and power generation.
- Threaded Flanges: Threaded flanges have a threaded bore, allowing them to be screwed onto the pipe. They provide a secure and easy-to-assemble connection without the need for welding. Threaded flanges are commonly used in low-pressure applications where disassembly and reassembly are required. They are commonly used in industries such as plumbing, water treatment, and fire protection systems.
These are just a few examples of the types of carbon steel flanges available. Each type offers specific advantages and is suitable for different scenarios or industries based on factors such as pressure, temperature, and installation requirements. It is important to consider the specific needs of your application and consult with industry experts to select the appropriate type of carbon steel flange for your project.
4. Advantages of carbon steel flanges
- Strength and Durability: Carbon steel flanges offer exceptional strength and durability, making them suitable for various high-pressure and high-temperature applications. They can withstand heavy loads and provide structural stability, ensuring long-term performance and reliability.
- Temperature and Pressure Resistance: Carbon steel flanges have excellent temperature and pressure resistance. They can withstand extreme temperatures and high-pressure conditions without deformation or failure. This makes them ideal for industries such as oil and gas, petrochemical, and power generation, where the operating conditions can be harsh.
- Corrosion Resistance: Carbon steel flanges are highly resistant to corrosion, especially when compared to materials like cast iron. They can withstand exposure to aggressive fluids, chemicals, and humid environments, making them suitable for industries like chemical processing, water treatment, and offshore applications.
- Cost-effectiveness: Carbon steel flanges are relatively more cost-effective compared to materials like stainless steel or exotic alloys. They offer a good balance of price and performance, making them a cost-efficient choice for many applications. This affordability factor is particularly important for industries operating on tight budgets or where large quantities of flanges are needed.
- Easy Availability: Carbon steel flanges are widely available in the market, making them easily accessible for various projects and industries. They come in various sizes, types, and pressure ratings, ensuring that suitable options can be found for specific requirements. Easy availability helps in reducing lead time and ensures uninterrupted operations.
- Compatibility: Carbon steel flanges can be easily matched with pipes and fittings of the same material. They offer good compatibility with diverse systems in various industries. This compatibility simplifies installation and maintenance processes while ensuring a reliable and leak-free connection.
Due to these advantages, carbon steel flanges are extensively used across a wide range of industries, including oil and gas, petrochemical, chemical processing, power generation, water treatment, and many others.

5. Special considerations
Special considerations when using carbon steel flanges:
- Corrosion Resistance: While carbon steel flanges offer good corrosion resistance, they are not as resistant as stainless steel or other corrosion-resistant materials. It is important to consider the operating environment and the type of fluids or chemicals that will come into contact with the flanges. Corrosion mitigation strategies such as coatings or cathodic protection may be required in aggressive environments.
- Compatibility with other materials: Carbon steel flanges should be chosen with compatibility in mind. It is important to consider the materials of the pipes and fittings that will be connected to the flanges. Dissimilar metals in contact can lead to galvanic corrosion, compromising the integrity of the connection. Proper insulation or the use of appropriate gaskets can help mitigate this issue.
- Welding considerations: Carbon steel flanges can be easily welded to the pipes, but welding may have an impact on their properties. Heat-affected zones (HAZ) created during the welding process can alter the mechanical properties of the flanges. Proper welding techniques, including the use of qualified welders and suitable welding procedures, should be employed to ensure the integrity and strength of the connection.
- Temperature limitations: While carbon steel flanges offer good temperature resistance, they may have limitations at extremely high temperatures. For applications that require exposure to very high or cryogenic temperatures, alternative materials like stainless steel or specialized alloys may be more suitable.
- Maintenance: Like any other material, carbon steel flanges require regular inspection and maintenance to ensure their continued performance. Routine inspections for signs of wear, corrosion, or damage should be carried out to identify any potential issues and take corrective measures promptly.
It is crucial to consider these special considerations and consult with professionals or industry experts when selecting and installing carbon steel flanges. By understanding the specific requirements of the application and implementing proper measures, the longevity and performance of carbon steel flanges can be optimized.
6. Installation and maintenance
Proper installation and maintenance are essential for ensuring the longevity and functionality of carbon steel flanges. Here are some guidelines and best practices to follow:
Installation:
- Preparing the flange surfaces: Ensure that the flange surfaces are clean, free from contaminants, and properly prepared. Any dirt, rust, or scale should be removed using appropriate cleaning methods, such as wire brushing or abrasive blasting.
- Proper alignment: Align the flanges accurately before installation to ensure a proper fit. Misalignment can lead to leaks and stress on the flange joints. Use alignment tools and techniques, such as flange alignment pins or spacers, to achieve accurate alignment.
- Gasket selection: Proper gasket selection is crucial for creating a leak-free seal between the flanges. Consider factors such as temperature, pressure, and fluid compatibility when selecting gaskets. Ensure the gasket is properly centered and aligned within the bolt holes before tightening.
- Bolt tightening: Follow the recommended bolt tightening procedure specified by the flange manufacturer. This usually involves tightening the bolts in a specific sequence and applying the appropriate torque. Over-tightening or uneven tightening can result in leaks or flange distortion. Consider using torque wrenches or other appropriate tools for accurate and uniform bolt tightening.
- Welding considerations: If welding is required for the installation, ensure that qualified welders carry out the welding process following appropriate welding procedures. Control the heat input and use suitable filler materials to prevent distortion or damage to the flanges.
Maintenance:
- Regular inspections: Conduct regular inspections of the carbon steel flanges to identify any signs of wear, corrosion, or damage. Look for leaks, cracks, corrosion, loose bolts, or signs of misalignment. Inspect the flange surfaces, gaskets, and bolts for any visible issues.
- Corrosion protection: Apply appropriate coatings or corrosion inhibitors to protect the flange surfaces from corrosion. Regularly monitor the effectiveness of these protective measures and reapply as necessary.
- Gasket replacement: Depending on the application and gasket type, it may be necessary to replace the gaskets periodically. Follow the manufacturer’s recommendations for gasket replacement intervals. Ensure that new gaskets are properly installed and aligned.
- Bolt re-tightening: Over time, the bolts may gradually loosen due to thermal expansion and contraction or other factors. Regularly check the bolt tightness and re-tighten if needed, following the recommended bolt tightening procedure.
- Record keeping: Maintain a record of installation, maintenance, and inspection activities for each carbon steel flange. This record can help track the history of maintenance, identify recurring issues, and facilitate timely and appropriate corrective actions.
Proper installation and regular maintenance in accordance with these guidelines can help maximize the longevity and functionality of carbon steel flanges. It is also important to refer to any specific instructions or recommendations provided by the flange manufacturer.
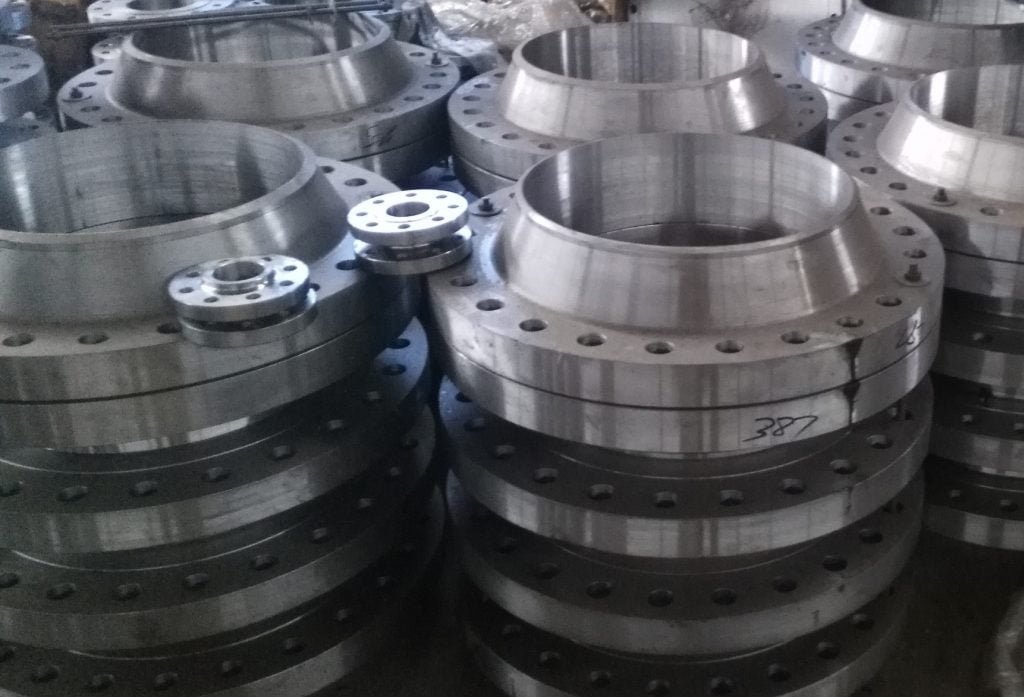
7. Emerging trends and new applications
Emerging trends and new applications for carbon steel flanges:
- Advanced manufacturing technologies: The manufacturing industry is leveraging advanced technologies, such as additive manufacturing (3D printing) and digital design tools, for producing carbon steel flanges with complex geometries and enhanced performance. These technologies allow for more customized designs and improved efficiency in the production process.
- Energy sector: The energy sector, including oil and gas, is a significant user of carbon steel flanges. With the growing demand for renewable energy sources, carbon steel flanges are also finding applications in sectors like wind turbines and solar power plants. These flanges are used for connecting pipelines, mounting structures, and other components in these renewable energy systems.
- Infrastructure development: Carbon steel flanges play a crucial role in the construction and maintenance of foundational infrastructure such as bridges, tunnels, and buildings. As infrastructure development continues to grow worldwide, carbon steel flanges are in high demand for various applications, including pipe connections and structural supports.
- Environmental sustainability: The focus on environmental sustainability is driving the development of carbon steel flanges with improved corrosion resistance and reduced environmental impact. Some innovative coatings and surface treatments are being explored to enhance the corrosion resistance of carbon steel flanges, reducing the need for maintenance and replacement.
- Water and wastewater treatment: Carbon steel flanges are widely used in water and wastewater treatment facilities, where they are employed for connecting pipes, valves, and pumps. With the increasing demand for clean water and efficient wastewater treatment, carbon steel flanges will continue to play a vital role in this sector.
- Offshore and marine applications: Carbon steel flanges are commonly used in offshore oil and gas platforms, floating terminals, and shipbuilding. These flanges are designed to withstand harsh offshore and marine environments, including saltwater corrosion, high pressure, and temperature variations.
- Industrial automation and control: In the era of industrial automation and digitalization, carbon steel flanges are being integrated into smart systems for remote monitoring and control. Embedded sensors and IoT technology can provide real-time information about flange performance, allowing for proactive maintenance and minimizing downtime.
As technology advances and new industries emerge, the applications for carbon steel flanges continue to expand. The ongoing development of materials, manufacturing techniques, and design capabilities will further drive innovation and create opportunities for the use of carbon steel flanges in diverse sectors.
8. Conclusion
In conclusion, carbon steel flanges have a wide range of applications and are crucial components in numerous industries. Emerging trends and advancements in the industry, such as advanced manufacturing technologies, the focus on environmental sustainability, and the integration of carbon steel flanges into smart systems, are driving innovation and expanding the possibilities for their use.
Key takeaways from this discussion include the importance of carbon steel flanges in sectors such as energy, infrastructure, water and wastewater treatment, offshore and marine applications, and industrial automation. These flanges play a critical role in connecting pipes, supporting structures, and ensuring the reliable and efficient operation of various systems.
As the industry continues to evolve, future research and development opportunities lie in further improving the corrosion resistance and durability of carbon steel flanges, exploring new coatings and treatments, and enhancing their performance in extreme conditions.
YANHAO, as a leading provider of carbon steel flanges, is committed to delivering high-quality products that meet the evolving needs of our customers. We are dedicated to continuously improving our manufacturing processes, adopting new technologies, and collaborating with our clients to develop innovative solutions for their specific applications.
Contact us today to learn more about our carbon steel flanges and how we can support your projects.
Author: Lewis Liu
Hello, my name is Lewis Liu, and I’m a professional sales engineer with over a decade of expertise in the flange fittings sector.
I am quite informed about flange selection, installation, and maintenance. I am passionate about providing customers with the greatest solutions for keeping their pipeline systems running smoothly, safely, and dependably.
If you have any queries or concerns concerning flange fittings for your pipelines, whether they are about selection, material choice, specification requirements, or anything else, please contact me at any time. I am dedicated to providing expert advice and assistance to help you make educated decisions and reach your objectives.
